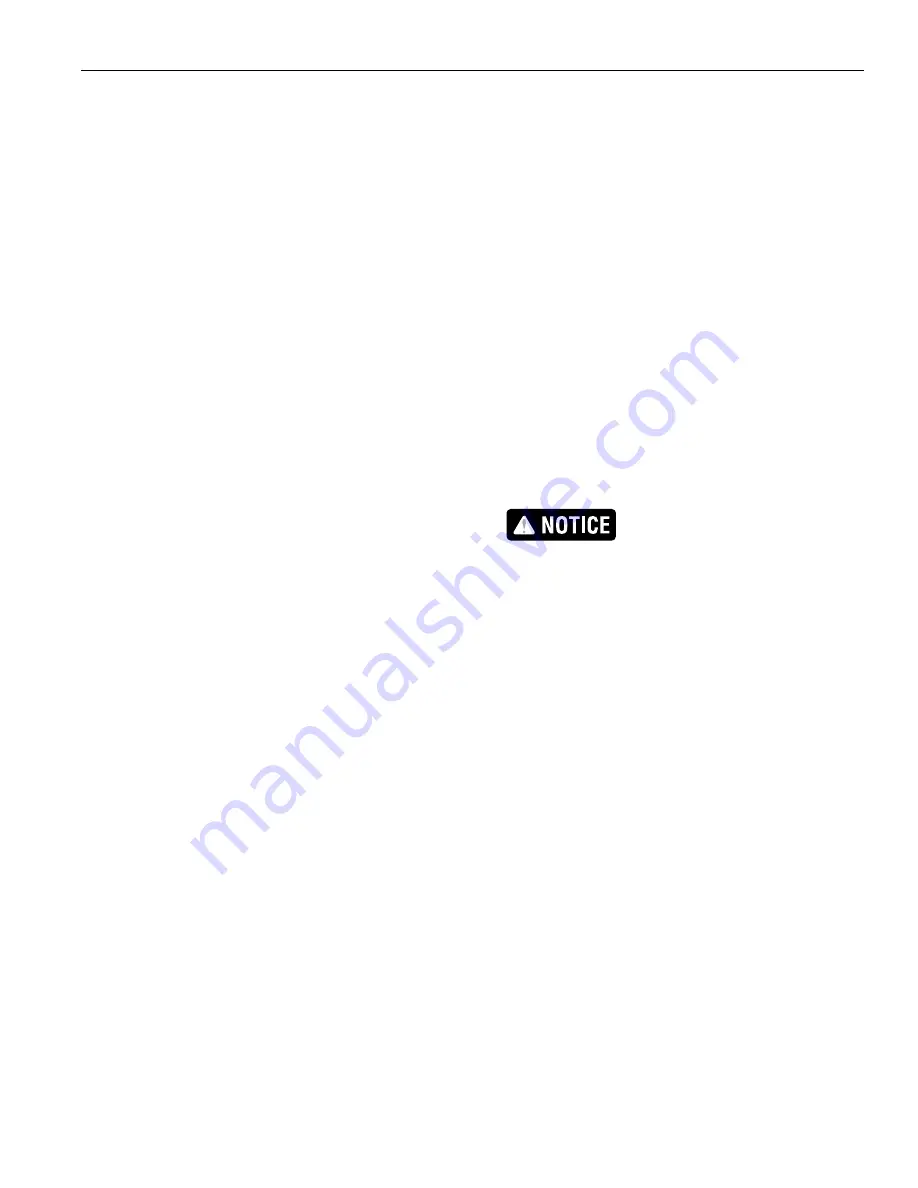
Part I General Description
The Bernard W-Gun is a water-cooled gun that is designed for
processing mild steel electrode under GMAW (Gas Metal Arc Welding),
MIG (Metal Inert Gas), MAG (Metal Active Gas), FCAW (Flux Cored Arc
Welding), and MOG (Metal without Gas).
The Bernard W-Gun provides longer consumable life while reducing
operator fatigue, which can increase overall welding effectiveness.
Bernard W-Guns can reduce the downtime and expenses associated
with changing consumables during the welding process. Lightweight
and flexible design allows for easier movement during welding between
standard horizontal welding, overhead, and hard-to-reach side angles.
Bernard W-Guns can effectively reduce your operating cost and improve
the productivity of your welding operation.
The Bernard W-Gun meets or exceeds NEMA (National Electrical
Manufacturer’s Association) EW3 and CE EN50078 requirements for
guns used in a wide variety of applications including aluminum, silicone
bronze, and hard facing alloys to name a few. With Bernard’s flexibility,
many applications can be accommodated with field installed options,
increasing performance and maneuverability.
Part II Installation
1. Your gun has been shipped with a specific feeder connector and
sized for electrode as per the part number indicated on its package.
Please inspect the received gun against this part number for
accuracy.
2. Turn off power prior to any installation.
3. Fully extend gun and cable. Press liner fully into power pin.
4. Safely expose approximately 2” (51 mm) of electrode beyond
feeder or adaptor block.
5a.
Bernard Quick Disconnect
If you have purchased a Bernard Quick Disconnect gun, it is
necessary to connect this unit to an adaptor kit providing the
shielding gas, control circuit, and arc power. If this is a new
installation, install the adaptor kit as per the kit instructions. With
the Bernard adaptor installed, perform the following:
Orient power pin and gas pin with the adaptor receptacle. Slide
the electrode into the liner and push the power pin into the socket.
Rotate the locking sleeve until the locking pins of adaptor drop into
the receiver of locking sleeve. Continue to engage power pin while
twisting locking sleeve to make connection. Shielding gas, control
circuit, and power are now engaged.
5b.
Direct Plug
Connect the power pin of the direct plug gun by sliding the
electrode into the liner and the power fitting into the drive housing
of the feeder. Fully seat the unit in position and tighten into
place as designated in the manufacturer’s instructions. On initial
installations, a thin film of silicone lubricant will aid installation and
prevent O-ring damage.
Attach control lead wires to the appropriate plug, terminals, or lead
kit. Plug or wire into the control circuit of the feeder as designated
in manufacturer’s instructions.
If a gas hose is provided, connect to the feeder’s solenoid circuit
to deliver shielding gas to the arc. If no gas hose is provided, gas
is delivered through the power pin. Refer to the manufacturer’s
instructions for proper gas connection at the feeder block or
solenoid.
6. Connect water lines to a water coolant source. Each hose is
identified for proper connection by a tethered drip cap (blue: water
inlet, red: water outlet) and label. If a water hose hook-up kit is
used, make all runs as short as possible. Always use hoses with
at least a 3/16” inside diameter for extended runs. Reinforced
hoses of high quality are recommended to prevent damage due to
operating pressures, heat, and hose contamination. The coolant
system must produce a minimum of 0.5 gpm at 60 psi. Run
coolant through gun for approximately 2 minutes to purge system
of entrapped air before applying power. Water must flow through
the gun at all times while the power supply is on.
7. Remove nozzle from gas diffuser.
8a. Centerfire Tip – Remove tip holder by turning counterclockwise
and then pull tip from gas diffuser. An unobstructed electrode path
has now been established.
8b. Elliptical Tip – Remove tip with a 1/8-1/4 turn counterclockwise
while pulling. An unobstructed electrode path has now been
established.
8c. Quik Tip – Remove tip with a 1/4 turn counterclockwise. An
unobstructed electrode path has now been established.
9. Safely feed electrode through the gun and approximately 1” (25
mm) beyond gas diffuser.
10a. Centerfire Tip – Reinstall the tip over the electrode and lock into
position by reinstalling the tip holder. Reinstall nozzle.
10b. Elliptical and Quik Tip – Reinstall the tip over the electrode locking
into position with a clockwise motion. Reinstall nozzle.
Coolant must flow through the gun prior to and
during welding. Welding current and duty cycle
should not exceed published specification of
this product. If such conditions exist, product
life and performance will be reduced.
Part III Helpful Operating Tips
Nozzles:
1. If anti-spatter is used, do not coat nozzle insulator as this may
degrade insulating material.
2. Nozzle should be cleaned as often as possible. Spatter buildup can
often lead to poor gas shielding or short circuiting between the
contact tip and the nozzle.
3. Spatter should be removed with the proper tools designed for
spatter removal.
4. In high temperature welding applications, heavy duty consumables
are recommended.
Contact Tips, Gas Diffusers:
1. Centerfire and Elliptical contact tips may be removed and rotated in
gas diffuser, providing additional wear surfaces and extending the
service life of the product.
2. Electrical stickout of the elliptical contact tip can be altered by
positioning the contact tip in the desired location of the gas
diffuser and rotating clockwise locking in place.
3. Inspect nozzle for spatter adhesion, blocked gas ports, and carbon-
ized contact surfaces. Clean as often as possible.
4. If anti-spatter is used, periodically check gas ports for blockage.
5. When using dual shield electrode, periodically check gas ports for
clogging caused by flux from within the electrode.
page 2