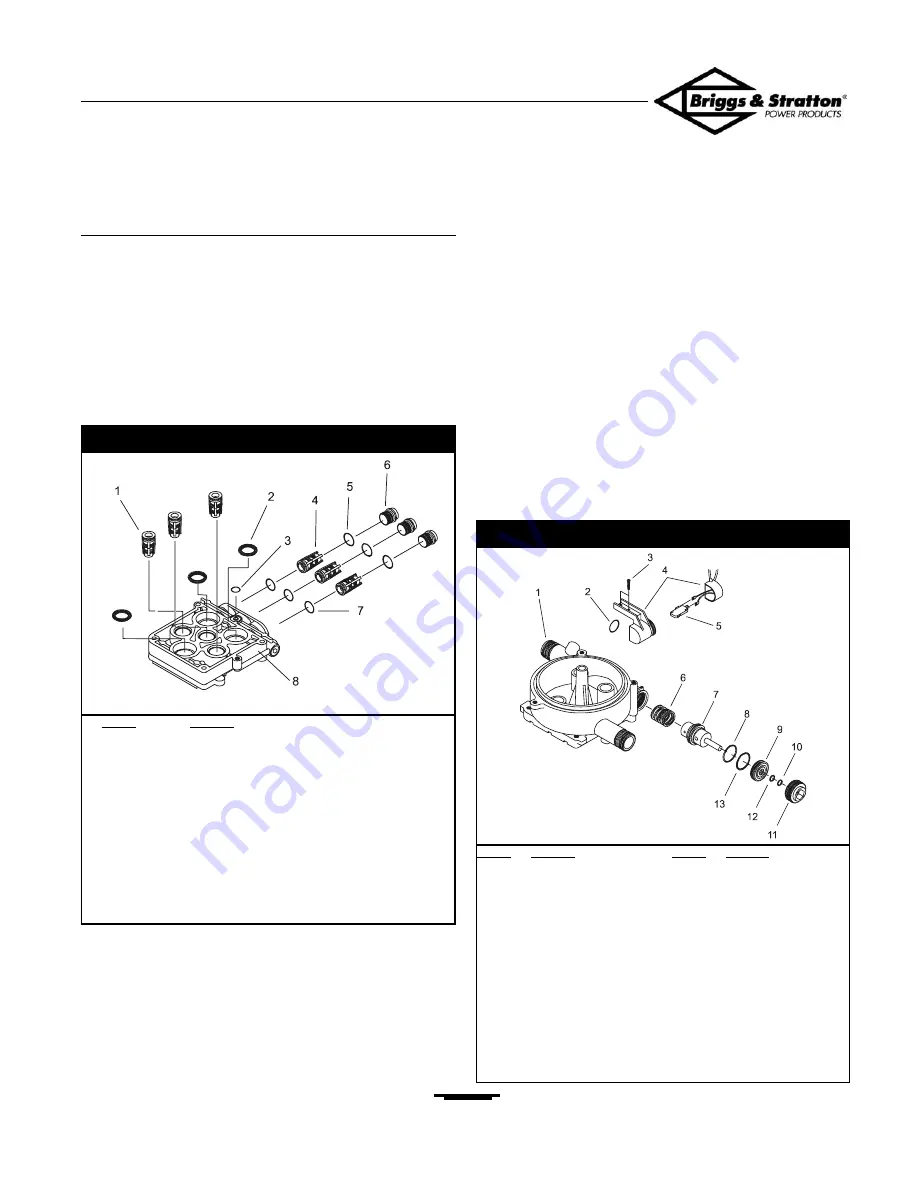
29
Part 4 - Reassembly
Refer to the Torque Specifications provided on the
pump sectional view found at the beginning of this
section when reassembling this product.
Pump Head Assembly
The pop off valve is not serviceable. The entire head
assembly must be replaced if a problem occurs in these
components.
To assemble the pump head, refer to Figure 4.13 for the
following steps:
1. Install three (3) outlet check valve o-rings (item 7). Ensure
they lie flat at the bottom of the cavity.
2. Install three (3) outlet check valves, with large end first
(item 4).
3. Install and snug the three (3) M18-1.5 outlet caps with
pre-installed o-rings (items 5 & 6).
After the pump is assembled, tighten the three (3) outlet
caps to the torque value specified in the Torque Chart,
found on Figure 4.2 (Exploded View) at the beginning of this
chapter.
4. Press three (3) inlet check valves (item 1) into place.
Notice that the small end of the valve goes into the cavity
first, and that the valve is pressed in until it is flush with
the head surface. It may be necessary to pre-lubricate the
check valve o-rings with silicone spray before installation.
5. Pre-lubricate three (3) high pressure water seals (item 2)
with silicone spray. Insert a seal into each piston cylinder
cavity with the flat side facing out. Review Figure 4.11,
seen earlier, for a view of proper seal orientation.
6. Install the pop off valve o-ring (item 3). Petroleum jelly
will help to hold it in place.
Auto Start Switch Assembly
Refer to Figure 4.14 for this assembly.
Section 4 • Small Frame Electric Pump
Portable Pressure Washer Familiarization and Troubleshooting Guide
Item
Name
1
Inlet check valve assembly
2
High pressure water seal
3
Pop off valve o-ring
4
Outlet check valve assembly
5
Outlet port cap o-ring
6
Outlet port cap
7
Check valve o-ring
8
Pump head
Item
Name
1
Piston housing
2
Rubber diaphragm
3
Taptite screw
4
Auto switch
housing
5
Auto switch
6
Auto switch piston
spring
7
Auto switch piston
assembly
Item
Name
8
O-ring
9
Auto switch piston
return stop
10
Backup ring
11
Retainer cap
12
O-ring
13
Backup ring
Figure 4.13 — Pump Head
Figure 4.14 — Auto Start Switch