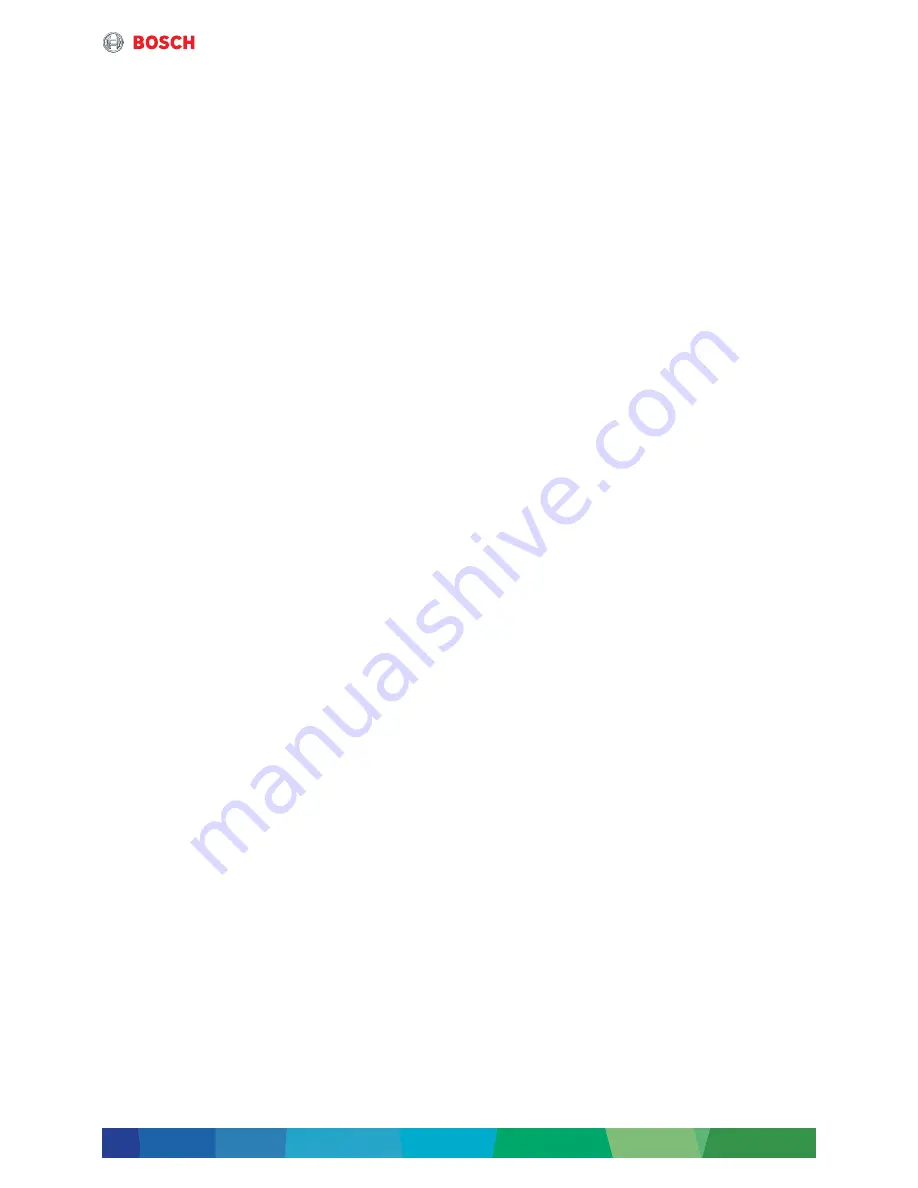
Engineering information and sizing
35
Systemlösung – 6 720 885 509 (2018/03)
Functional description for system hydraulics with
bypass
Priority for designing a CHP, is always the low
temperature side. If the CHP shall be operated, is has to
be ensured that also the waste heat from the motor
coolant circuit on the low temperature level can be used
or that an emergency cooling is integrated in the CHP.
For this purpose, the buffer cylinder has to be
dimensioned such that it has a water volume to assure
at least one hour CHP runtime without interruption.
It has to be determined individually with the customer
for which process the heat from the buffer cylinder can
be used. It can be be integrated in the heating network
or it can be used for make-up water preheating, DHW
heating or for special processes.
The commonly in the CHP integrated flue gas heat
exchanger is superfluous, because the hot flue gas is
used as waste heat for the fourth draught of the steam
boiler. Furthermore, the flue gas components are
adapted to the uncooled flue gas temperatures.
The flue gas first flues through a catalytic converter,
before it attains the primary and secondary silencers.
These serve, besides reducing the flue gas sound
pressure level of the module, as prevention against a
propagation of a possible pulsation of the flue gas to the
fourth draught.
The pneumatic driven flue gas damper combination is
decides whether flue gas is led through the fourth
draught of the steam boiler or passes it.
The bypass has several functions:
If designed for this purpose, at idle state of the steam
boiler, the CHP module can continue to be operated via
bypass if required. For this, it has to be assured that the
heat can be taken from the low temperature side and
that in addition the generated current can be used
efficiently via the German Renewable Energies Law.
In order to bypass the fourth draught, the hot flue is led
directly via the bypass to the chimney. This however
should be no permanent condition, because the bypass
operation has a negative effect on the annual efficiency
of the overall system. This value should not fall below
70 %, because otherwise not CHP subsidy is granted.
The flue gas chimney for the steam boiler solution of the
CHP must be designed for 650 °C (T650) and must be
pressure-tight for at least for 1 bar overpressure.
If the flue gases of the CHP are led through the fourth
draught of the steam boiler, these ensure the generation
a certain amount of steam and thus reduce the
frequency of burner starts and thus protect the burner.
Behind the fourth draught is a flue gas heat exchanger
that uses the residual heat of the flue gas for make-up
water preheating. To prevent evaporation, the
temperature of the make-up water is monitored. The flue
gas can also be led past the flue gas heat exchanger via
a second bypass.
The feed water can be heated via the flue gas heat
exchanger (ECO2) and can be led back to the feed water
container via the feed water control valve with pump
freewheel function if no feed water is required in the
steam boiler.
If feed water is required, it is first heated up by the ECO2
and subsequently by the ECO1 and finally provided for
the steam boiler.
Содержание CHP CE 1200 NE
Страница 43: ...43 Systemlösung 6 720 885 509 2018 03 Notes ...
Страница 44: ...Subject to technical modifications ...