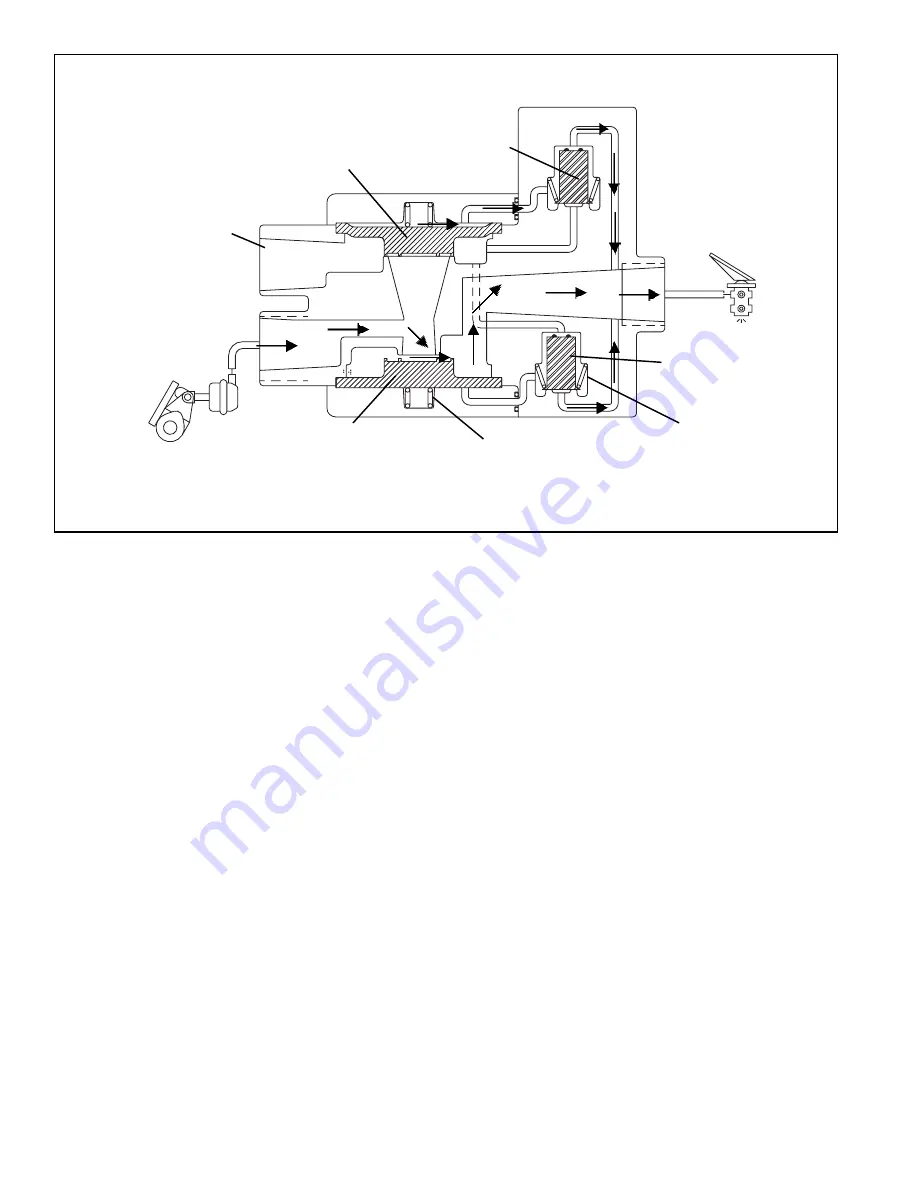
4
NON-ANTILOCK EXHAUST
The manner in which air exhausts through the modulator
differs, depending upon how rapidly the brake application is
released by the driver.
Normal Exhaust
(Figure 5)
- During a normal, relatively
"slow", brake release, air moves back through the modulator
in the reverse direction as it flowed during application. The
internal components of the modulator will remain in the same
position as they assumed during application until air pressure
decreases to approximately one half psi, at which time the
supply diaphragm will seat on the supply passage. Air will
generally not be expelled from the modulator exhaust port
during normal brake release.
Rapid Exhaust
(Figure 6) -
The rapid exhaust operation
described in the following text only occurs when the
modulator is controlling two type 30 (or larger) service
chambers. During a very rapid brake release the modulator
will exhaust air in a different manner. An example of this
would be the case if the driver made a severe brake
application then lifted his foot from the foot valve. During a
rapid brake release, air from the exhaust diaphragm flows
back through the open exhaust solenoid and to the
application device's exhaust. With pressure removed from
the control side of the exhaust diaphragm, air, returning to
the modulator from the service chambers, lifts the exhaust
diaphragm from its seat. Returning air flows past the open
exhaust and out the modulator exhaust port. Air will also
flow past the open supply diaphragm and back to the
application device's exhaust.
ANTILOCK OPERATION
GENERAL
If a service brake application is made and the antilock system
detects an impending wheel lockup, the antilock controller
will immediately begin modification of the brake application
using the modulator.
In order to modify the brake application, the coils of the two
solenoid valves contained in the modulator are energized or
de-energized in a pre programmed sequence by the antilock
controller. When a solenoid coil is energized, a shuttle within
the solenoid moves, and depending upon the function of the
specific solenoid, it either opens or closes thereby causing
the exhaust or re-application of air pressure to the brake
actuator. The solenoids in the modulator are controlled
independently by the antilock controller. By opening and
closing the solenoid valves in the modulator, the antilock
controller is able to simulate what the driver does when he
"pumps the brakes". It must be remembered, however, that
unlike the driver the antilock controller is able to "pump"
each modulator, along with the brakes connected to it,
independently and with far greater speed and accuracy.
FIGURE 5 -
M-21
™
, M-22
™
MODULATOR NON-ANTILOCK EXHAUST OF SERVICE BRAKES (NORMAL)
BRAKE VALVE
SPRING
SUPPLY
DIAPHRAGM
SUPPLY
SOLENOID
SPRING
EXHAUST
DIAPHRAGM
EXHAUST
SOLENOID
BRAKE
CHAMBER
EXHAUST PORT
Содержание M-21
Страница 10: ...10...
Страница 11: ...11...
Страница 12: ...12 BW1664 2004 Bendix Commercial Vehicle Systems LLC All rights reserved 6 2004 Printed in U S A...