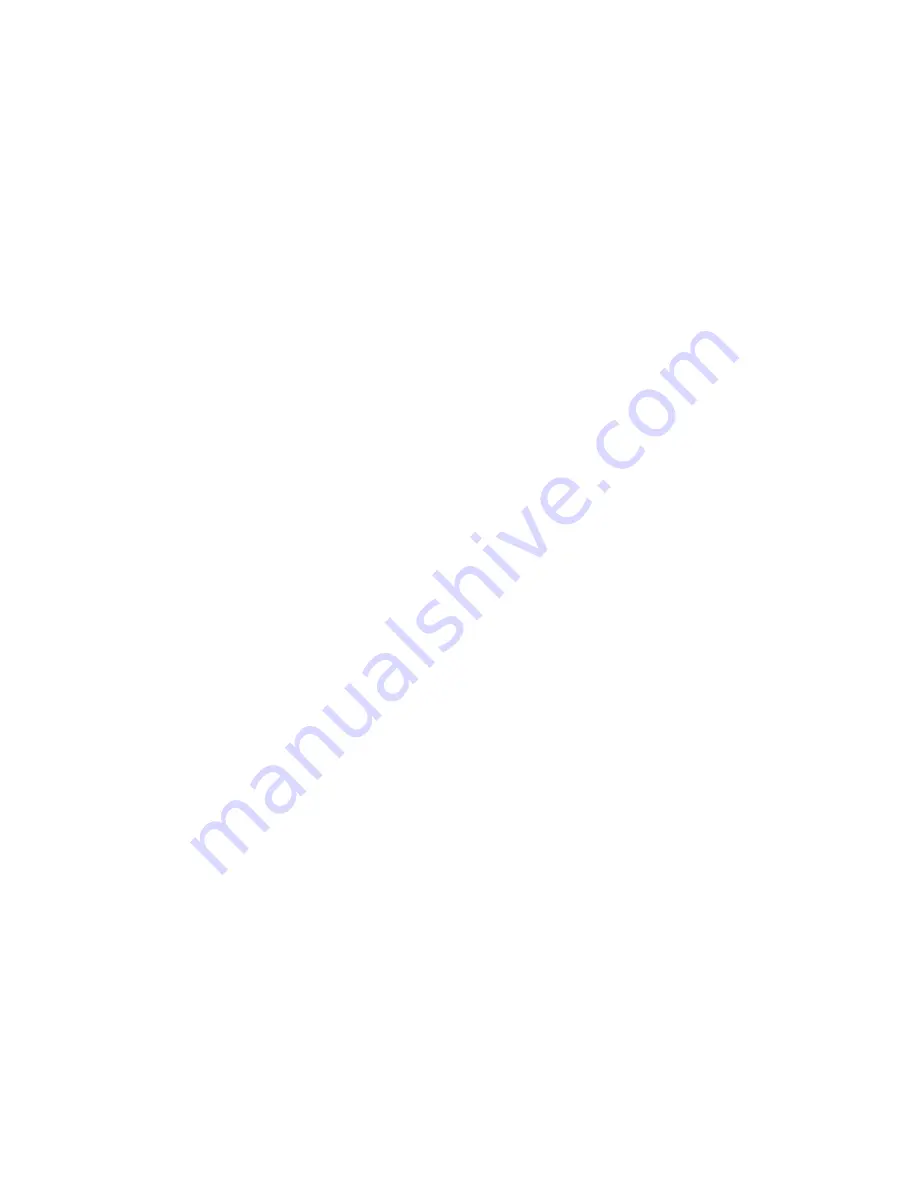
2.6 Electrode Types
A range of well established electrode types are
available for the welding of ferrous materials,
and these are usually classified in the following
groups:
• cellulosic
• rutile
• basic, iron powder,
• others
Cellulosic electrodes contain over 30%
organic material (e.g. cellulose) in the coating.
This decomposes in the arc to generate
hydrogen and carbon dioxide. High arc forces
are formed in the arc and these depress the
weld pool and produce deep penetration
characteristics. The arc force may also be used
to generate a 'keyhole' effect that may be used
to complete single sided root runs, particularly
in pipe. It is usually these types of electrodes
that are use in the "Stovepipe" method of
welding.
Rutile electrodes contain the principal alloying
element titanium dioxide (TiO
2
i.e. rutile).
This addition gives excellent arc stability, low
voltages, low spatter and easily controlled self-
detaching slag. These characteristics make the
rutile electrode the most common general-
purpose electrode type.
Basic (Low Hydrogen) electrodes usually
contain calcium carbonate (CaCO
3
) and
calcium fluoride (CaF
2
). The hydrogen content
of the coating is controlled by the absence of
minerals containing combined water and careful
baking procedures. In general, the arc running
characteristics of these electrodes are inferior
to those of the rutile types described above, but
the mechanical properties of the weld metal are
superior. These electrodes are used on ferritic
steels when resistance to hot and cold cracking
is required.
Iron powder may be added to any of the above
coating types to increase the 'recovery' or the
amount of filler material produced when the
electrode is used. The addition of iron powder
also increases the deposition rate and usually
reduces the arc voltage requirement.
Iron oxide/silicate electrode formulations
may be used for general purpose mild steel
welding in the flat and HV positions but these
types have largely been superseded by rutile
coatings.
In addition to electrodes for plain carbon, low
alloy and high alloy steels a range of surfacing
and non-ferrous alloy electrodes are available.
2.7 Care of Electrodes
The performance of MMA electrodes and
the quality of the resultant weld depend on
the type of electrode and its condition. If the
mineral coating is damaged or chipped, poor
arc stability and inadequate shielding may
result. Most coating materials absorb moisture
if not properly protected and this may result
in deterioration of the coating and hydrogen
pick up in the weld bead. Particular care must
be taken with controlled hydrogen electrodes
that should be stored and if necessary re-dried
according to the manufacturers instructions.
Poor electrode condition will often be indicated
by increased spatter, striking difficulties, weld
bead porosity, and 'harsh' arcing characteristics.
8