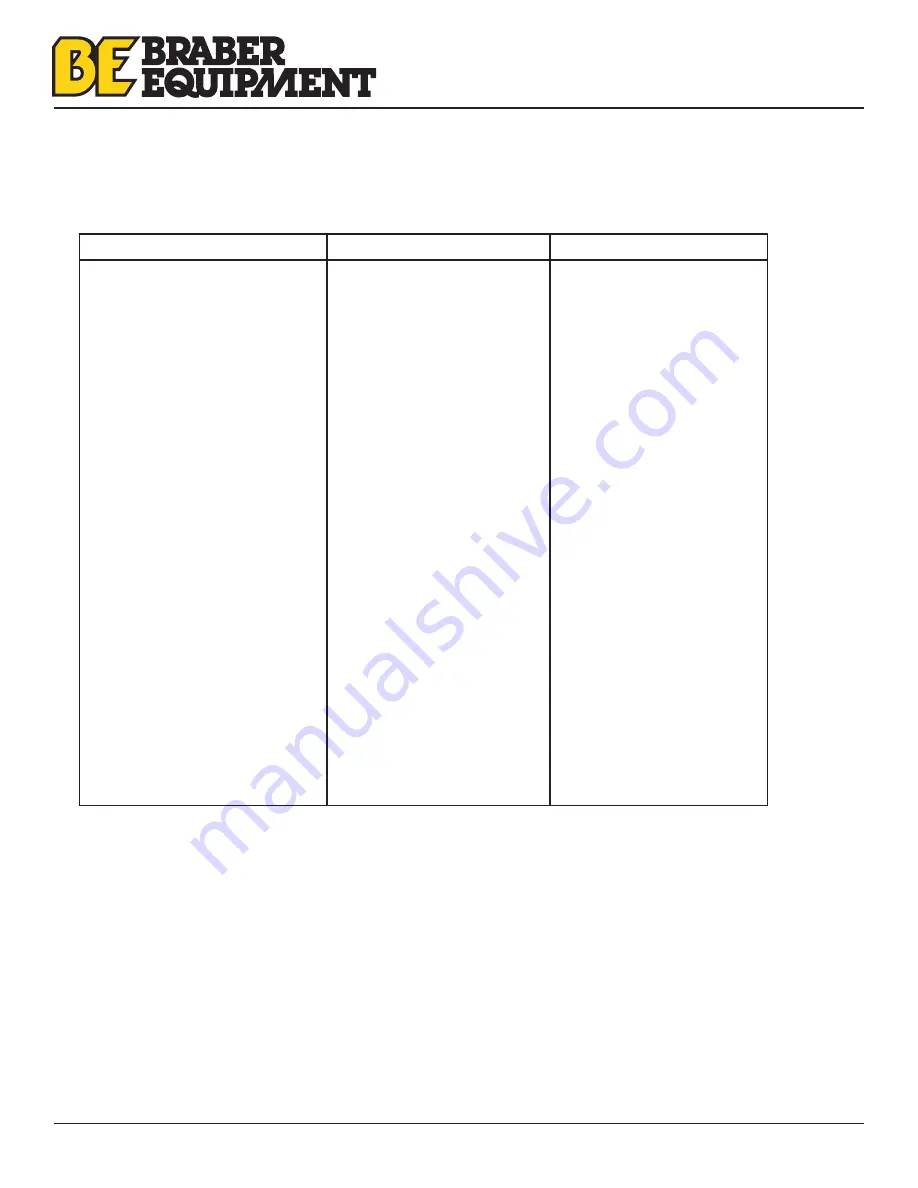
54
BE-WC92S/R
Drive System
Engine
Chipper capacity
Chipper Housing Opening
Rotor Size
Number of Rotor Knives
Knife Type Rotor Weight
Feeding System
Dimensions (hopper folded) Hopper
Opening
Discharge Hood Rotation Discharge
Hood Height
Rated RPM
Weight
Direct drive, pto w/shearbolt n/a
10” diameter, (up to 14” slab)
10 1/2” x 14”
36”
4/offset
Hardened Tool Steel
280 lbs
Self or Hydraulic
BE-WC92S/RS - 54” W x 52”
x 88” H
25” x 25”
360
84”
540
BE-WC92S/RS-1000lbs/BE-
WC92S/RR-1375lbs
BE-WC92S/RR- 64” W x 68”
L x 88” L
7
SPECIFICATIONS
7. 1 MECHANICAL
SPECIFICATIONS SUBJECT TO CHANGE WITHOUT NOTICE