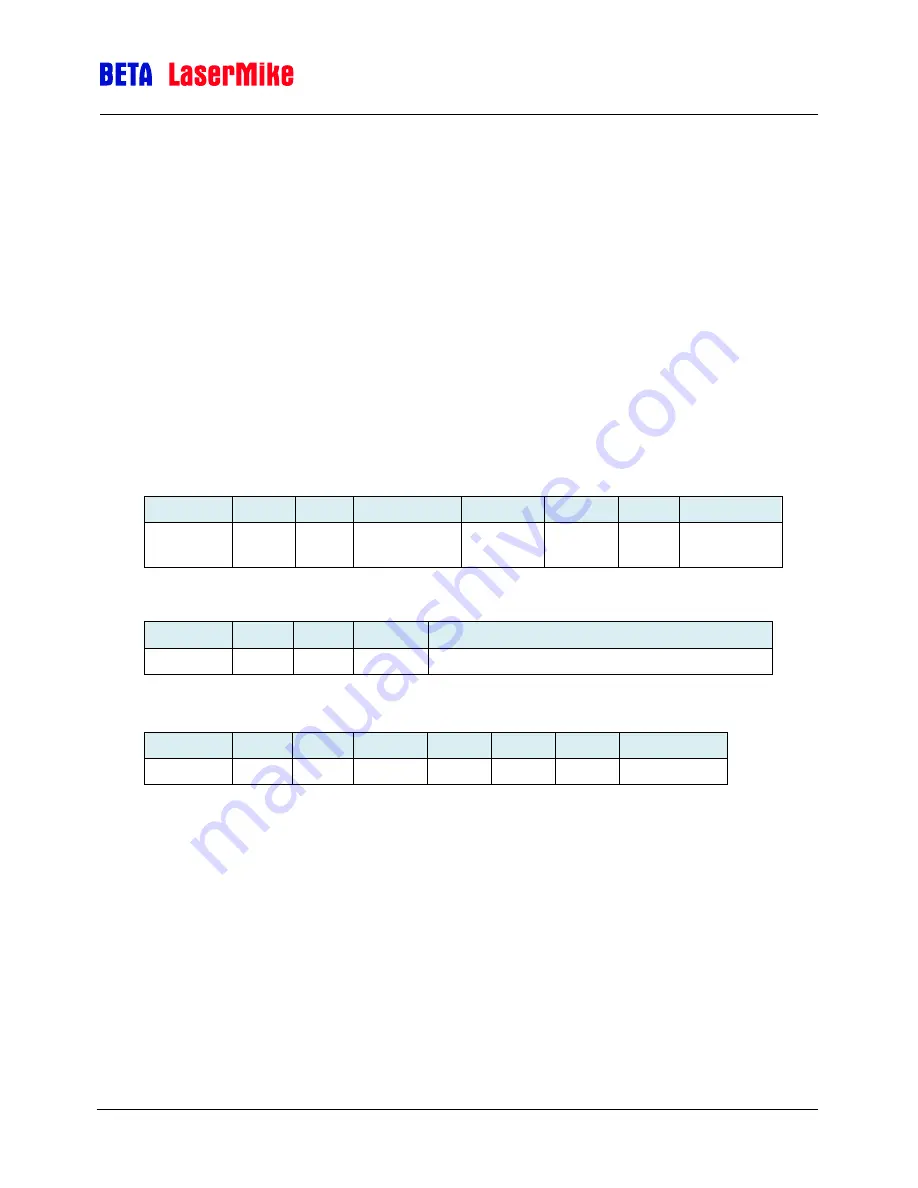
LaserSpeed 8000/9000 I/O Module Instruction Handbook
Operation
Part No. 93342 / Drawing No. 0921-01516
Page 64 of 84
Revision E (Dec 2013)
To retrieve data, the least significant 2 bits (LS-nibble) of the PUV Command
Status Byte determine the mode of operation of the I/O Module. The data
corresponds to Output Data block. A simple handshake scheme between the
Fieldbus Master and the I/O Module accomplish configuration. The Master sets
the LS-nibble of its PUV Command Status to 0x02 (hexadecimal value) to begin
the initialization process. The I/O Module reads the PUV value at every 100
milliseconds and begins a configuration sequence when the PUV = 0x02. The
I/O Module gets the configuration parameters from the gauge and updates
Master’s Output Data block, then writes 0x02 back to the Master’s PUV to signal
start of transfer. The Master sets the PUV to 0x00. The configuration sequence
ends with the LaserSpeed setting its corresponding PUV byte to 0x00. The
Master then reads data.
PUV, Velocity, Length, Status, Quality Factor
These locations are updated on each user update period.
Status Bits
Bit 7
Bit 6
Bit 5
Bit 4
Bit 3
Bit2
Bit 1
Bit 0
Toggle
0
0
Valid
measurement
Material
present
Shutter
Open
Laser
On
At
Temperature
Quality Factor Bits
Bit 7
Bit 6
Bit 5
Bit 4
Bit 3
– Bit 0
0
0
0
0
0- 15
Velocity Sign Bits
Bit 7
Bit 6
Bit 5
Bit 4
Bit 3
Bit 2
Bit 1
Bit 0
0
0
0
0
Sign
Sign 1 = minus, 0 = +.