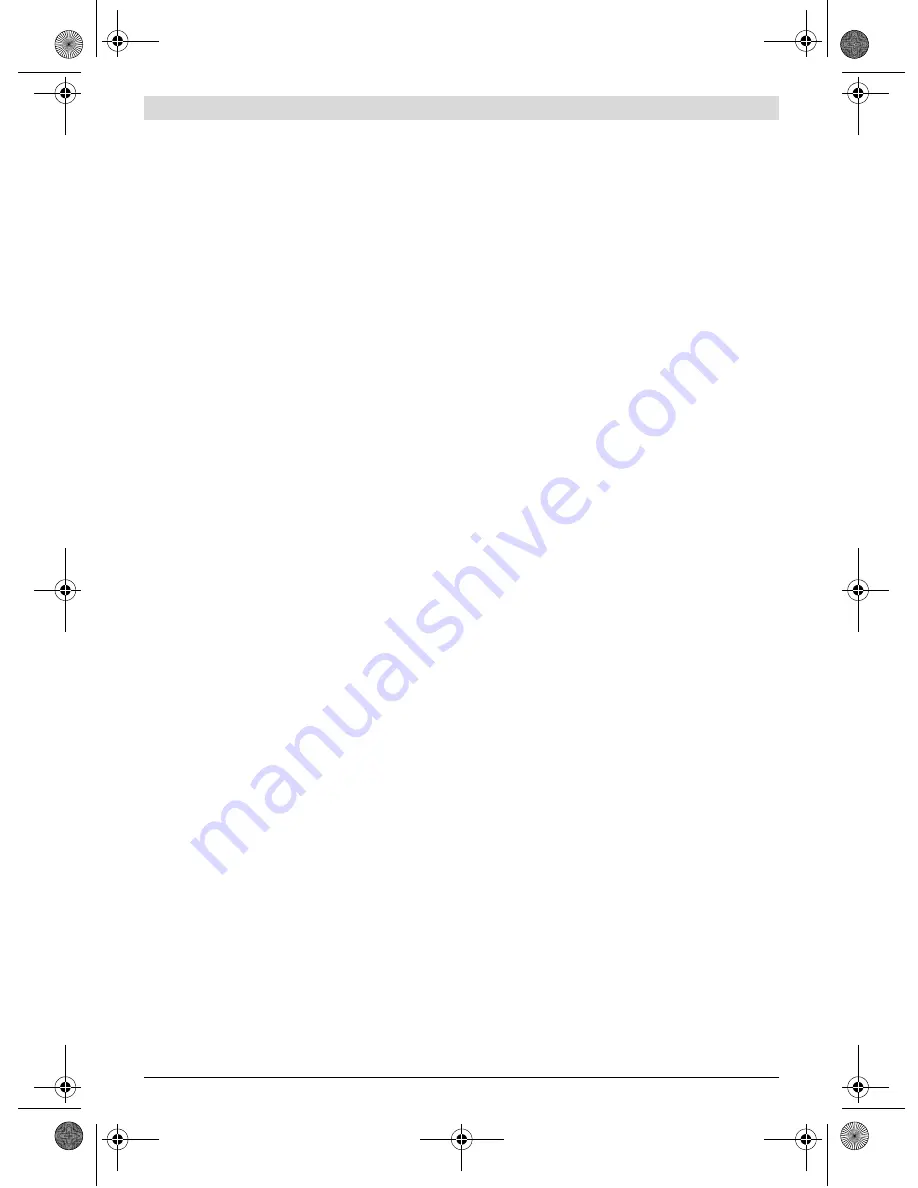
English |
23
Bosch Power Tools
1 619 929 J34 | (18.7.11)
Checking and Adjusting the Basic Adjustment
To ensure precise cuts, the basic adjustment of the machine
must be checked and adjusted as necessary after intensive
use.
A certain level of experience and appropriate specialty tools
are required for this.
A Bosch after-sales service station will handle this mainte-
nance task quickly and reliably.
Setting the Stops for Standard 0°/ 45° Bevel Angles
– Bring the power tool into the working position.
– Adjust to a 0° bevel angle.
– Tilt the blade guard
6
toward the rear to the stop.
Checking:
(see figure T1)
– Set an angle gauge to 90° and place it on the saw table
8
.
The leg of the angle gauge must be flush with the saw blade
27
over the complete length.
Adjusting:
(see figure T2)
– Loosen screw
55
.
The 0° stop
56
can now be moved.
– Loosen locking lever
19
.
– Move handwheel
20
toward the 0° stop until the leg of the
angle gauge is flush with the saw blade over the complete
length.
– Hold the handwheel in this position and tighten locking le-
ver
19
again.
– Tighten screw
55
again.
When the angle indicator
49
is not in line with the 0° mark of
scale
50
, loosen screw
57
with a commercially available Phil-
lips screwdriver and align the angle indicator alongside the 0°
mark.
Repeat the above mentioned worksteps accordingly for the
45° bevel angle (loosening screw
58
; moving the 45° stop
59
). In this, the angle indicator
49
must not be misadjusted.
Parallelism of the Saw Blade to the Guide Grooves of the
Angle Stop (see figure U)
– Bring the power tool into the working position.
– Tilt the blade guard
6
toward the rear to the stop.
Checking:
– With a pencil, mark the first visible saw tooth on the left
side that projects above the insert plate.
– Set an angle gauge to 90° and place it on the edge of the
guide groove
5
.
– Move the leg of the angle gauge until it touches the marked
saw tooth, and read the clearance between saw blade and
guide groove.
– Turn the saw blade until the marked tooth projects above
the right side of the insert plate.
– Move the angle gauge alongside the guide groove to the
marked tooth.
– Measure the clearance between the saw blade and guide
groove again.
Both clearances measured must be identical.
Adjusting:
– Loosen Allen screws
60
at the front below the saw table
and Allen screws
61
at the rear below the saw table with
the supplied Allen key
14
.
– Carefully move the saw blade until it is parallel to guide
groove
5
.
– Retighten all screws
60
and
61
again.
Adjusting the Saw Table’s Clearance Indicator
(see figure V)
– Position the parallel guide on the right side of the saw
blade.
Move the parallel guide until the mark in the lens
28
indi-
cates 26 cm on the bottom scale.
To lock the parallel guide, press clamping handle
36
down
again.
– Loosen tensioning lever
17
and pull the table extension out
to the stop.
Checking:
On the upper scale
1
, clearance indicator
53
must indicate
the identical value as the mark in lens
28
on the bottom scale
1
.
Adjusting:
– Loosen screw
62
with a Phillips screwdriver and align
clearance indicator
53
alongside the 26 cm mark of the up-
per scale
1
.
Adjusting the Lens of the Parallel Guide (see figure W)
– Bring the power tool into the working position.
– Tilt the blade guard
6
toward the rear to the stop.
– Move parallel guide
9
from the right until it touches the saw
blade.
Checking:
The mark of lens
28
must be in a line with the 0° mark of scale
1
.
Adjusting:
– Loosen screw
63
using a Phillips screwdriver and align the
clearance indicator alongside the 0° mark.
Adjusting the Level of the Insert Plate (see figure X)
Checking:
The front side of the insert plate
24
must be flush with or
somewhat lower than the saw table; the rear side must be
flush with or somewhat above the saw table.
Adjusting:
– Remove the insert plate
24
.
– Adjust the correct level of the four adjusting screws
64
with the Allen key
65
.
Adjusting the Tension Force of the Parallel Guide
The tensioning force of the parallel guide
9
can decrease after
frequent usage.
– Tighten the adjustment screw
23
until the parallel guide
can be firmly affixed on the saw table again.
Storage and Transport
Storing Product Features (see figures Y1–Y6)
For storage purposes, certain product features can be se-
curely fastened to the power tool.
– Loosen auxiliary parallel guide
38
from parallel guide
9
.
– Attach all loose tool parts to their storage locations on the
housing. (see Table)
OBJ_BUCH-1473-001.book Page 23 Monday, July 18, 2011 10:33 AM