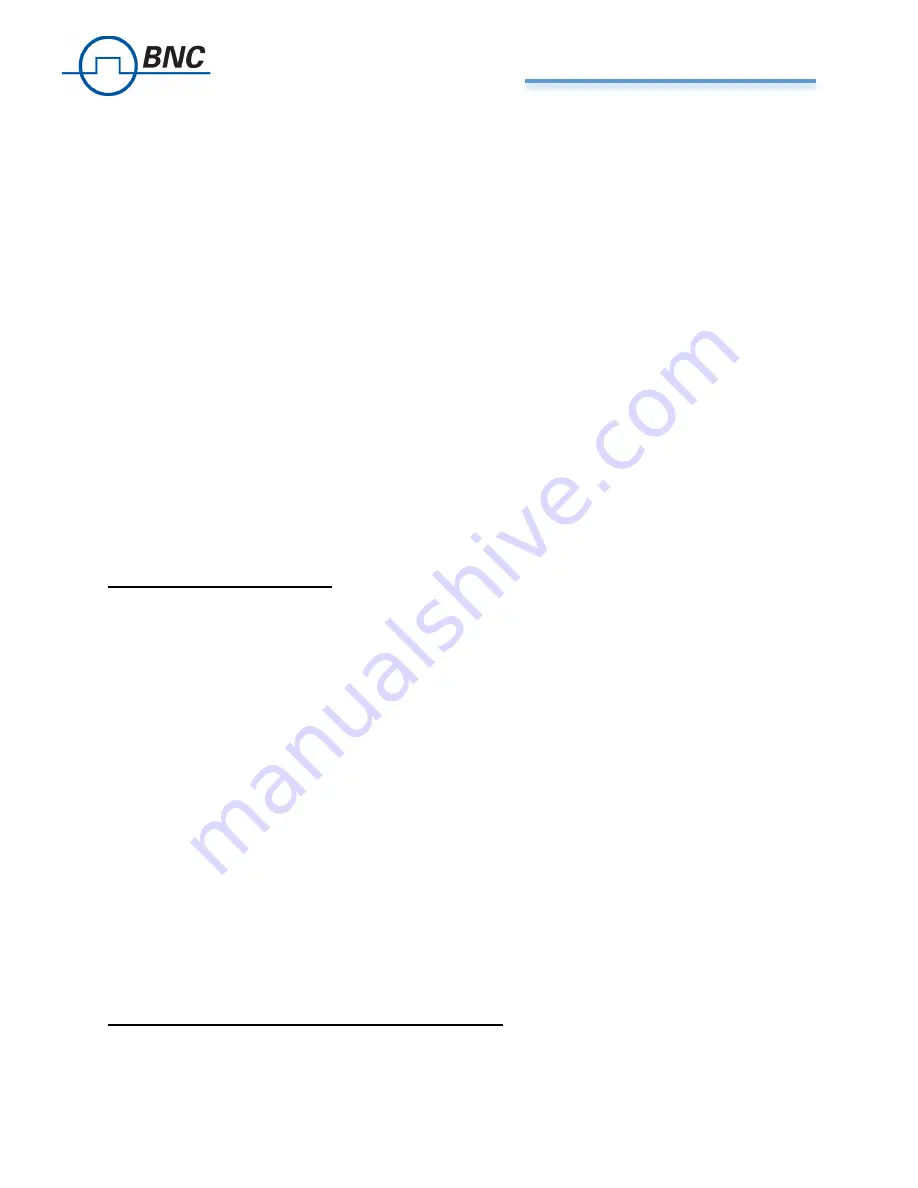
Berkeley Nucleonics Corporation
2955 Kerner Blvd., San Rafael, CA 94901 ° Tel (415) 453 9955 ° Fax (415) 453 9956 ° www.berkeleynucleonics.com
The control signal for the current source is called the “enable” and has thresholds
compatible with TTL logic. The “gate” control has thresholds compatible with
CMOS (CMOS is complementary metal oxide semiconductor) logic.
Very little power is dissipated in the driver until it is enabled. When enabled, at 125
A maximum output approximately 75 W is continuously dissipated in the driver to
maintain the current in the energy storage inductor (see note #1 under
specifications). The load power is added to this continuous power and the pulse
rate will further increase power consumption.
This architecture provides a high-performance driver in a small form factor, with
high operating efficiency and low stored energy. At 125 A output current, the
stored energy in the inductor of the driver is approximately 0.5 s, dramatically
lower than the stored energy in comparable linear current sources.
The PCO-6131 features a user-adjustable variable rise time control. This
innovative feature allows the user to adjust the rise time within a range of <30 ns
to >2.5 µs by means of a PCB-mounted potentiometer, to optimize the driver’s rise
time for the user’s application. In applications in which the laser diode or
interconnection between the driver and the diode is somewhat inductive, the fast
rise time of the PCO-6131 may induce ringing on the leading edge of the pulse.
The rise time may be slowed down using the variable rise time control to minimize
or eliminate this ringing.
3.0 System Requirements
The PCO-6131 requires user-su24 VDC support power, a CMOS (+5 V)
gate signal, and a TTL-level enable/disable signal. The high current output is
derived from the +24 VDC DC input. The output pulse width and frequency are
controlled by the gate signal. The output current amplitude is controlled by a PCB-
mount potentiometer. An optional current monitor, the PCA-9155, output may be
viewed with an oscilloscope, providing a straight-forward means to observe the
diode current waveform in real-time.
To protect the laser diode and the driver, circuitry is incorporated into the driver
that disables the output if the +24 VDC support power drops below 18 V. Clamp
diodes are incorporated into the output network to protect the laser diode against
reverse voltage conditions. The heat sink is monitored for over temperature by a
thermistor. The output cable connection is monitored by a magnetic reed switch.
When the reed switch is not activated, the pulse will be disabled.
Open circuit protection is provided by a 60 Ampere diode connected from the
output to the 24 VDC supply. The user should be aware that even if the output is
an open-circuit, the output current (determined by the current set-point) will flow
into this protection diode. Therefore, care should be taken to ensure the load is
properly connected to the PCO-6131 before pulsing.
4.0 Connector Pinouts And User Adjustments
The support power and control signals are on a 14 pin FCI Connector header, part
number 66429-055. This header mates with an FCI housing, part number 65846-