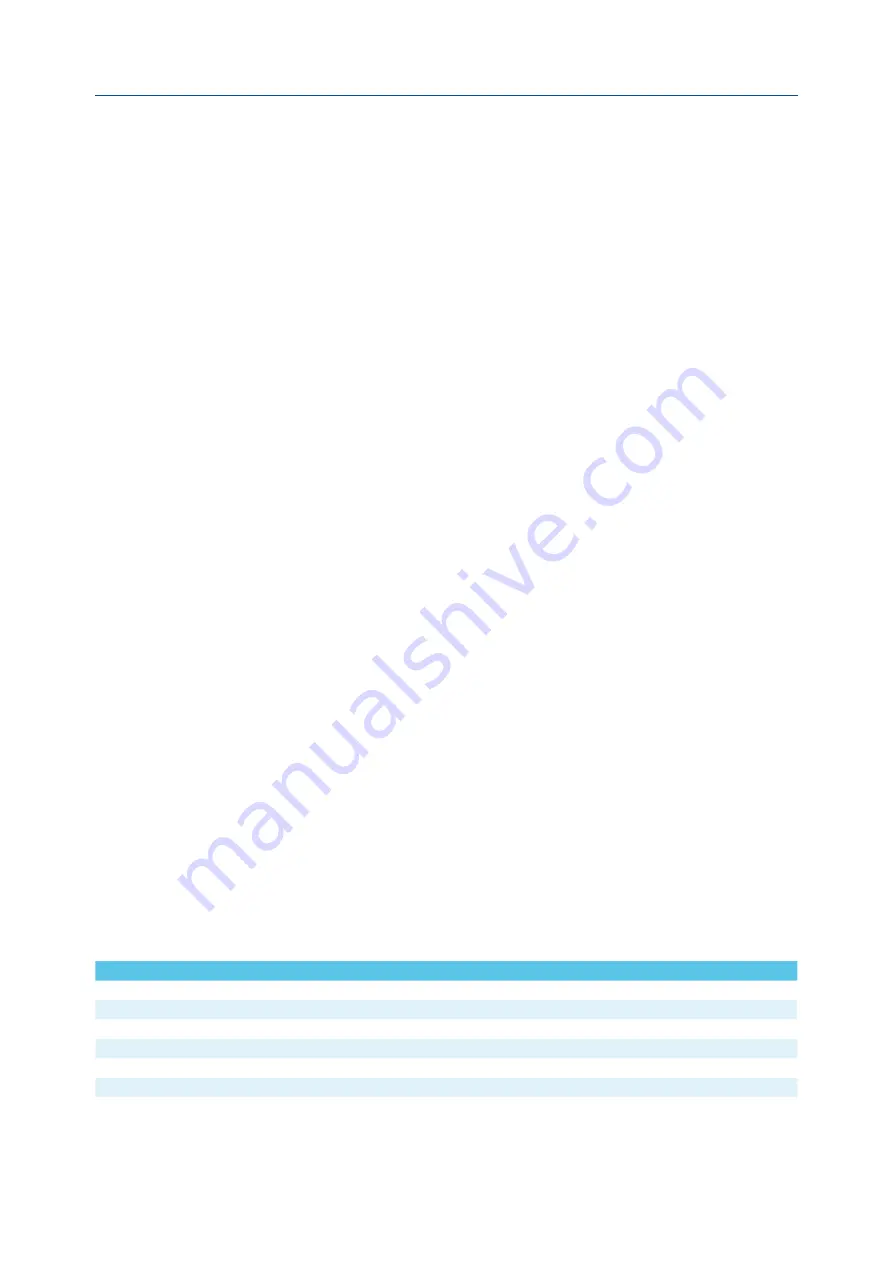
Revision Details
December 2020
Installation, Operation and Maintenance Manual
MAN 608 Rev. 5
Revision Details
Revision Details
Revision
Date
Description
Prepared
Checked
Approved
5
December 2020
Migration to new template
4
April 2020
Updated DATAPLATE
Ermanni
Orefici
Vigliano
3
April 2018
Updated applicable regulation (chapter 1.1.1)
Ermanni
Orefici
Vigliano
2
July 2012
General update
Ermanni
Stoto
Vigliano
1
February 2010
General update
Ermanni
Stoto
Vigliano
0
May 1999
Document release
Lazzarini
Aliani
Ziveri