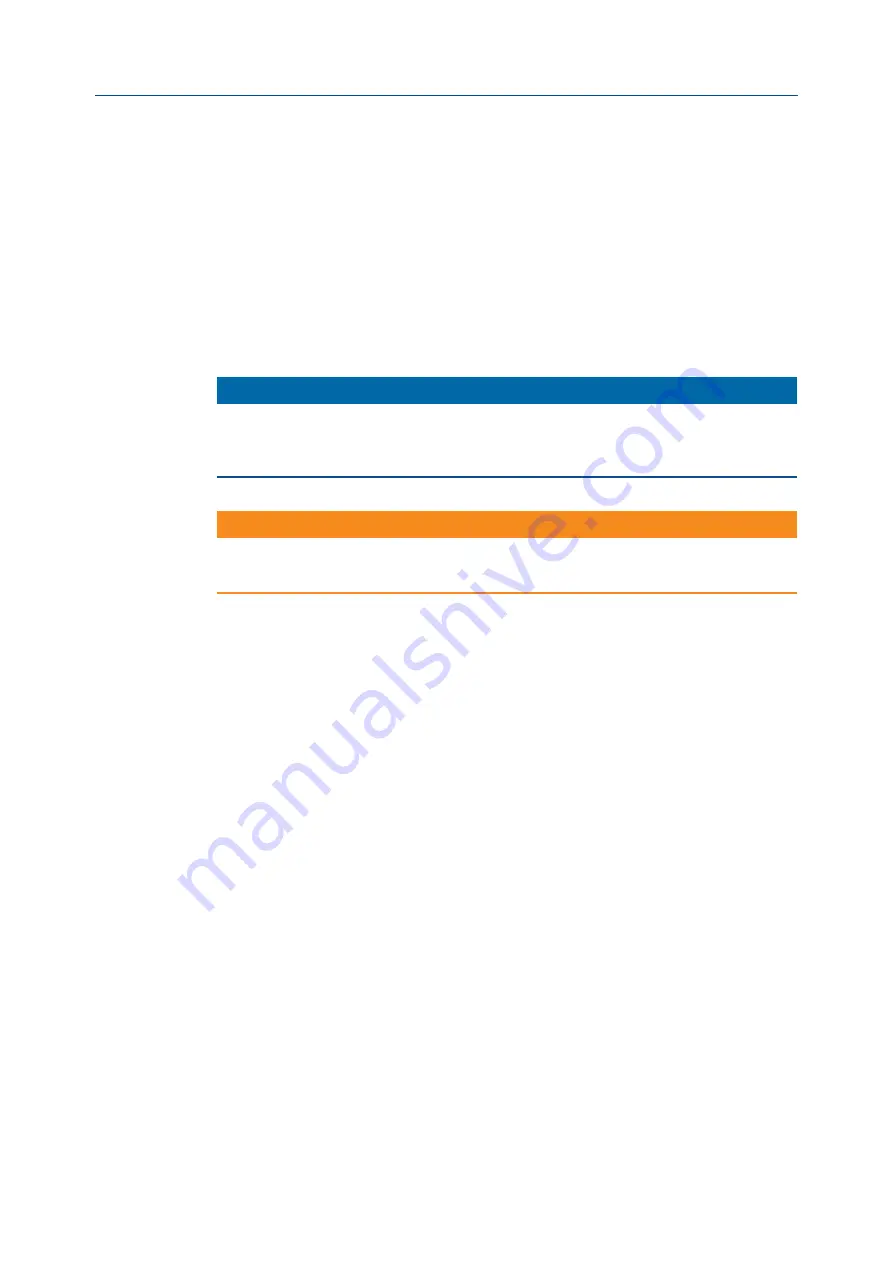
July 2020
Installation, Operation and Maintenance Manual
MAN 575 Rev. 4
22
Maintenance
Section 5: Maintenance
5.2
Extraordinary Maintenance
If there are leaks on RPD actuator or a malfunction in the mechanical components, or in
case of scheduled preventive maintenance, the actuator must be disassembled and seals
must be replaced with reference to the follow general sectional drawing and adopting the
following procedures.
5.2.1
Replacement of Cylinder Seals
(refer to Table 7)
NOTICE
Before carrying out any maintenance operation, it is necessary to close the pneumatic feed
line and exhaust the pressure from the actuator and from the control unit, to ensure safety
of maintenance staff.
!
WARNING
Installation, commissioning and maintenance and repair works should be carried out by
qualified staff. Before carrying out any operation, cut power off from the electrical line.
Replacement of cylinder seals
(see sectional drawing, Figure 15)
1.
Measure the protrusion of the stop screw (30) with reference to the end flange (4)
surface, so as to be able to easily restore the setting of the actuator mechanical
stop, once the maintenance procedures have been completed.
2.
Loosen the lock nut (10) and unscrew the stop screw (30) together with the nut
(10), the washer (28) and the sealing washer (17).
3.
Remove the nuts (25) from the tie rods (14) at the end flange (4) side.
4.
Slide off the end flange (4) and the tube (13). Take care not to damage the plane
surfaces of the tube ends.
Seals replacement
Prior to reassemble check that the actuator components are in good conditions and clean.
Lubricate all the surfaces of the parts, which move in contact with other components, by
recommended grease (AGIP-ENI LCX 2/32 if seals are in NBR/Viton or Neoprene rubber,
or with Aeroshell Grease 7 if the seals are in Fluorosilicon rubber). If the O-ring must be
replaced, remove the existing one from its groove, clean the groove carefully and lubricate
it with protective grease film.
Assemble the new O-ring into its groove and lubricate it with a protective oil film.
1.
Replace the O-ring (24) and the piston guide sliding ring (20).
2.
Remove the existing gaskets (7) from their seats in the housing (1) and in the end
flange (4). Carefully clean the seats and the plane surfaces, at the tube ends, which
are in contact with the gaskets.