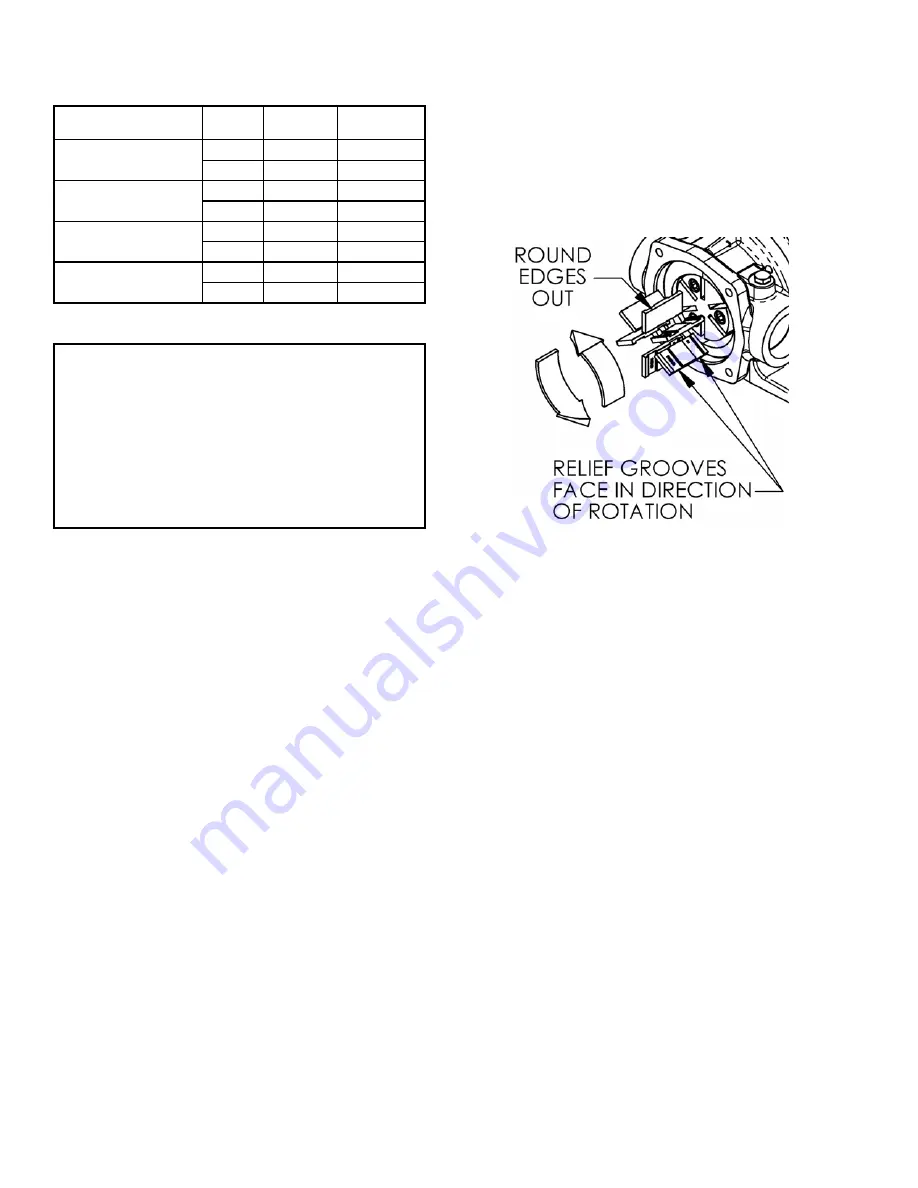
111-G00 Page 8/16
MAINTENANCE:
Torque Table 1
Pump Size
10, 15
20, 30,
40, 50
Ft-Lbs 16.2
30.0
Head / Casing/ Seal
Cover Cap Screws
N-m 22
40.5
Ft/Lbs
4.50
38.00
Rotor Capscrews
N/m
6.10
51.53
Ft-Lbs 3.4
13.1
Bearing Adjuster
Set Screw (189)
N-m 4.7
17.8
Ft-Lbs 3.1
3.1
Ball Bearing Set
Screws (24C)
N-m 4.2
4.2
Suggested Tool List
Allen Wrenches: 5/32”,1/4”, 2mm - 4mm
Combination Wrenches: 10mm - 12mm, 23mm
Pliers: Standard & Long Nose
Spanner Wrench
Strap Wrench
Ball Peen Hammer: 8oz.
Ratchet & Socket Set: 10mm - 12mm, 23mm
Mallet: shot loaded rubber
Self indicating torque tool: PN 165811
SCHEDULED MAINTENANCE
LUBRICATION
The Blackmer ProVane pumps are equipped with ball
bearings that require no additional lubrication.
STRAINERS
Strainers must be cleaned regularly to avoid pump starvation.
Schedule will depend upon the application and conditions.
VANE REPLACEMENT
NOTICE:
Maintenance shall be performed by qualified technicians
following the appropriate procedures and warnings as
presented in this manual.
See the table on page 1 of this manual to determine your
pump model.
Figure 6 – Vane Replacement
1. Flush the pump per instructions in this manual. Drain and
relieve pressure from the pump and system as required.
2. Remove the head cap screws (21). Gently remove the
head from the casing. The head O-ring should come off
with the head assembly.
3. Turn the shaft by hand until a worn vane comes to the top
(12 o'clock) position of the rotor. Remove the vane.
4. Install a new vane, ensuring that the rounded edge is UP,
and the relief grooves are facing towards the direction of
rotation. See Figure 6.
5. Repeat steps 3 and 4 until all vanes have been replaced.
This method of vane installation ensures the push rods do
not fall out of their rotor slots.
6. Carefully install the head (23) into the casing. If equipped
with optional relief valve, to insure proper orientation see
Figures 4 and 5 in "Optional Pump Relief Valve"
section.
Install and tighten four head cap screws (21). Torque per
Table 1 shown at the beginning of the maintenance
section.
Содержание 111-G01
Страница 15: ...111 G00 Page 15 16 NOTES...