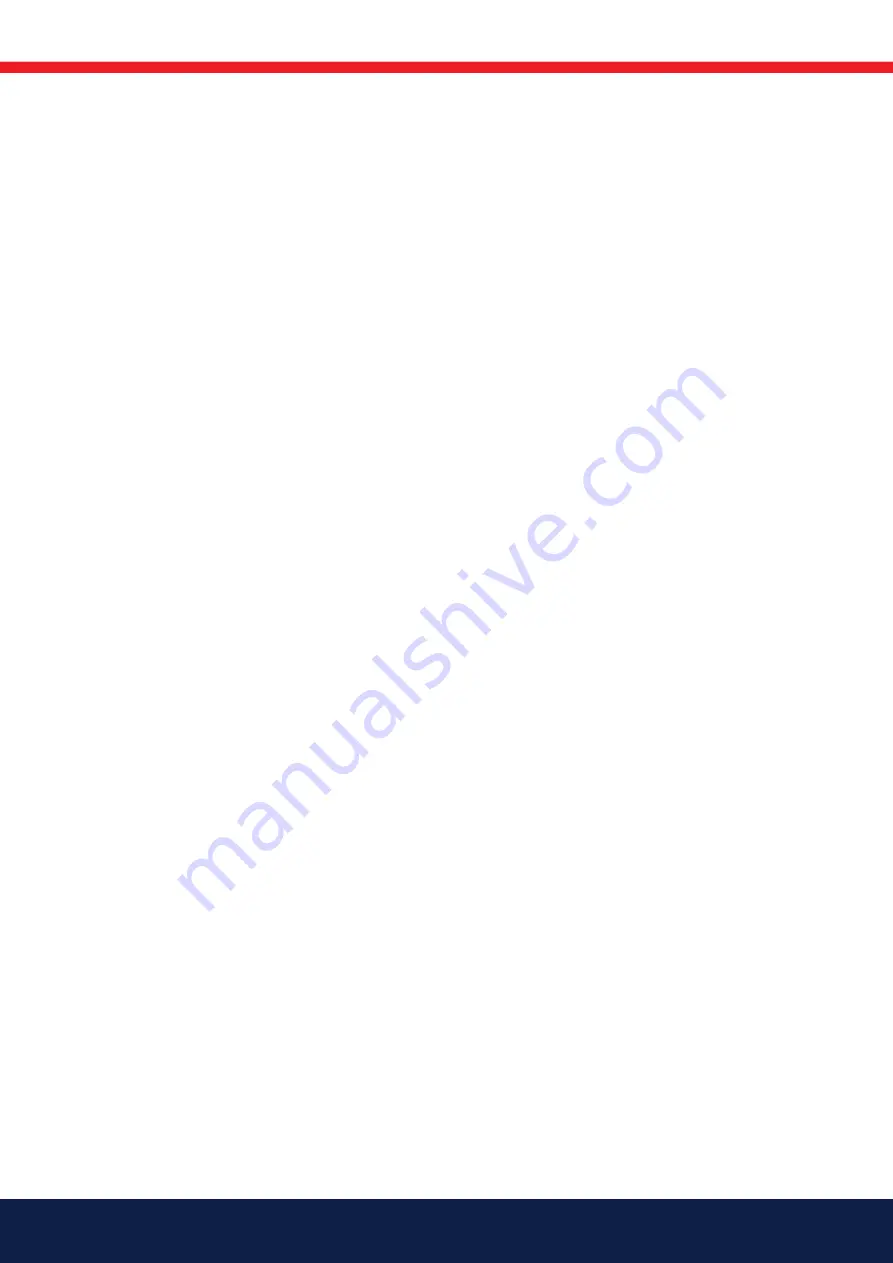
12
Bentone
172 515 03 2018-01-02
3. General instructions
3.1 General instructions
The installation of the gas burner must be carried out in accordance with
current regulations and standards. The installers of gas burners should
therefore be acquainted with all regulations and ensure that the installation
complies with the requirements. The installation, mounting and adjustment
should be made with the greatest care and only the correct gas should be
used.
3.2 Installation and maintenance
instructions
The maintenance instructions supplied with the burner must be kept at an
easily accessible location in the boiler room.
3.3 Instructions
The user should be thoroughly in-structed in the function of the gas burner
and the whole installation. The supplier must instruct the user.
3.4 Inspection and maintenance
See service schedule.
3.5 Start up
After the burner has been fitted to the boiler and the electric connection, the
leakage control, the venting and the electric function test have been carried
out, the burner will be ready for start-up.
Howerer, study the sections dealing with adjustments of multi-bloc,
combustion air and combustion head. Open the ball valve and switch on the
main switch. If the burner starts the actual adjustment can be made.
3.6 Commissioning of installation
Control of the combustion. The combustion quality is checked by means of a
flue gas analysis device. Adjust the burner to appr. 20%
excess air in accordance with the table. Check the flue gas temperature.
Calculate the efficiency. Check also the actual gas volume on the gas meter
so that the correct input is achieved.
Содержание BG 300 M-J/K-IP40
Страница 17: ...17 Bentone 172 515 08 2018 01 02 4 8 Gas nozzle Natural gas Propan Biogas UV detector 2 5 8 0 ...
Страница 36: ...36 Bentone 11 2 Wiring diagram BG300 BP JK IP 40 ...
Страница 46: ...14 EU Declaration of conformity Bentone Gasburners ...
Страница 49: ......
Страница 50: ......
Страница 51: ......
Страница 52: ...Enertech AB P O Box 309 SE 341 26 Ljungby www bentone se www bentone com ...