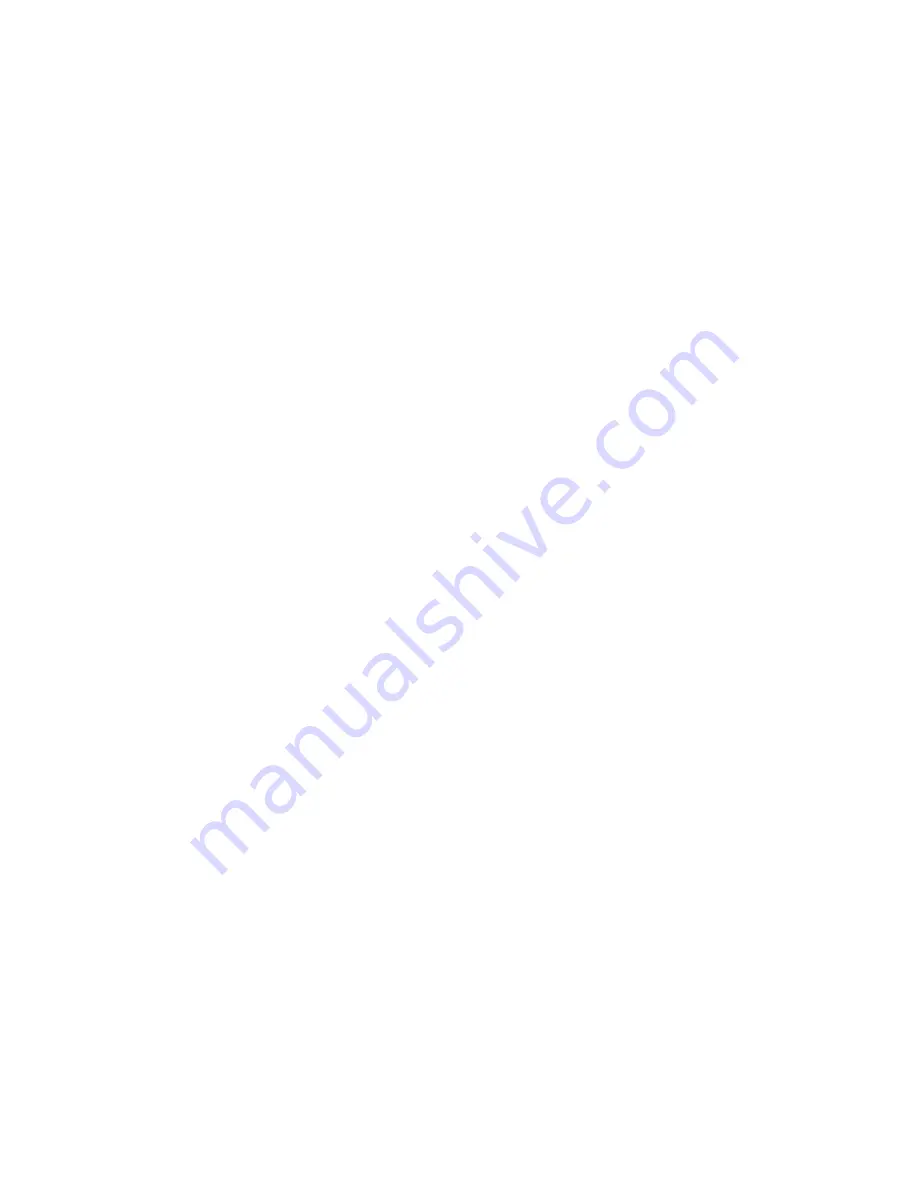
7
C. Apply a soap solution around each diaphragm cover.
Leakage should not exceed a 1" bubble in less than 3
seconds. If leakage exceeds the specified maximum,
tighten the diaphragm cap screws and re-test. If the
leakage remains excessive after re-testing, replace the
modulator.
OPERATION TESTING
To properly test the function of the modulator will require 2
service technicians.
1. Park the vehicle on a level surface and block or chock
the wheels. Release the parking brakes and build the
air system to governor cut out.
2. Turn the engine ignition key to the OFF position then
make and hold a full brake application.
3. With the brake application held and a service technicians
posted at one of the modulators, turn the vehicle ignition
key to the ON position. ONE OR TWO SHORT bursts
of air pressure should be noted at the modulator exhaust.
Repeat the test for each modulator on the vehicle. If at
least a single burst of exhaust is not noted or the exhaust
of air is prolonged and not short, sharp and well defined,
perform the Electrical Tests.
ELECTRICAL TESTS
1. Before testing the solenoid assembly of a "suspect"
modulator, its location on the vehicle should be confirmed
using the Trouble Shooting or Start Up Procedure for the
specific antilock controller in use. (See the Service Data
Sheet for the antilock controller for this procedure.)
2. Proceed to the modulator in question and inspect its
wiring connector. Disconnect the connector and test the
resistance between the pins ON THE MODULATOR.
Refer to figure 9.
A. HOLD to SOURCE: Read 3.5 to 5 OHMS
B. EXHAUST to SOURCE: Read 3.5 to 5 OHMS
C. EXHAUST to HOLD: Read 7 to 10 OHMS
D. Individually test the resistance of each pin to vehicle
ground and note there is NO CONTINUITY.
If the resistance readings are as shown, the wire harness
leading to the modulator may require repair or
replacement. Before attempting repair or replacement
of the wire harness, refer to the test procedures specified
for the antilock controller in use for possible further testing
that may be required to substantiate the wire harness
problem. If the resistance values are NOT AS SHOWN
ABOVE, replace the modulator.
VALVE REMOVAL
1. Park the vehicle on a level surface and block the wheels
and/or hold the vehicle by means other than the air
brakes.
2. Drain the air pressure from all vehicle reservoirs.
3. Identify and mark or label all air lines and their respective
connections on the valve to facilitate ease of installation.
4. Disconnect both air lines and the electrical connector.
5. Remove the valve from the vehicle.
VALVE INSTALLATION
1. Install all air line fittings and plugs making certain thread
sealing material does not enter the valve.
2. Install the assembled valve on the vehicle.
3. Reconnect both air lines to the valve using the
identification made during VALVE REMOVAL step 3.
4. Reconnect the electrical connector to the modulator.
5. After installing the valve, test all air fittings for excessive
leakage and tighten as needed.
M-21
™
MODULATOR TECHNICAL INFORMATION
Porting -
1 Supply Port (from brake,
relay or quick release
valve)
1 Delivery Port (brake
actuator)
Solenoid Voltage -
12 Volts DC Nominal
Maximum Operating Pressure - 150 psi Gauge
Operating Temp. Range -
-40 to +185 Fahrenheit
Pressure Differential -
1 psi maximum
Содержание M-21
Страница 10: ...10...
Страница 11: ...11...
Страница 12: ...12 BW1664 2004 Bendix Commercial Vehicle Systems LLC All rights reserved 6 2004 Printed in U S A...