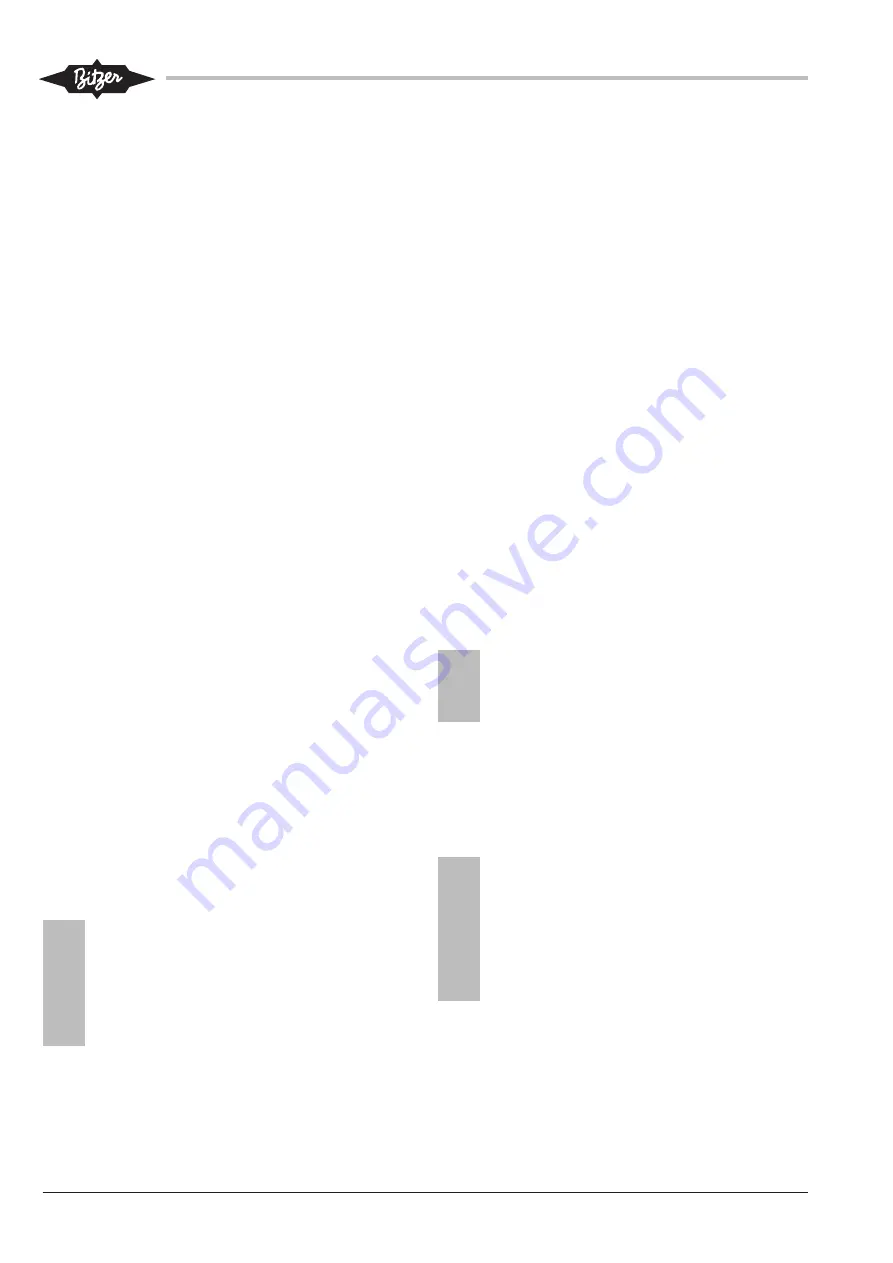
KB-130-6
24
after service work, always break the vacuum with
gaseous CO
2
.
• For CO
2
bottles with ascending pipe, only extract
high-pressure liquid! Do not use a pressure reducer!
The membranes of the pressure reducers are not
completely sealed against liquid penetration.
After filling the system with liquid, remove filling
pipeline or filling hose and make sure that no liquid is
enclosed in it any more!
Permitted refrigerant
CO
2
of purity class N4.5 or comparable, or H
2
O
< 5 ppm.
The CO
2
purity class can have a higher H
2
O level if the
system is filled using a generously dimensioned filter
drier. It is recommended to change the filter drier sev-
eral times after commissioning.
Due to the high requirements regarding residual mois-
ture, a filter drier is required when filling with CO
2
of
quality level N3.0!
Filling process
◦ Do not switch on the compressor.
◦ Switch on the oil heater.
◦ Do not start the charging process until the following
oil temperature has been reached: min. t
oil
= t
amb
+
20 K. Ideally at 35°C .. 40°C.
• Use a pressure reducer and flexible filling pipelines
to connect the CO
2
refrigerant bottle to the service
connections of the system (suction and high pres-
sure side). Before tightening the screwed joints, flush
the pipelines with CO
2
vapour.
• Open the valves of the charging connections and
break the vacuum with CO
2
from the gas phase of
the filling cylinder until an overpressure of approxim-
ately 10 bar is reached. If the temperature of the re-
frigerant bottle is too low, it should be heated in a
water bath (water max. 40°C).
!
!
Notice!
If the system pressure exceeds 10 bar, make
sure that the suction and discharge shut-off
valves of the compressor(s) are closed.
For booster systems: compressors of the me-
dium temperature and low temperature stages
are concerned.
The following work steps until commissioning may differ
depending on the system type.
5.2.1
Single stage systems without intermediate
pressure receiver
• Continue to fill the system with gaseous CO
2
up to a
maximum pressure of 40 bar.
• Make sure that the solenoid valves on the com-
pressor are closed (de-energised).
• Start the manual operation of the ventilators/water
supply for gas cooler.
• Continue to fill the gas cooler with liquid CO
2
.
• Further proceeding, see chapter Compressor start,
5.2.2
Single stage systems with intermediate
pressure receiver
• Continue to charge the system with gaseous CO
2
.
• If the system pressure exceeds 20 bar, make sure
that the solenoid valves on the compressor are
closed (de-energised).
• Start the manual operation of the ventilators/water
supply for gas cooler.
• Continue to charge the intermediate pressure re-
ceiver of the system with liquid CO
2
(the minimum li-
quid level in the container should be reached).
!
!
Notice!
If the pressure in the intermediate pressure re-
ceiver exceeds 30 bar, stop charging refriger-
ant!
• Further proceeding, see chapter Compressor start,
5.2.3
Medium temperature and low temperature
booster systems
!
!
Notice!
Observe the different maximum admissible op-
eration pressures of compressors and compon-
ents used in medium and low temperature
stages.
If system pressure exceeds approx. 10 bar, en-
sure that the suction and discharge valves in
medium and low temperature stages are closed!
• Make sure that the solenoid valves of the evaporator
in the low temperature stage are closed (de-ener-
gised).
• Continue to charge the medium temperature stage
with gaseous CO
2
.
Содержание 2KTE-7K
Страница 43: ...Notes...