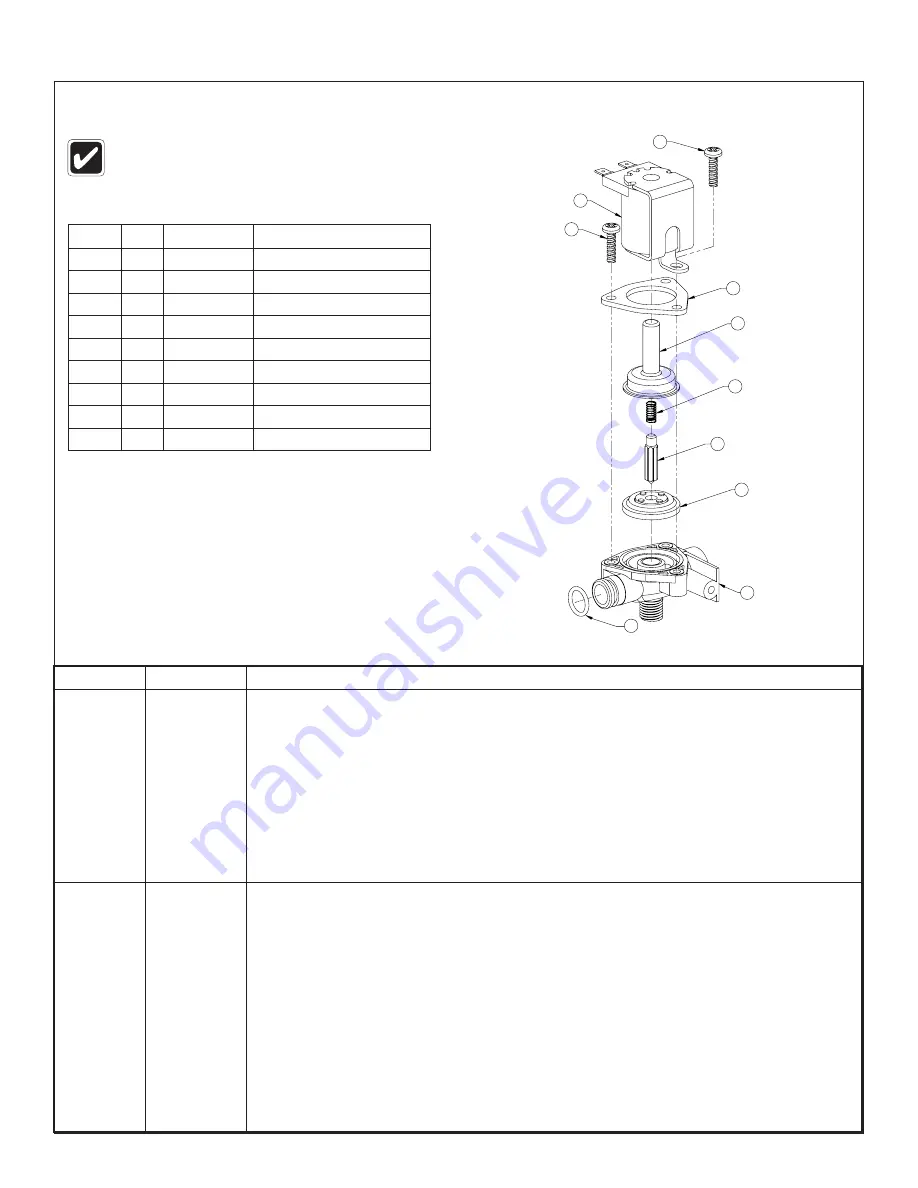
Installation
TDB3105
Bradley • 215-1563 Rev. E; ECN 12-00-004
1/15/2013
21
Solenoid Valve S07-069 (closed body)
Problem
Cause
Solution
An individual
operating
station fails
to shut off
and drips.
Debris is
trapped
between the
diaphragm
and the valve
seat.
Remove debris between diaphragm and the valve seat.
1. Remove the three #8 Phillips-head screws that hold the solenoid valve assembly together. Be
careful not to lose the armature or spring.
2. Remove the diaphragm. Remove any particles that have been trapped between the
diaphragm and the valve seat. Rinse off the diaphragm and inspect for damage. Make sure
the center orifice and both small side orifices are open.
3. Reassemble in reverse order (do not overtighten the Phillips-head screws or the plastic valve
body may crack). Tighten until the armature plate makes contact with the plastic body.
4. Reconnect the wiring.
An individual
operating
station fails
to turn on.
A failed coil for
the valve or
loose electrical
connection to
the terminal.
Test the station to determine the cause.
1. Disconnect the wires from the coil of an adjacent valve. Disconnect the wires from the
problem valve and reconnect to the adjacent valve.
2. Turn on electrical and water supplies to the unit. Pass your hand in front of the sensor of the
problem station, and the adjacent station should turn on.
If the adjacent station turns on and cycles normally, replace the coil on the problem valve.
If the adjacent valve fails to turn on, inspect the wires from the sensor cable and do the following:
•
make sure there are no breaks and that the fully insulated disconnect terminals are firmly
crimped in place;
•
turn off the electrical and water supplies;
•
reconnect to the adjacent valve and turn on the water supplies to the unit;
•
pass your hand in front of the sensor. If the station still fails to turn on, replace the sensor.
Item
Qty.
Part No.
Description
1
1
118-308
Valve Body, 5/16" Closed
2
1
269-983
Diaphragm
3
1
269-577
Armature
4
1
269-578
Spring
5
1
269-1729
Armature Housing
6
1
269-1730
Clamp, Armature Housing
7
1
269-1797
Coil, Solenoid Valve
8
3
160-447
Screw, #8 x 5/8"
9
1
125-165
O-ring, #2-013
Turn off water supplies to the unit before
troubleshooting.
1
2
3
4
5
6
7
8
9
8