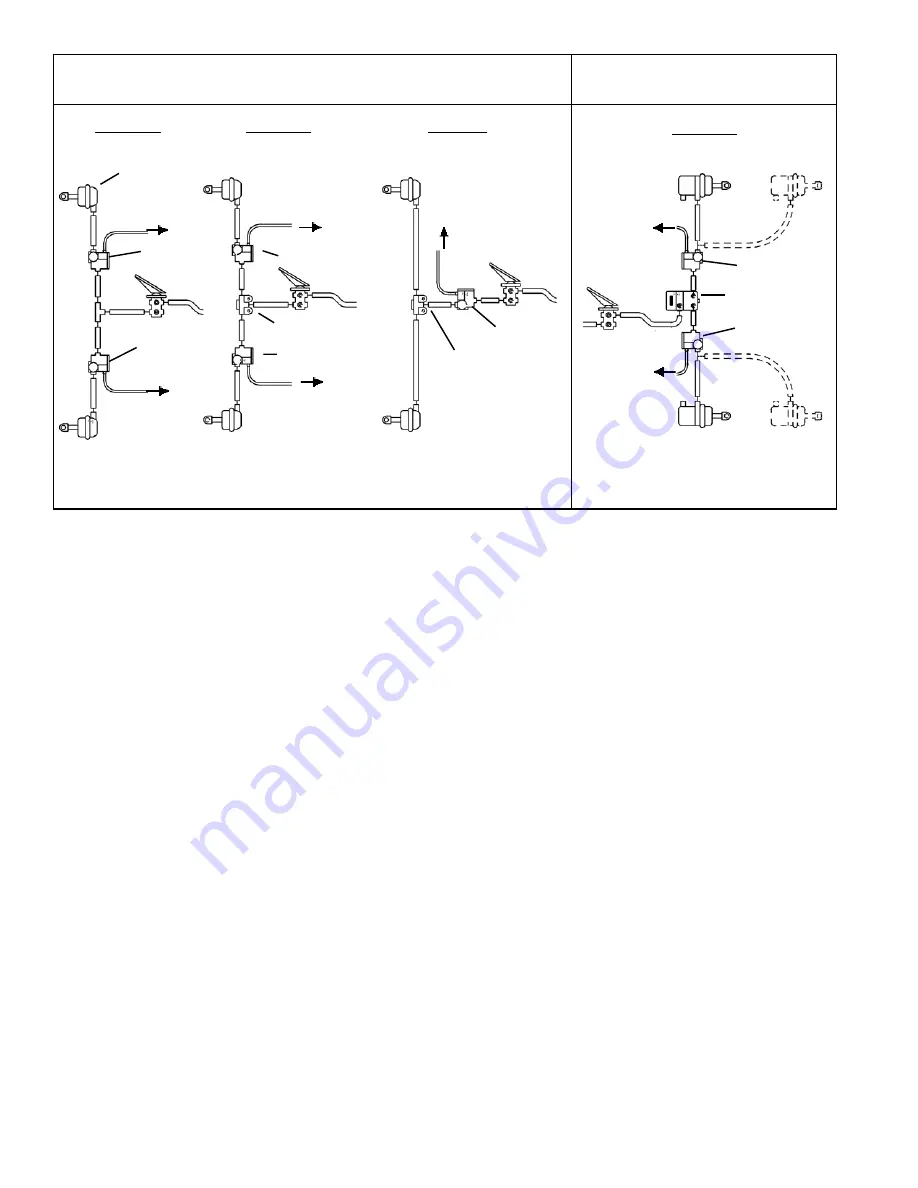
2
Service &
Spring Brake
Chamber
To Antilock
Controller
Controller/Relay
Assembly
M-32
™
or M-32QR
™
Modulator
M-32
™
or M-32QR
™
Modulator
To Antilock
Controller
FIGURE 3: TYPICAL WHEEL AND AXLE CONTROL SYSTEMS
NOTE: use of a quick release valve is not typically required with the M-32QR
™
modulator. Refer to vehicle specifications for recommended configuration.
NON-ANTILOCK HOLD
(Figure 5)
When the desired air pressure is attained in the service
brake chambers, the brake system is in the Holding position.
In the Holding position, both solenoids in the modulator
remain de-energized and the balance of the internal
components remain in the same position as they assumed
during application.
NON-ANTILOCK EXHAUST
The manner in which air exhausts through the modulator
differs depends upon how rapidly the brake application is
released by the driver.
Normal Exhaust (Figure 6) - During a normal, relatively
“slow” brake release, air moves back through the modulator
in the reverse direction as it flowed during application. The
internal components of the modulator will remain in the same
position as they assumed during application until air pressure
decreases to approximately one half psi, at which time the
supply diaphragm will seat on the supply passage. A
relatively small amount of air will generally be expelled from
the modulator exhaust port during “slow” brake release.
Rear Axle System
FUNCTIONAL CHECK
A wiring harness connects the vehicle modulators to the
controller. The ABS controller is able to simultaneously and
independently control the individual modulators. When vehicle
power is supplied to the ABS ECU, a modulator "chuff" test
is performed. When the brake pedal is depressed and the
ignition turned on, the modulator "chuff" test can be heard.
This test will verify if the modulator is functioning
pneumatically correct. The modulators will exhaust air in
the sequence of right front, left front, right rear, left rear. If
they do not follow this sequence, proceed with modulator
troubleshooting.
OPERATION
NON-ANTILOCK BRAKE APPLICATION
(Figure 4)
During normal, non antilock braking, both solenoids are de-
energized (no electrical power). Brake application air enters
the Supply port of the modulator and flows to the exhaust
diaphragm. Air pressure, along with spring force, seats the
exhaust diaphragm on the exhaust passage, thus preventing
the escape of service air. Simultaneously, application air
flows to the supply diaphragm and forces it away from its
seat. Air flows past the open supply port and out the
modulator delivery port to the service brake chambers.
Front Axle Systems
Axle Control
Wheel Control
Wheel Control
Service Brake
Chamber
M-32
™
or M-32QR
™
Modulator
M-32
™
or M-32QR
™
Modulator
Quick Release Valve
M-32
™
or
M-32QR
™
Modulator
Service Brake
Chamber
Quick
Release
Valve
To Antilock
Controller
To Antilock
Controller
To Antilock
Controller
or
Service Brake
Chamber
M-32QR
™
Modulator
To Antilock
Controller
M-32QR
™
Modulator
Service Brake
Chamber
Wheel Control
or
To Antilock
Controller