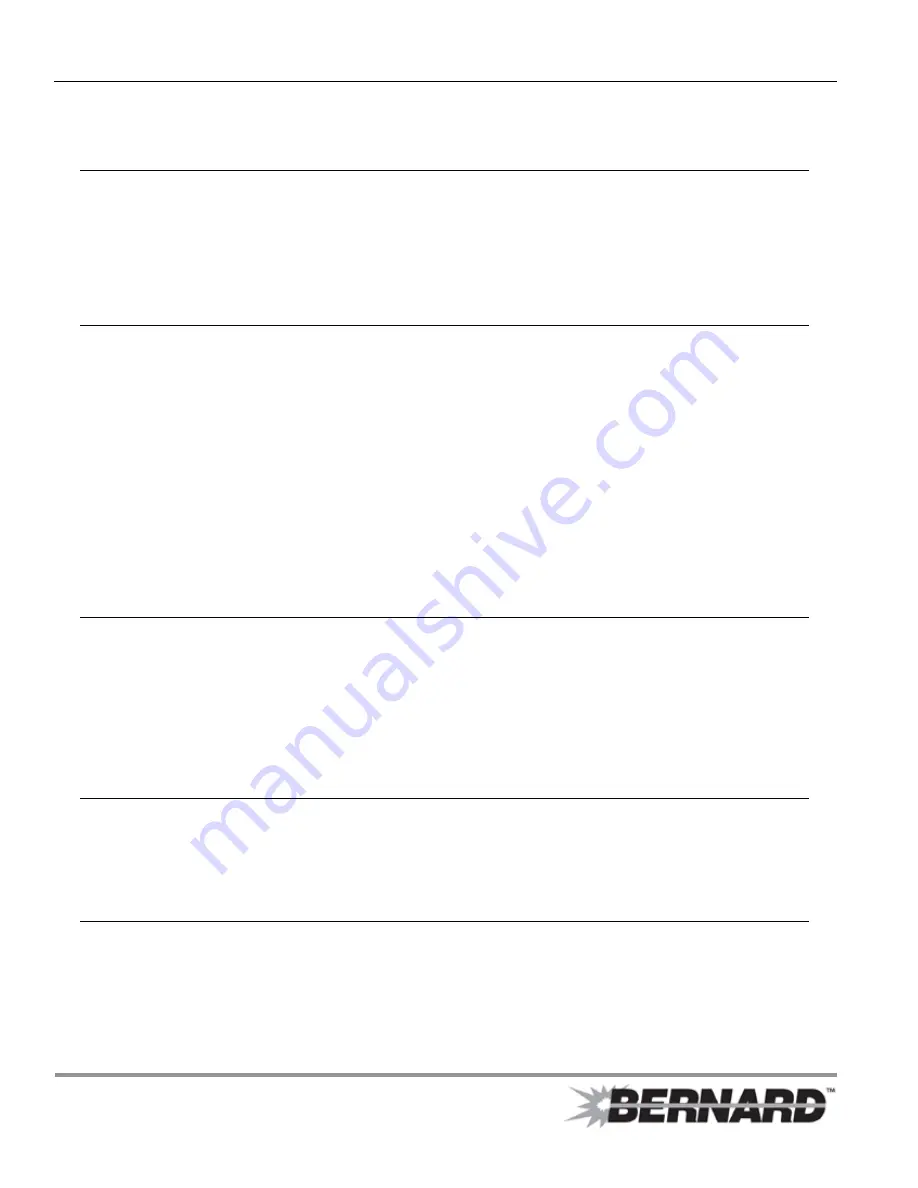
page 9
Part V Troubleshooting Guide (cont.)
*In some cases with aluminum and mild steels, it may be necessary to use a contact tip with either a larger or smaller bore size.
7. Extreme spatter
1. Improper machine parameters.
2. Improper tip installation.
3. Improper shielding.
4. Contaminated wire or work piece.
1. Adjust parameters.
2. Adjust nozzle/tip relationship.
3 a. Verify shielding gas coverage.
b. Verify gas mixture.
4. Clean wire and work piece.
8. Porosity in weld
1. Insulator worn.
2. Gas diffuser damaged.
3. Extreme heat or duty cycle.
4. Solenoid faulty.
5. No gas.
6. Flow improperly set.
7. Gas ports plugged.
8. Ruptured gas hose.
9. Control circuit loss.
10. Worn, cut or missing O-rings.
11. Loose fittings.
1. Replace nozzle/insulator.
2. Replace gas diffuser.
3. Replace with heavy duty consumables.
4. Replace solenoid.
5 a. Install full tanks.
b. Check supply.
c. Hose leaks.
6. Adjust.
7 a. Clean or replace gas diffuser.
b. Clean nozzle.
8. Repair or replace cable or line.
9. See ‘Electrode Does Not Feed’.
10. Replace O-rings
11. Tighten gun & cable connections to speci-
fied torque. See ‘Maintenance & Repair’
(Section 8).
9. Gun running hot
1. Exceeding duty cycle.
2. Loose or poor power connection.
3. Improper water flow
4. Exceeds water cooler capacity
1. a. Replace with properly rated Bernard gun.
b. Decrease parameters to within gun rating.
2. a. Clean, tighten or replace cable grounding
connection.
b. Tighten gun & cable connections to
specified torque. See ‘Maintenance & Repair’
(Section 8).
3. Verify proper water flow
4. Replace with properly rated water cooler
10. Liner is discolored full length
1. Short circuit to electrode.
2. Broken copper stranding in power cable.
1. Isolate electrode reel from feeder and drive
block. Consult feeder manufacturers manual.
2. Replace power cable assembly as per
‘Maintenance & Repair’ (Section 8).
11. Sporadic feeding of aluminum electrode
1. Tip galling.
2. Synthetic liner melting.
3. Wire deformed by feed rolls.
1. *Inspect & replace.
2. a. Replace liner.
b. Replace with composite liner.
3. Adjust drive rolls as per feeder manufacturer’s
manual.
PROBLEM
POSSIBLE CAUSE
CORRECTIVE ACTION
©2014 Bernard