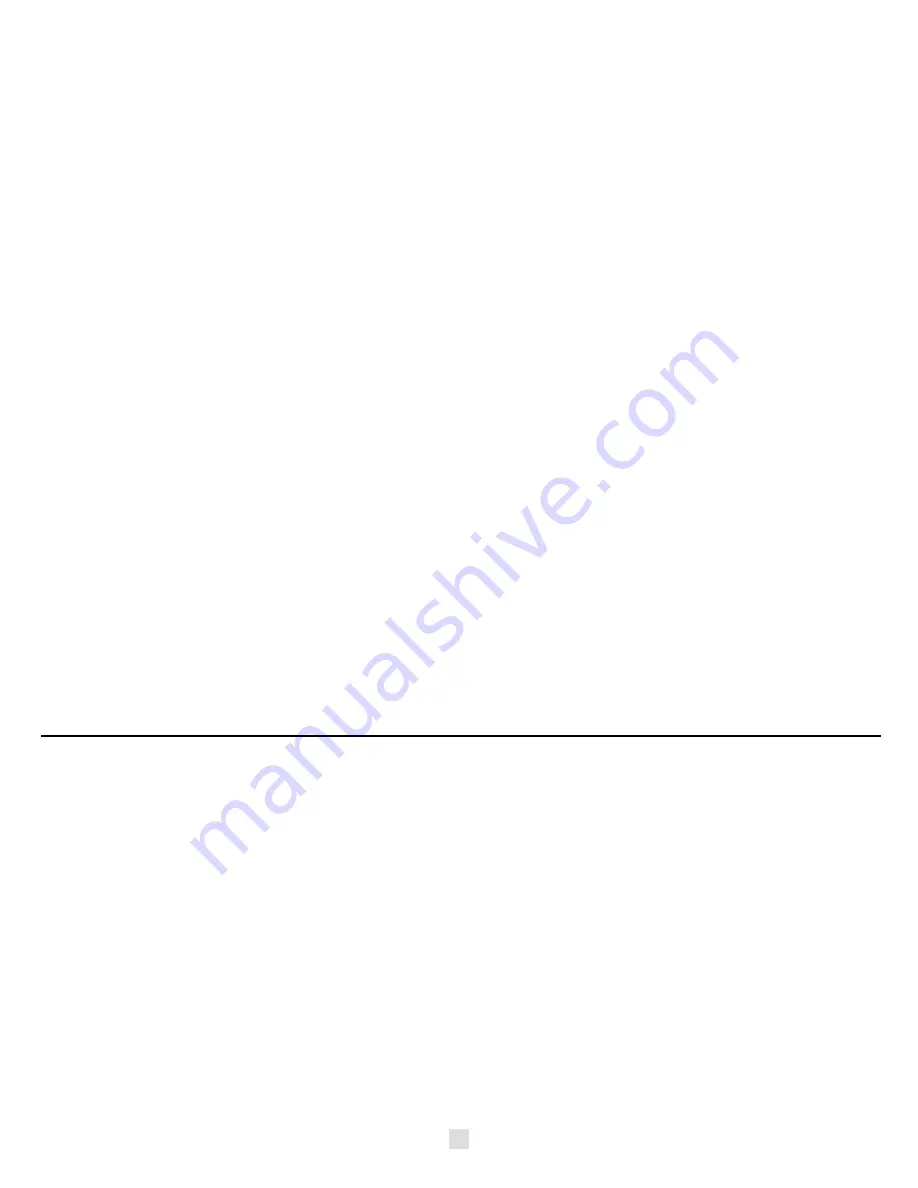
6
besseytools.com
To understand the process in greater detail: Induction heating works when an alternating
electrical current is applied to the primary of a transformer creating an alternating magnetic
field. According to Faraday’s Law, if the secondary of the transformer is located within the
magnetic field, an electric current will be induced. For example: an AC current is sent through
an inductor (like a copper coil in an induction bearing heater), and the part to be heated (the
workpiece) is placed within or around the inductor (crossbar/yoke). The inductor serves as
the transformer primary and the part to be heated becomes a short circuit secondary. When
a metal part is placed within the inductor and enters the magnetic field, circulating eddy
currents are induced within the part. An eddy current is a localized electric current induced
in a conductor by a varying magnetic field and when these electrical currents flow against
the electrical resistance of metal they generate precise and localized heat without any direct
contact between the part being heated and the bearing heater.
The efficiency of a bearing heater depends on several factors: size and weight of the material
being heated, the design of the inductor, the capacity of the power supply, and the amount of
temperature change required for the application. It is important to note that induction heating
works directly only with conductive materials, normally metals. With conductive materials,
about 85% of the heating effect occurs on the surface or “skin” of the part; the heating
intensity diminishes as the distance from the surface increases. Small or thin parts generally
heat more quickly than large thick parts, especially if the larger parts need to be heated all
the way through. Also, the type of material can affect the speed of induction heating. Some
materials like steel – along with carbon, tin and tungsten – have high electrical resistivity.
Because these metals strongly resist the current flow, heat builds up quickly. Low resistivity
metals such as copper, brass and aluminum take longer to heat. Temperature can also
affect the speed of induction heating. Resistivity increases with temperature, so a very hot
piece of steel will be more receptive to induction heating than a cold piece.
3. Installation
■
Remove packing material and place the induction heater on a non-ferrous, stable, flat surface.
The box will normally contain the heater and a crossbar/yoke, or set of crossbars/yokes.
■
Check that supply voltage and current meet the specifications on the type plate, found on
the back of the machine.
■
When the heater is not provided with a plug, a suitable one must be affixed by a qualified
electrician.
■
Make sure the supply cable cannot come into contact with the bearing that is to be
heated. Insert the plug into a shockproof wall socket.
■
Use the main switch to switch on the current. The machine will emit a short beep and the
display will show a “pre-set goal temperature” set by the manufacturer.
■
The induction heater is now ready to be used.
Isolate larger workpieces from the environment by packing them in isolation material like
welding cloth. This keeps the heat in the workpiece and avoids heat transmitting to the air.