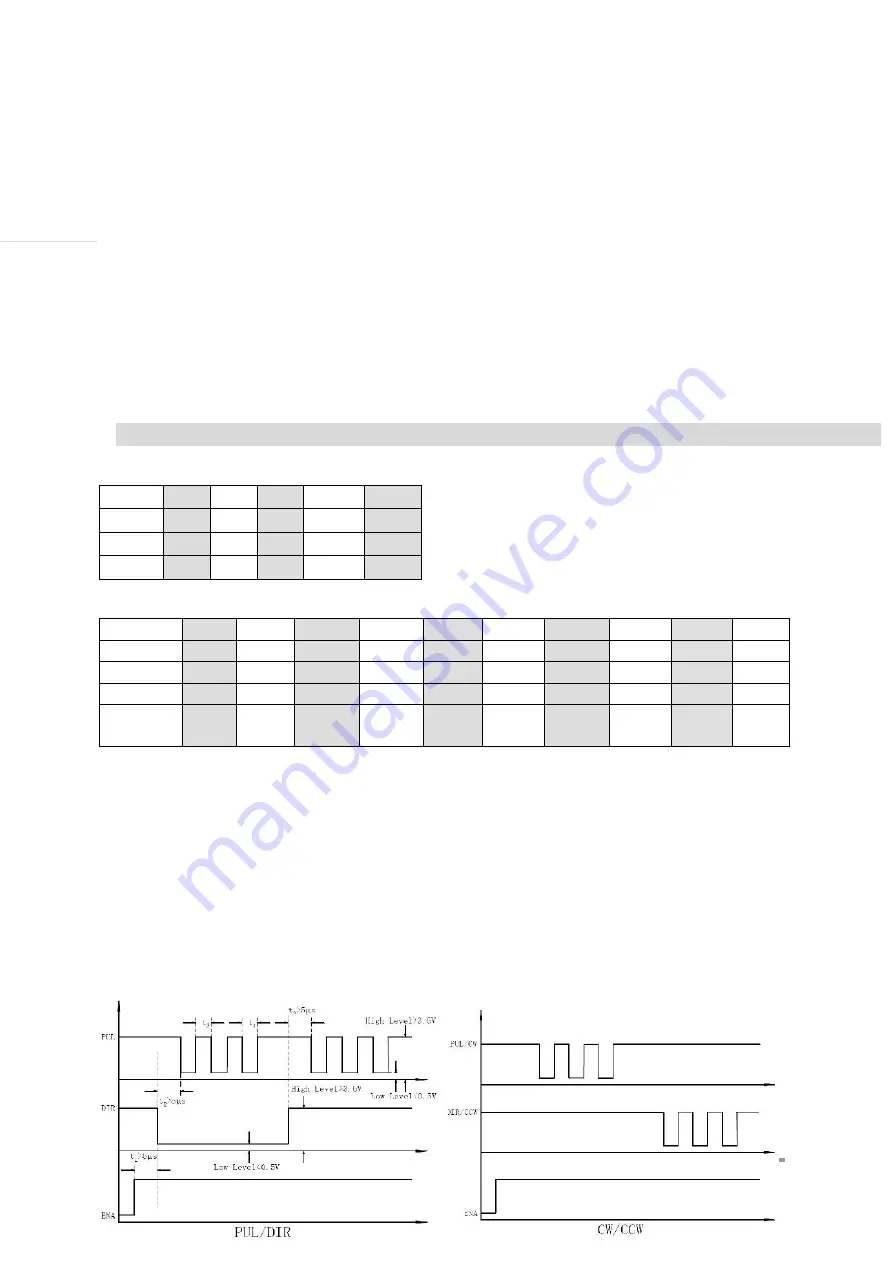
Website:-www.bholanath.in
E-mail id:[email protected]
BHOLANATH PRECISION ENGINEERING PVT. LTD.
Page | 6
Wiring Notes
To prevent noise incurred in PUL/DIR signal, pulse/direction signal wires and motor wires
should not be tied up together. It is better to separate them by at least 10 cm, otherwise the
disturbing signals generated by motor will easily disturb pulse direction signals, causing
motor position error, system instability and other failures.
If a power supply serves several drivers, separately connecting the drivers is recommended
instead of daisy-chaining.
It is prohibited to pull and plug connector P2 while the driver is powered ON, because there is
high current flowing through motor coils (even when motor is at standstill). Pulling or
plugging connector P2 with power on will cause extremely high back-EMF voltage surge,
which may damage the driver.
Switch Choice:
1.Microstepping choice:
SW 6
off
on
off
on
off
SW 7
off
off
on
on
off
SW 8
off
off
off
off
on
Micro
200
400
800
1600
3200
2.Current choice
::::
SW 1
off
on
off
on
off
on
off
on
off
on
SW 2
off
off
on
on
off
off
on
on
off
off
SW 3
off
off
off
off
on
on
on
on
off
off
SW 4
off
off
off
off
off
off
off
off
on
on
Current
(A)
2
2.5
3
3.5
4
4.5
5
5.5
6
6.5
SW5:-OFF- Half Current, ON- Full Current.
Default setting is OFF i.e. Half Current. Full current to be used for increasing torque if required and for
holding torque operations. At full current motor and driver temperature will rise, kindly arrange external
cooling.
Note:-Any DIP Switch Setting other than above
Current:-The 0.5 A current will be set.
Microstep:-3200 microstep will be set.
4.Sequence Chart of Control Signals
In order to avoid some fault operations and deviations, PUL, DIR and ENA should abide by
some rules, shown as following diagram
: