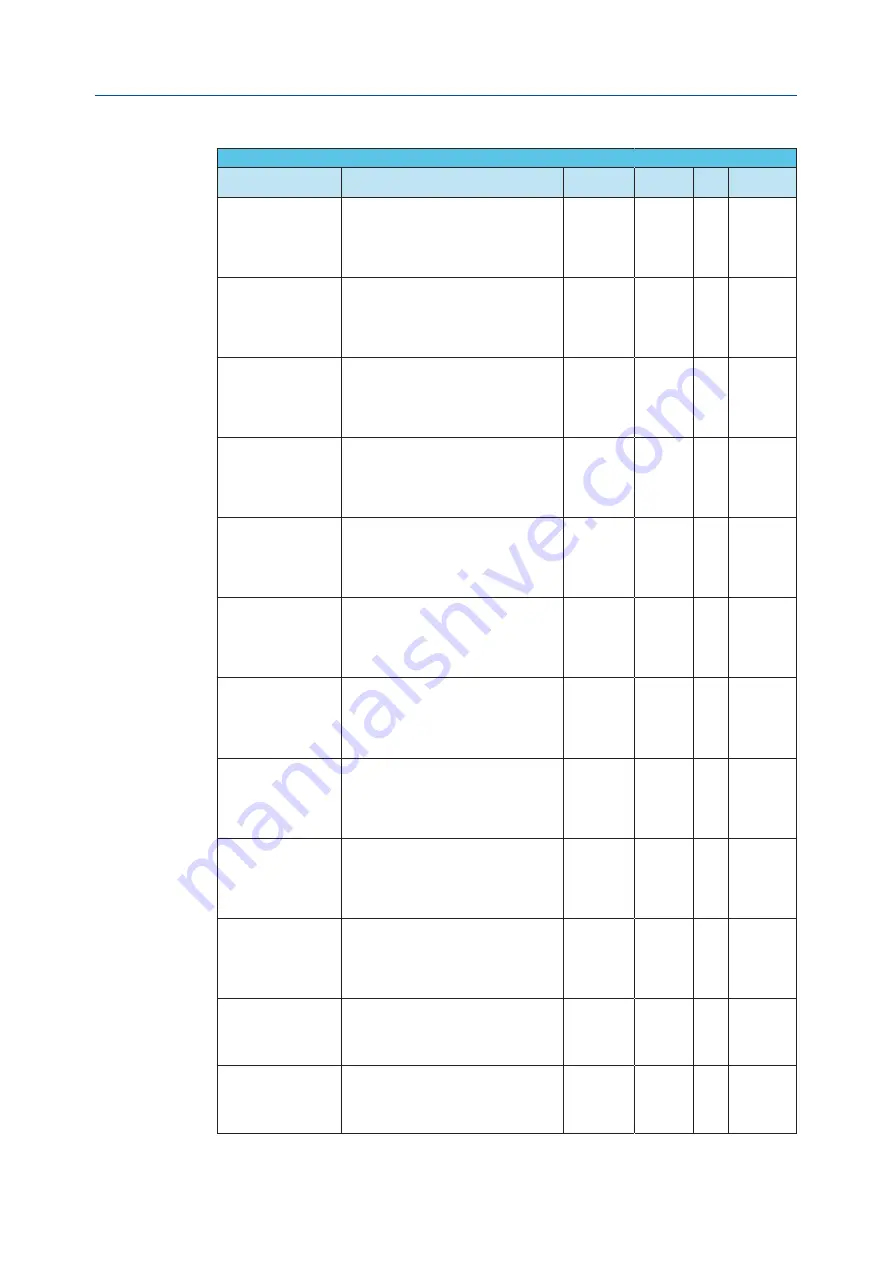
Installation, Operation and Maintenance Manual
September 2019
MAN720_IMVS2000v2_IOM Rev. 6
Section 6: Configuration Parameters
Configuration Parameters
PARAMETERS OF THE “VIEW/SETUP MODE” MENU
PARAMETER NAME
DESCRIPTION
RANGE
DEFAULT
VALUE
R/W
(1)
AVAILABLE
ON (2) (3)
Al. PSA En.
(Alarm PSA Enabled)
Set as “No” it is disabled.
Set as “CFA” it is enabled and associated to the
“PST St.” and to the “CFA St.”
Set as “ALR” it is enabled and it is associated to
the “PST St.” but not to the “CFA St.”
See
Sections
5.2.7, 8 and 5.2.3 for details.
CFA, ALR, No
CFA
R/W
Local, Serial,
Bus
Al. PSB En.
(Alarm PSB Enabled)
Set as “No” it is disabled.
Set as “CFA” it is enabled and associated to the
“PST St.” and to the “CFA St.”
Set as “ALR” it is enabled and it is associated to
the “PST St.” but not to the “CFA St.”
See
Sections
5.2.7, 8 and 5.2.3 for details.
CFA, ALR, No
CFA
R/W
Local, Serial,
Bus
Al. SISA En.
(Alarm SISA Enabled)
Set as “No” it is disabled.
Set as “CFA” it is enabled and associated to the
“CFA St.”
Set as “ALR” it is enabled but not associated to
the “CFA St.”
See
Sections
5.2.7, 8 and 5.2.3 for details.
CFA, ALR, No
ALR
R/W
Local, Serial,
Bus
Al. SISB En.
(Alarm SISB Enabled)
Set as “No” it is disabled.
Set as “CFA” it is enabled and associated to the
“CFA St.”
Set as “ALR” it is enabled but not associated to
the “CFA St.”
See
Sections
5.2.7, 8 and 5.2.3 for details.
CFA, ALR, No
ALR
R/W
Local, Serial,
Bus
OPOS En.
(Alarm OPOS Enabled)
Set as “No” it is disabled.
Set as “CFA” it is enabled and associated to the
“CFA St.”
Set as “ALR” it is enabled but not associated to
the “CFA St.”
See
Sections
5.2.7, 8 and 5.2.3 for details.
CFA, ALR, No
ALR
R/W
Local, Serial,
Bus
Al. CPOS En.
(Alarm CPOS Enabled)
Set as “No” it is disabled.
Set as “CFA” it is enabled and associated to the
“CFA St.”
Set as “ALR” it is enabled but not associated to
the “CFA St.”
See
Sections
5.2.7, 8 and 5.2.3 for details.
CFA, ALR, No
ALR
R/W
Local, Serial,
Bus
Al. LSP En.
(Alarm LSP Enabled)
Set as “No” it is disabled.
Set as “CFA” it is enabled and associated to the
“CFA St.”
Set as “ALR” it is enabled but not associated to
the “CFA St.”
See
Sections
5.2.7, 8 and 5.2.3 for details.
CFA, ALR, No
ALR
R/W
Local, Serial,
Bus
Al. HSP En.
(Alarm HSP Enabled)
Set as “No” it is disabled.
Set as “CFA” it is enabled and associated to the
“CFA St.”
Set as “ALR” it is enabled but not associated to
the “CFA St.”
See
Sections
5.2.7, 8 and 5.2.3 for details.
CFA, ALR, No
ALR
R/W
Local, Serial,
Bus
Al. LPP En.
(Alarm LPP Enabled)
Set as “No” it is disabled.
Set as “CFA” it is enabled and associated to the
“CFA St.”
Set as “ALR” it is enabled but not associated to
the “CFA St.”
See
Sections
5.2.7, 8 and 5.2.3 for details.
CFA, ALR, No
ALR
R/W
Local, Serial,
Bus
Al. HPP En.
(Alarm HPP Enabled)
Set as “No” it is disabled.
Set as “CFA” it is enabled and associated to the
“CFA St.”
Set as “ALR” it is enabled but not associated to
the “CFA St.”
See
Sections
5.2.7, 8 and 5.2.3 for details.
CFA, ALR, No
ALR
R/W
Local, Serial,
Bus
Al. OPNM En.
(Alarm OPNM Enabled)
Set as “CFA” it is enabled and associated to the
“CFA St.”
Set as “ALR” it is enabled but not associated to
the “CFA St.”
See
Sections
5.2.7, 8 and 5.2.3 for details.
CFA, ALR
CFA
R/W
Local, Serial,
Bus
Al. CLNM En.
(Alarm CLNM Enabled)
Set as “CFA” it is enabled and associated to the
“CFA St.”
Set as “ALR” it is enabled but not associated to
the “CFA St.”
See
Sections
5.2.7, 8 and 5.2.3 for details.
CFA, ALR
CFA
R/W
Local, Serial,
Bus
53
Содержание IMVS2000v2
Страница 2: ......