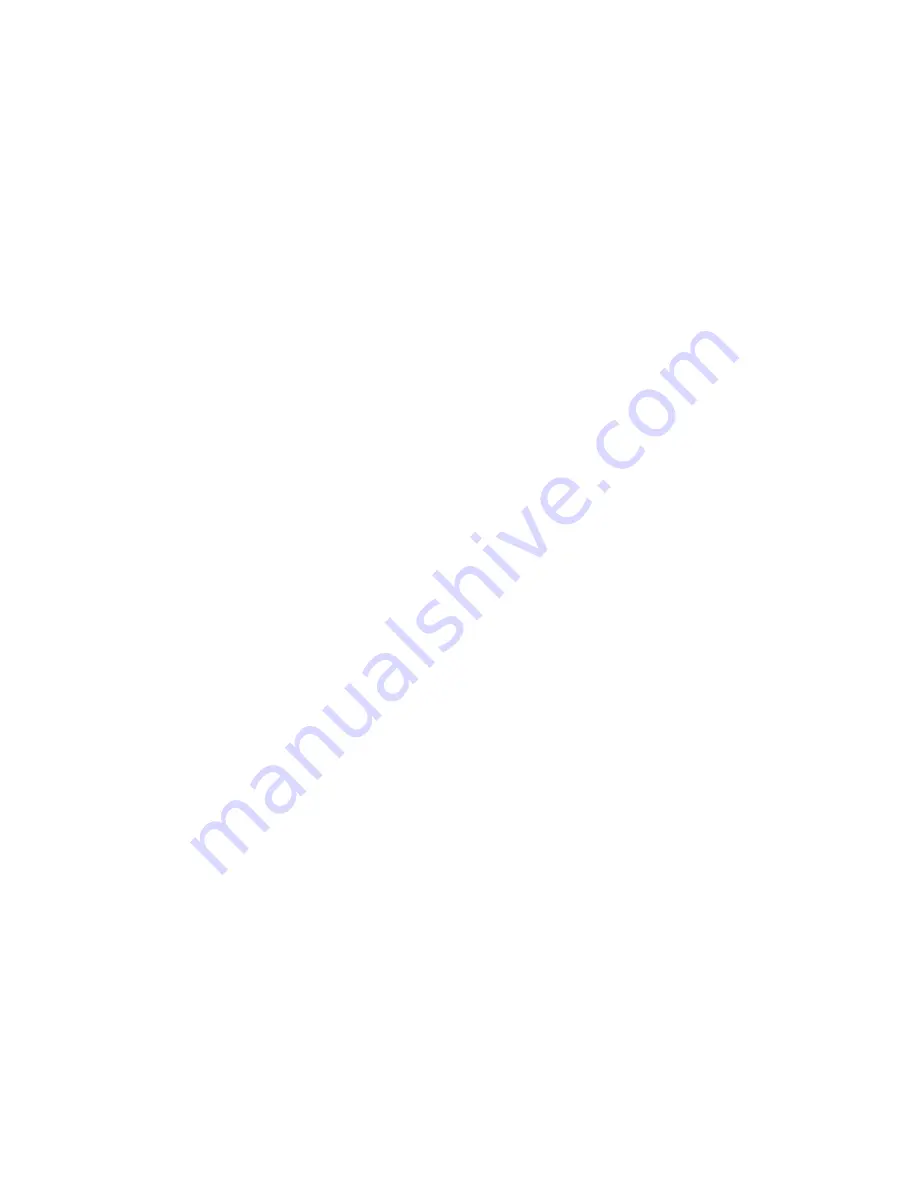
2
RELEASING
When the handle or operating lever is moved in a
counterclockwise direction the force above the piston is
decreased. The air pressure beneath will then lift the piston,
moving it away from the exhaust valve. With the exhaust
passage open, air pressure in the service line will exhaust
out the exhaust port of the valve.
PREVENTIVE MAINTENANCE
Important:
Review the warranty policy before performing
any intrusive maintenance procedures. An extended
warranty may be voided if intrusive maintenance is
performed during this period.
Because no two vehicles operate under identical
conditions, maintenance and maintenance intervals will
vary. Experience is a valuable guide in determining the best
maintenance interval for any one particular operation.
Visually check for physical damage to the brake valve such
as broken air lines and broken or missing parts.
Every 3 months, 25,000 miles or 900 operating hours
perform Operating and Leakage Tests.
SERVICE CHECKS
OPERATING TEST
Connect an accurate test gauge to a delivery port. When
the handle is moved to the fully applied position, the gauge
should register full reservoir pressure. NOTE: Some valves
may be preset to deliver lower than reservoir pressure;
however, the standard valves generally used on tractors are
set to deliver full reservoir pressure. Intermediate positions
should deliver proportional intermediate pressures. Upon
release, the gauge should immediately register zero.
LEAKAGE TEST
Locate the exhaust port or exhaust line and apply a soap
solution. (It is common practice to connect a line from
the valve exhaust port to a location remote from the
immediate driver’s area.) With the valve in the released
position, exhaust leakage should not exceed a 1" bubble
in 5 seconds (100 sccm).
With the valve fully applied, leakage at the exhaust
should not exceed a 1" bubble in 3 seconds (175 sccm).
If the valve does not function as described or leakage is
excessive, it is recommended that it be replaced with a
new or remanufactured unit, or repaired with genuine parts
available at Bendix outlets.
REMOVING AND INSTALLING
REMOVING
1. Block and hold vehicle by means other than air
brakes.
2. Drain air brake system.
3. If remote-operated type valve, disconnect the operating
mechanism.
4. Disconnect air lines from valve.
5. Remove mounting clamp bolts, clamp, and then valve.
INSTALLING
1. Check and clean air lines to valve.
2. Operating mechanism for remote type should be
checked functionally and for proper adjustment.
3. Mount valve with clamp and mounting bolts.
4. Tighten mounting bolts evenly to approximately 200
inch pounds torque (3/8-16 bolt torque 180-220 inch
pounds.)
5. If remote type valve, connect operating mechanism.
DISASSEMBLY
HANDLE OPERATED VALVE
1. Drive out the spirol pin and remove the handle, head,
and head seal o-ring.
2. Remove handle o-ring.
3. Remote Operated Type Valve: Remove set screw, head
and head seal o-ring.
4. Remove adjusting ring lock washer.
5. Remove cap screws that hold body and cover together;
separate cover from body.
6. Remove gasket and graduating spring.
7. Remove cam and cam follower from cover.
8. Unscrew and remove adjusting ring.
9. Remove piston and piston return spring from body.
10. Remove piston o-ring.
11. Remove inlet and exhaust insert screws and lock
washers, then insert and o-ring seal.
12. The inlet and exhaust valve insert can be disassembled
if desired or necessary.
13. Insert some object such as a cap screw in the supply
port to hold the inlet valve on its seat.
14. Depress the exhaust valve guide and spring; remove
the exhaust valve.
15. Remove stem with inlet valve from inlet seat and
remove inlet valve from stem.
CLEANING AND INSPECTION OF PARTS
1. Clean all metal parts in mineral spirits.
2. Wipe rubber parts clean.
3. Inspect valve seats for nicks or burrs.
4. Check all springs for distortion, cracks, and
corrosion.
5. All rubber parts should be inspected for wear or
deterioration.
6. Replace all parts not considered serviceable during
their inspection with genuine Bendix replacement
parts.