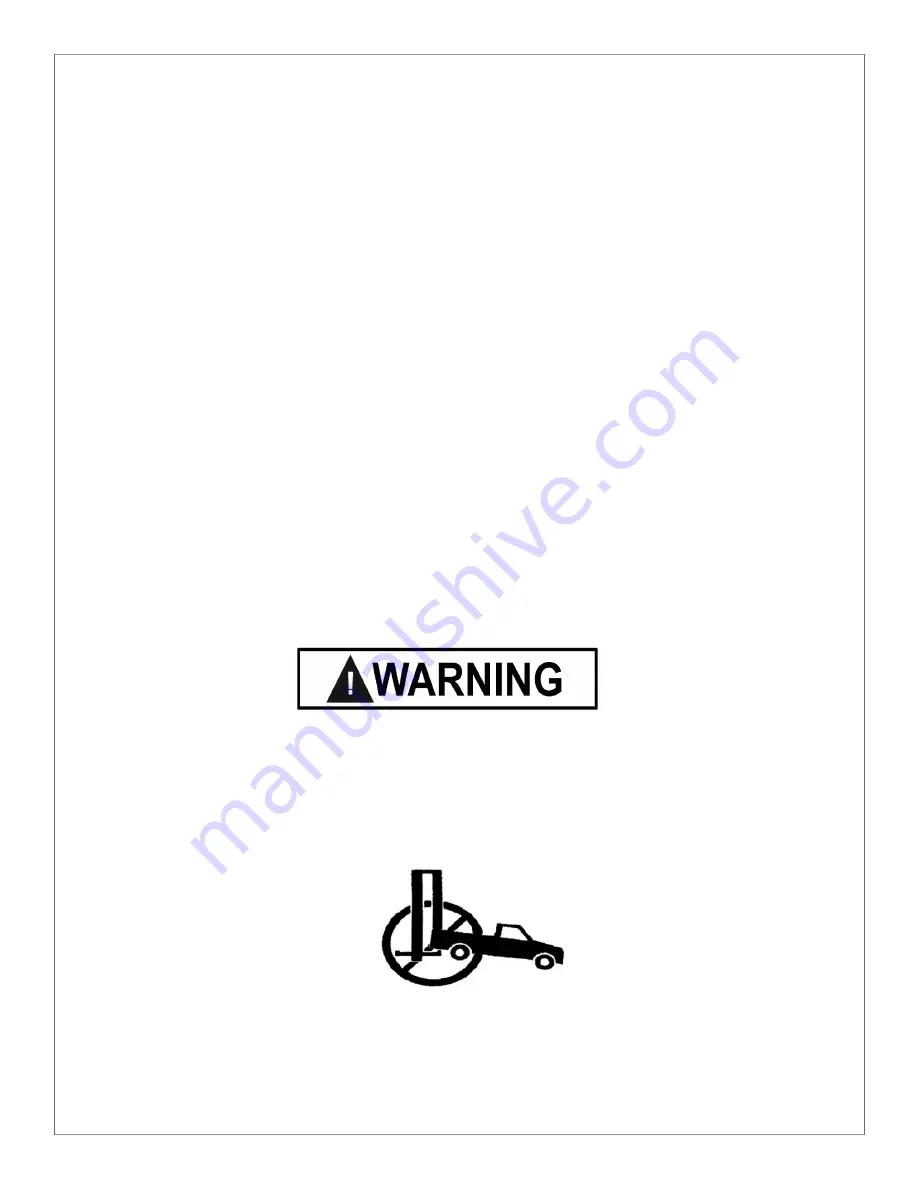
TO RAISE LIFT
Read operating and Safety manuals before using lift.
Always lift a vehicle according to the manufactures recommended lifting points.
Position vehicle between columns.
Adjust swing arms so that the vehicle is positioned with the center of gravity midway between lift arms.
Raise the vehicle by depressing button until the vehicle just lifts off the ground. Recheck to make sure
the vehicle is secure and all locking pins are lock in place.
Raise vehicle to desired height. Lower vehicle onto nearest safety,
Always ensure safeties are engaged before any attempt is made to work on or near vehicle.
TO LOWER THE LIFT
First raise the lift clear to the safeties.
Release safeties by pulling on the safety handle.
Be sure tool trays, stands or personnel are cleared from under the vehicle.
Lower vehicle by activating lowering handle on power unit.
Before removing vehicle from lift; position lift arms and supports to provide an unobstructed exit.
NEVER
, drive over lift arms.
REQUIRED MONTHLY MAINTENANCE
Check all arm adjusting locks for proper operation.
Check all cables connections, bolts and pins to insure proper mounting and torque.
Visually inspect safeties for proper operation.
Lubricate columns with grease.
Inspect all anchors bolts and retighten if necessary.
Check all columns for squareness and plumb.
Inspect all pivot arms pins making sure they are properly secure.
Check equalizer cable tension, and adjust if necessary.
If lift is equipped with over head cut-off switch, check for proper operation.
1.
WARNING!
: If cement anchor bolts are loose or any component of the lift is found to be defective,
DO NOT USE THE LIFT!!
2, Never operate the lift with any person or equipment below the vehicle.
3. Never exceed the rated lift capacity.
4. Always insure the safeties are engaged before any attempt is made to work on or near the vehicle.
5. Never leave lift in elevated position unless the safeties are engaged.
6. Do not permit electric motor to get wet! Motor damage caused by dampness is not covered under warranty.
NEVER LIFT ANY VEHICLE IN ANY MANNER WITH
LESS THE ALL FOUR (4) ARMS. RATED CAPACITY OF
EACH LIFT ARM IS NO GREATER THAT ONE FOURTH
(1/4) OF THE OVERALL LIFT CAPACITY.
33
Содержание XPR-7TR
Страница 11: ...11 FLOORPLAN CAPACITY MODEL XPR 7TR Dim A 3683mm 145 CAPACITY 7 000 Lbs ...
Страница 12: ...12 MAIN ASSEMBLY VIEW ...
Страница 24: ...24 ...
Страница 28: ......
Страница 31: ...31 OPTIONAL EQUIPMENT INSTALLATION ...
Страница 35: ...35 ...
Страница 36: ...36 ...
Страница 47: ...47 ...