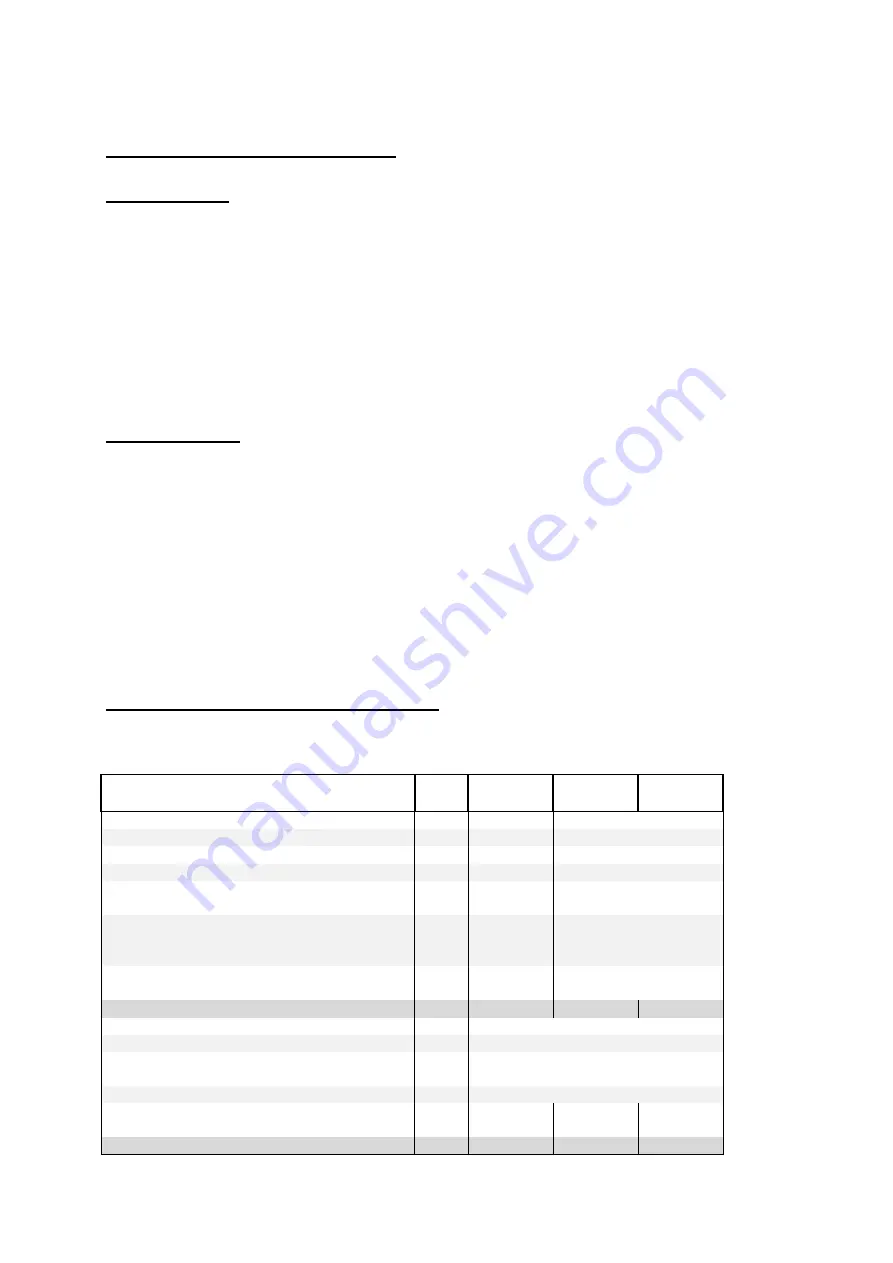
- 4 -
1. Boiler use and advantages
Use of the boiler:
The BENEKOV K14 hot water boiler is designed to heat small or low-energy houses, chalets and other
buildings whose thermal loss does not exceed 15 kW.
The BENEKOV K20 hot water boiler is designed to heat small or low-energy houses, chalets and other
buildings whose thermal loss does not exceed 20 kW.
The BENEKOV K25 hot water boiler is designed to heat small or low-energy houses, chalets and other
buildings whose thermal loss does not exceed 25 kW.
BENEKOV K14, K20 and K25 boilers are designed to burn wooden pellets.
Boiler advantages:
•
the boilers meet the requirements of boiler class 5 and ECODESIGN
•
high efficiency of the boilers
•
minimal environmental impact
•
automatic boiler operation
•
patented burner solution with self-cleaning furnace
•
automatic boiler ignition and extinguishing
•
mechanical delivery of the fuel from external feeder to the furnace
•
simple, time-efficient use and maintenance
•
low operating costs
•
modern design
2. Boiler technical specifications
Chart 1 Dimensions and technical parameters of the boilers
Boiler type
BENEKOV
K14
BENEKOV
K20
BENEKOV
K25
Weight
kg
215
310
Volume of the water tank
dm
3
45
70
Diameter of the flue pipe
mm
115
145
Boiler heat exchange surface
m
2
1,71
2,16
Fuel store capacity
dm
3
200
370
kg
120
222
Boiler dimensions: width
depth
height
mm
mm
mm
889
1035
1453
1256
1186
1453
Diameter of the fuel store replenishing
aperture
mm
542x388
635x690
Highest allowed operating pressure
bar
2,0
Testing pressure
bar
4,0
Recommended heating water operating
temperature
°C
65 - 80
Temperature controller setting range
°C
60 - 85
Hydraulic loss of the boiler:
∆ T = 10 K
∆ T = 20 K
mbar
mbar
5,72
1,64
19,07
4,71
23,84
5,89
Содержание K14
Страница 1: ...BOILER OPERATION AND INSTALLATION GUIDE BENEKOV K14 BENEKOV K20 BENEKOV K25 ...
Страница 9: ... 9 Fig 3 BENEKOV K14 boiler basic dimensions ...
Страница 10: ... 10 Fig 4 BENEKOV K20 and K25 boiler dimensions ...
Страница 17: ... 17 Fig 7 Position of the K14 boiler in a boiler room ...
Страница 33: ... 33 Fig 17 Diagram of electrical connection of XS20 burner of the K14 boiler ...
Страница 34: ... 34 Fig 18 Diagram of electrical connection of XS26 burner of the K20 and K25 boilers ...