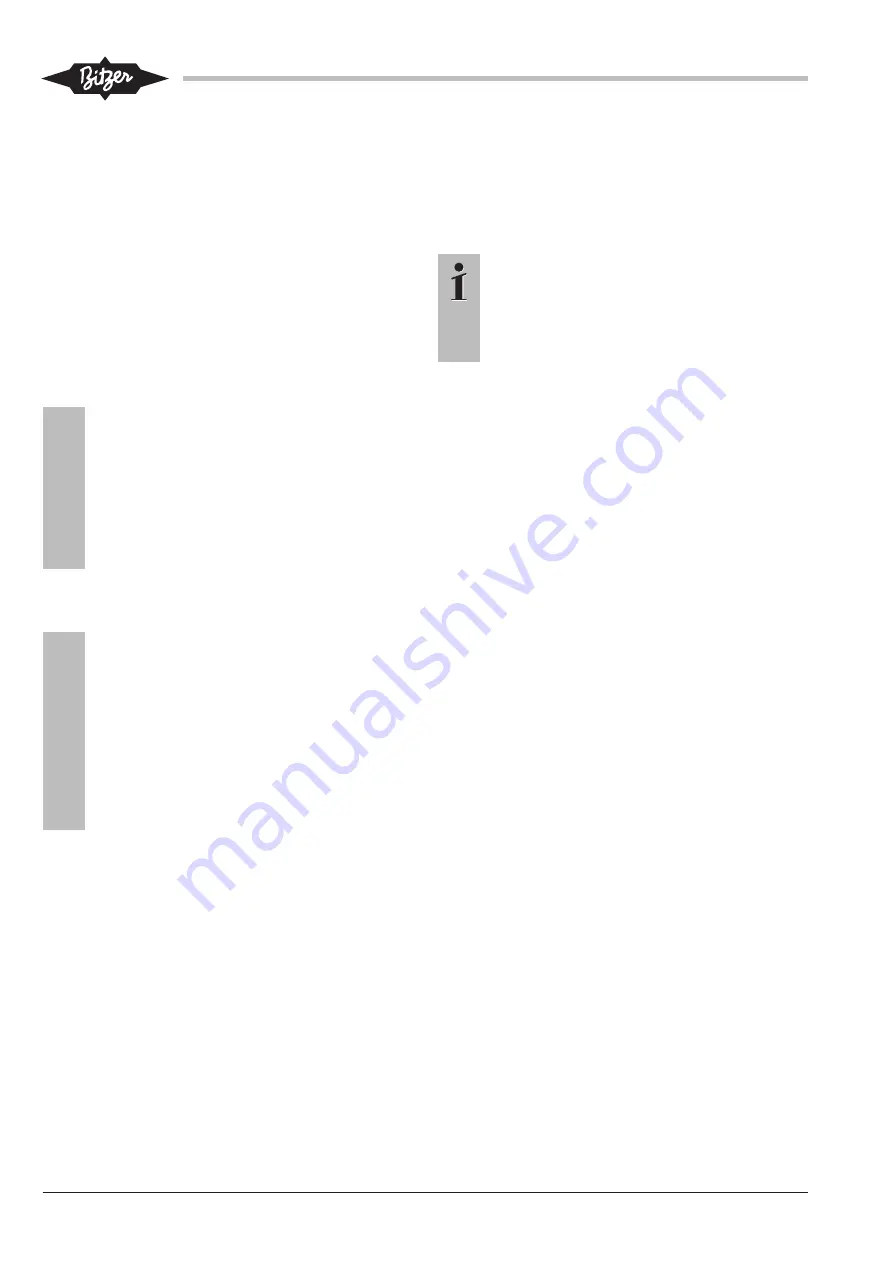
KB-130-7
14
• Cycling rate:
– max. 6 starts per hour
– min. time for a start / stop cycle = 10 min
• Current values of all phases.
• Voltage.
7
Operation
When performing work or measurements on the service
connection (7/16-20 UNF) of the discharge shut-off
valve:
!
!
NOTICE
On the service connection of the discharge
shut-off valve, pressures up to 160 bar may oc-
cur!
Standard components (e.g. pressure gauge
connections, hoses etc.) may be damaged or
destroyed.
Proceed with care and use only appropriate
components for these high pressure levels!
7.1
Operating temperatures and lubrication conditions
!
!
NOTICE
Operation at low pressure ratios and low suction
gas superheat results in low discharge gas and
oil temperature.
Danger of insufficient lubrication due to the high
solubility of CO
2
in oil.
Continuous operation with frequencies > 60 Hz
reinforces this effect and should therefore be
avoided.
If necessary, consultation with BITZERis recom-
mended.
With respect to the lubrication conditions, the following
requirements must be complied with:
• Always use a crankcase heater, particularly during
stop phases.
• Recommended suction gas superheat 20 K – if ne-
cessary, provide for a heat exchanger in order to
minimise the refrigerant concentration in the oil.
A lower suction gas superheat is possible provided
that minimum oil and discharge gas temperatures
are maintained. In direct expansion systems, avoid
values < 10 K!
• Oil temperature 30°C (20°C = absolute minimum
value!).
• Minimum discharge gas temperature = condensing
temperature (t
c
) + 40 K.
For continuous operation, the oil temperature must not
fall below 30°C and pressure gas temperature not
below 50°C!
Information
The discharge gas temperature must be de-
termined with regard to the peak pressures!
Depending on the high and low pressures, very
high discharge gas temperatures may occur
even when operating with saturated suction gas.
• Maximum discharge gas temperature: 140°C, meas-
ured at the discharge gas pipeline (10 cm distance
from the discharge gas connection of the com-
pressor).
• The influence of different load conditions and the ap-
plication of system technologies such as flash gas
bypass on the operation conditions of the com-
pressor must be considered and included in the cal-
culations. If necessary, contact BITZER.
7.2
Regular checks
Check the system at regular intervals according to na-
tional regulations. Check the following points:
• Operating data, see chapter Compressor start, page
• Oil supply, see chapter Compressor start, page 13.
• Safety and protection devices and all components
for compressor monitoring (check valves, discharge
gas temperature sensors, differential oil pressure
limiters, pressure limiters, etc.).
• Tight seat of electrical cable connections and
screwed joints.
• Screw tightening torques.
• Refrigerant charge.
• Tightness.
• Prepare data protocol.
• Replace the pressure relief valves of the com-
pressors after deflating because the opening pres-
sure may be reduced after this procedure.
• Check the sight glass and its joint at regular intervals
and replace them if necessary.
• Check the opto-electronic oil monitoring (OLC-K1) at
regular intervals and replace it, if necessary.