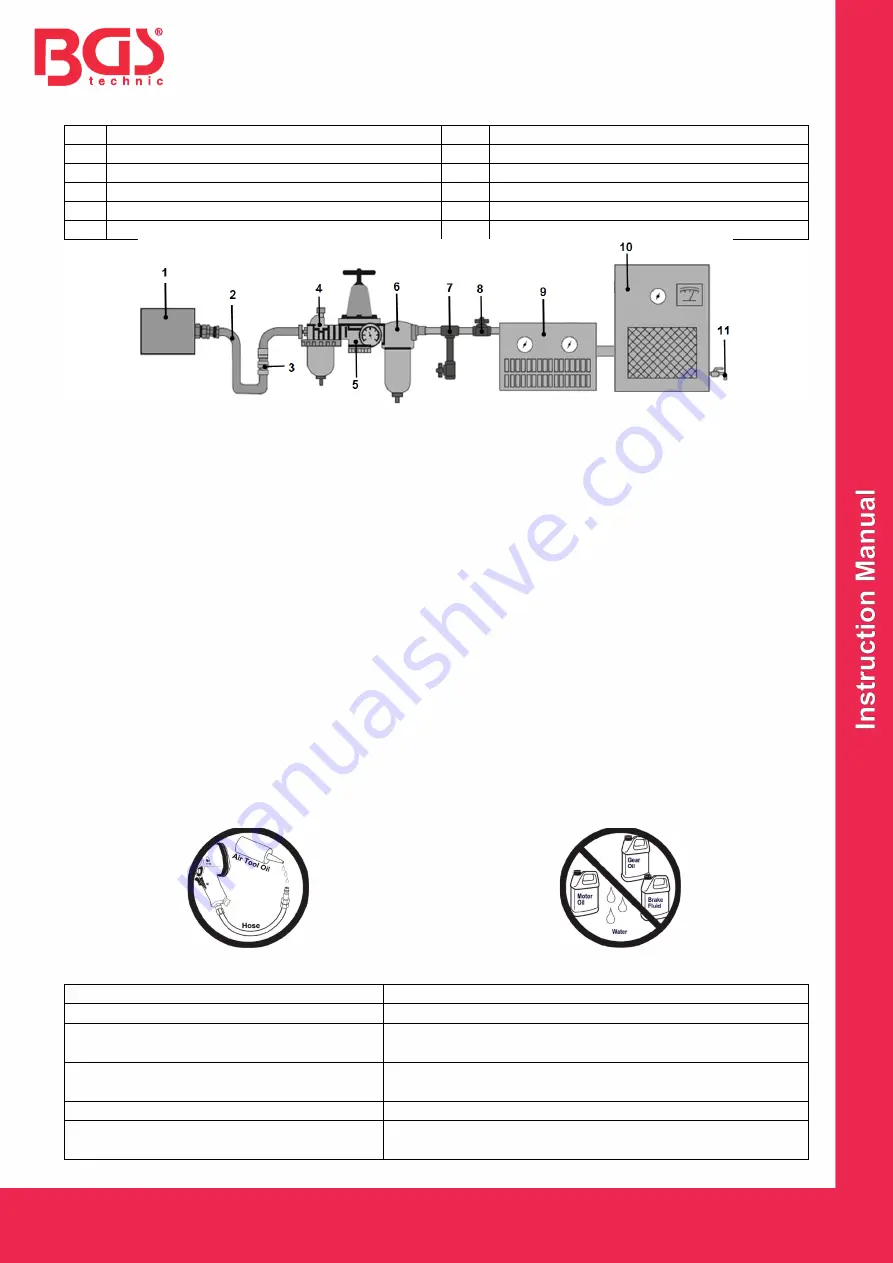
BGS technic KG
Bandwirkerstr. 3
D-42929 Wermelskirchen
Tel.: 02196 720480
Fax.: 02196 7204820
www.bgstechnic.com
© BGS technic KG, Copying and further use not allowed
RECOMMENDED AIR SYSTEM
No.
Description
No.
Description
1
Air Tool
6
De-Watering / Filter Unit
2
Air Hose
7
De-Watering Valve
3
Quick coupler
8
Shut-Off Valve
4
Oiler
9
Dryer / Filter Unit
5
Pressure Regulator
10
Compressor / 11 De-Watering Valve
LUBRICATION & MAINTENACE
•
Use proper air pressure and CFM rating listed for this tool
.
•
Drain water from hoses and compressor tank
.
Water in the air supply line damage the tool and
loss of power
.
•
Clean or replace air filters at prescribed intervals
.
•
The tool should be lubricated daily (or before each use) with air tool oil (not included).
Note
:
SAE #10 weight oil or sewing machine lubricant or any other high grade turbine oil
containing moisture absorbent, rust inhibitors, metal wetting agents and an EP (extreme
pressure) additive may be used as a substitute. Do not use detergent oil. During continuous
operation, the tool should be oiled every 1 to 2 hours. This may be done using an in-line oiler, or
manually. If done manually, proceed as follows
:
•
Disconnect the air tool from air supply. (Fig.7)
•
Place a few drops of air tool oil into the air inlet. (Fig.8)
.
Note
:
Avoid the misuse of thicker oil
which may lead to the reduced performance or malfunction
.
•
Connect the tool to the air supply. Run the tool without load for a few seconds to distribute the oil
through the tool. Any excess oil may be propelled from the air exhaust area. Direct the air tool in
a safe direction.
•
After operating the air tool and before storing, disconnect the air hose and place 4 or 5 drops of
air tool oil into the air inlet, then re-connect the air hose and run the tool to evenly distribute the oil
throughout the tool for 30 seconds approximately. This will increase the life of the tool.
•
Avoid storing the tool in a humid environment which promotes rusting of internal mechanisms.
Always oil the air tool before storage.
•
Do not use a damaged air tool, only use the air tool again after it has been repaired.
TROUBLESHOOTING
I
nsufficient power:
Probable Cause
Solution
Dirty or clogged air passages
Flush and lubricate tool, drain air tank and supply line
Insufficient air supply
Increase line pressure, make sure compressor matches
tool's air pressure and consumption needs
Air leakage
Use teflon tape at all fittings and joints.
Check tool for worn or damaged o-rings & seals.
Worn/damaged wear & tear parts
Replace as necessary
Tool matching
Be sure you are using a tool suited for the sanding
requirements of the job at hand.