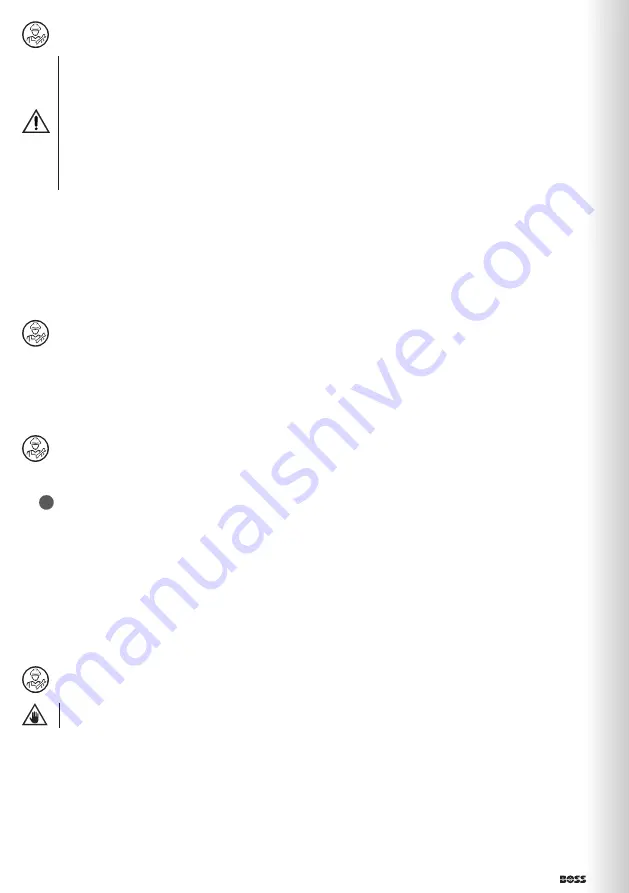
7
EN
4.0 - FIRST START-UP
Before commissioning, verify that:
• all of the instructions on the rating plate, including the direction of flow, are observed;
• the holes of the dust cap (
6
) are not clogged.
• IMPORTANT:
The leak test of the piping must be performed while avoiding to subject the membrane of the
regulator (therefore, the downstream pipe section) to a pressure higher than 300 mbar. Use special manual gas
closing devices to prevent damaging the regulator;
• The pressurisation manoeuvre of the equipment must be carried out very slowly so as to avoid possible damage.
NOTE:
under no circumstances should a blind cap be placed instead of the dust cap (
6
) as the regulator may
not work;
• Open the downstream vent valve partially;
• Slowly open the upstream shut-off devices (e.g. solenoid valves, OPSO shut-off valve, etc.);
• Wait until the downstream pressure stabilises at the calibration value P2 of the spring (indicated on the plate);
• Close the vent valve;
• Check the tightness of all the system gaskets and check the internal/external tightness of the regulator;
• Open the downstream shut-off valve very slowly;
• Check the operation of the regulator.
4.1 - RECOMMENDED PERIODIC CHECKS
• Use a suitable calibration tool to ensure the bolts are tightened as indicated in 3.2;
• Check the tightness of the flanged/threaded connections on the system;
• Check the tightness and operation of the regulator;
It is the responsibility of the final user or installer to define the frequency of these checks based on the severity of the service
conditions.
4.2 - ADJUSTING THE OUTLET PRESSURE
Before starting the system, make sure that the spring supplied with the regulator is suitable for the desired adjustment
pressure. The outlet pressure P2 (unless specifically requested) is factory set with the top cover (
4
) positioned as shown in
3.2
a
and with the adjustment screw (
2
) set approximately at the minimum calibration value.
If the regulator is installed in different positions, check and reset the outlet pressure P2.
Adjust the outlet pressure as follows:
• Unscrew the cap (
1
);
• Unscrew the adjustment screw (
2
) and set it to the minimum calibration allowed (threaded end of the top cover (
4
));
• Start the system or make sure there is a minimum flow downstream of the regulator;
• To increase the pressure calibration downstream of the regulator, tighten the adjustment screw (
2
) to the desired value.
Perform the reading with a calibrated pressure gauge, installed downstream of the regulator to at least 5 DN (see example in 3.4);
• Screw the cap (
1
) back on and if necessary, seal it in that position using the appropriate seal holes (if present);
• Use pressure outlets (
13
) on the device only for zero flow or very low flow measurements.
4.3 - REPLACING THE SPRING
The step must be carried out without gas inside the regulator.
Replace the spring as follows:
• Unscrew and remove the cap (
1
) from the top cover (
4
);
• Completely loosen and take out the adjustment screw (
2
);
• Remove the spring washer (
26
);
• Remove the spring (
3
) from the top cover (
4
) and replace it with the new spring;
• Place the washer (
26
) on the new spring once again;
• Tighten the adjustment screw (
2
) and after starting the system as shown in 4.0, set the outlet pressure to the desired value
as shown in 4.2;
• Screw the cap (
1
) back on and if necessary, seal it in that position using the appropriate seal holes (if present);