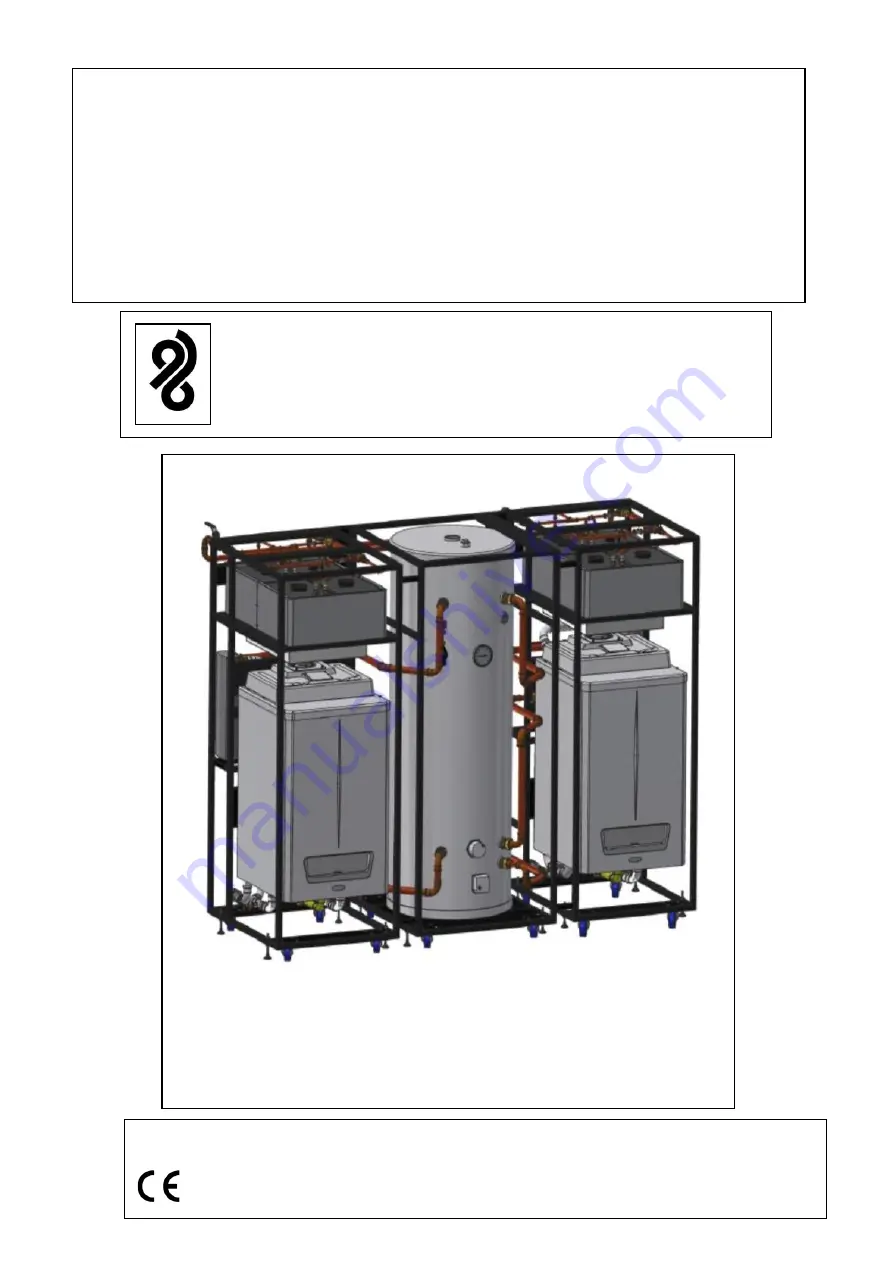
INSTALLATION & SERVICE MANUAL
FOR
BLADE TWIN PLUS WATER HEATER
Models TPWH60 and TPWH80
With 500 litre storage cylinder
INCLUDES ALPHA
E-Tec 20S, 30S and 35S Boiler manual
BLADES LOW CARBON SYSTEMS Ltd
4 Valhalla Industrial Estate, Holsworthy, Devon EX22 6HN
For Technical help or Service call...01566 770799
For use with Natural Gas or Propane Gas (LPG)
Leave these instructions with the User
Содержание BLADE TWIN PLUS TPWH60
Страница 2: ......
Страница 6: ...4 Blade 60 80 Twin Plus Water Heater Manual July 2020 3 0 BLADE WATER HEATER SCHEMATIC LAYOUT ...
Страница 7: ...Blade 60 80 Twin Plus Water Heater Manual July 2020 5 3 1 SCHEMATIC LEGEND ...
Страница 17: ...Blade 60 80 Twin Plus Water Heater Manual July 2020 15 9 0 MAINTENANCE AND SERVICING CLEARANCES ...
Страница 18: ...16 Blade 60 80 Twin Plus Water Heater Manual July 2020 10 0 INSTALLATION SCHEMATIC LAYOUT ...
Страница 21: ...Blade 60 80 Twin Plus Water Heater Manual July 2020 19 13 0 WIRING DIAGRAM ...
Страница 29: ...Blade 60 80 Twin Plus Water Heater Manual July 2020 27 Notes ...
Страница 30: ...APPENDIX A ALPHA BOILER MANUAL ...
Страница 89: ...59 Alpha E Tec S 20 30 and 35 Page intentionally Blank ...
Страница 99: ...Blade 60 80 Twin Plus Water Heater Manual July 2020 29 APPENDIX B DAB PUMP MANUAL ...
Страница 113: ...ENGLISH 41 It is dangerous to touch the circulator DANGER OF SCALDING ...
Страница 123: ...ENGLISH 51 18 PERFORMANCE CURVES EVOSTA2 40 70 XXX ...
Страница 124: ...ENGLISH 52 EVOSTA2 80 XXX ...
Страница 125: ...ENGLISH 53 EVOSTA3 40 XXX ...
Страница 126: ...ENGLISH 54 EVOSTA3 60 XXX ...
Страница 127: ...ENGLISH 55 EVOSTA3 80 XXX ...