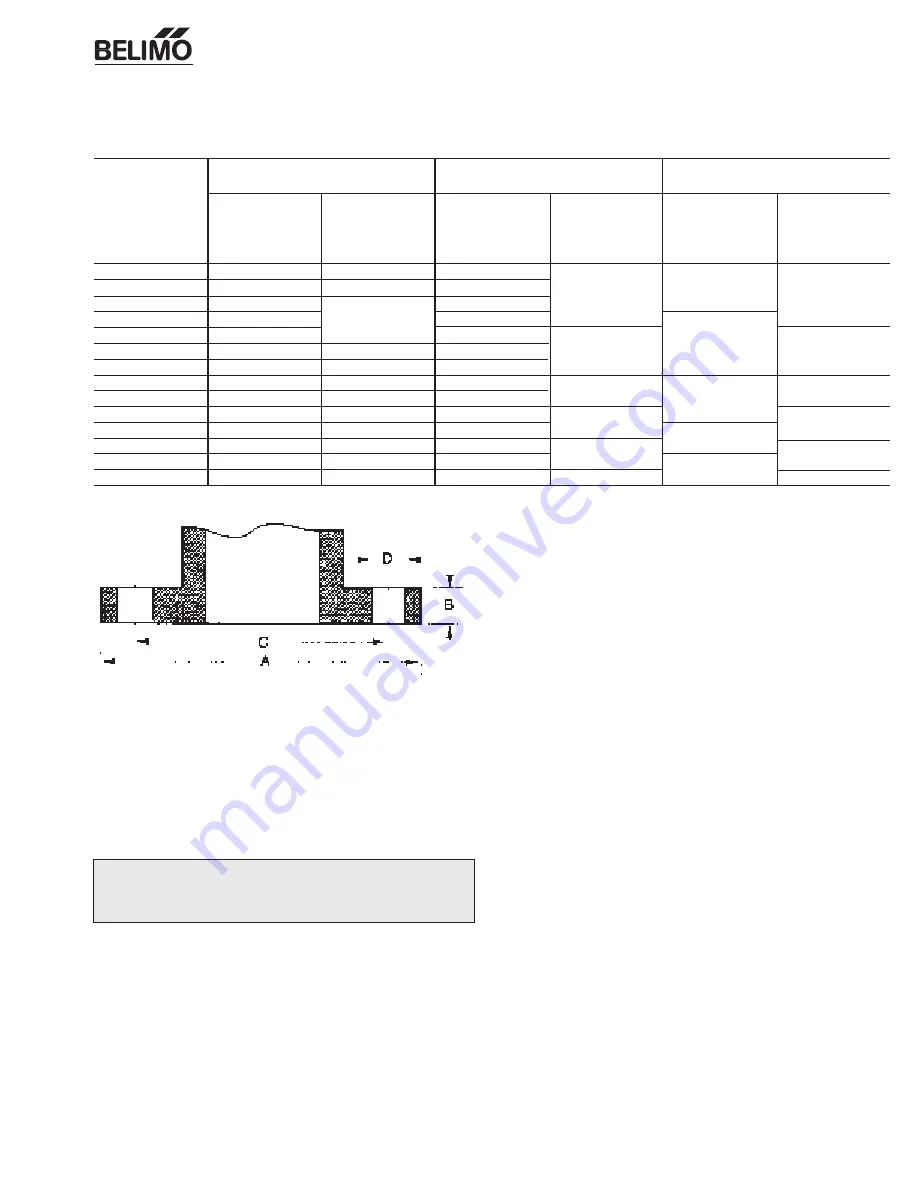
39
Installation Recommendations
F6…, F7… Series Butterfly Valves
Flange Bolting Recommendations
Flange Detail for Ansi B16.5 Pipe Flanges
Flanges
Drilling
Bolting
A
B
C
D
Nominal
Flange
Flange
Diameter of
Diameter of
Number
Diameter
Pipe Size
Diameter
Thickness
Bolt Circle
Bolt Holes
of Bolts
of Bolts
2”
6”
¾”
4¾”
4
2½”
7”
⁷⁄₈
”
5½”
¾”
¹⁄₈
”
3”
7½”
6”
4”
9”
¹⁵⁄₁₆
”
7½”
5”
10”
8½”
8
6”
11”
1”
9½”
⁷⁄₈
”
¾”
8”
13½”
1
¹⁄₈
”
11¾”
10”
16”
1
³⁄₁₆
”
14¼”
1”
⁷⁄₈
”
12”
19”
1¼”
17”
12
14”
21”
1
³⁄₈
”
18¾”
1
¹⁄₈
”
1”
16”
23½”
1
⁷⁄₁₆
”
21¼”
16
18”
25”
1
⁵⁄₈
”
22¾”
1¼”
1
¹⁄₈
”
20”
27½”
1
¹¹⁄₁₆
”
25”
20
24”
32”
1
⁷⁄₈
”
29½”
1
³⁄₈
”
1¼”
Pre-Installation Procedure
1. Remove any protective flange covers from the valve.
2. Inspect the valve to be certain the waterway is free from dirt
and foreign matter. Be certain the adjoining pipeline is free
from any foreign material such as rust and pipe scale or weld-
ing slag that could damage the seat and disc sealing surfaces.
3. Any actuator should be mounted on the valve prior to installa-
tion to facilitate proper alignment of the disc in the valve seat.
4. Check the valve identification tag for materials, and operating
pressure to be sure they are correct for the application.
WARNING! Personal injury or property damage may result
if the valve is installed where service condi-
tions could exceed the valve ratings.
5. Check the flange bolts or studs for proper size, threading, and
length.
6. These valves are designed to be installed between ANSI
Class 125/150 flanges.
7. Carefully follow installation using welded flanges: on page 30
of this document.
8. Follow ASME flange alignment standards:
Section 335.1.1 Alignment
a) Piping Distortions:
Any distortion of piping to bring into alignment for joint
assembly which introduces a detrimental strain in equip-
ment or piping components is prohibited.
b) Flange Joints:
Before bolting up, flange faces shall be aligned to the
design plane within
¹⁄₁₆
in/ft measured across any diameter;
flange bolt holes shall be aligned within
¹⁄₈
” maximum offset.
9. When observed during assembly, the flange faces shall be
parallel within 1°, and the force required to align pipe axes
shall not exceed 10 lb/ft per inch of NF bolts and nuts shall be
fully engaged.
Valve Installation Procedure
Position the connecting pipe flanges in the line to insure proper
alignment prior to valve installation. Spread the pipe flanges
apart enough to allow the valve body to be located between the
flanges without actually contacting the flange surfaces (See
Figure 1). Exercise particular care in handling the valve so as to
prevent possible damage to the disc or seat faces.
1. For Lug style valves:
a. Place the valve between the flanges.
b. Install all bolts between the valve and the mating flanges.
Hand tighten bolts as necessary.
2. Before completing the tightening of any bolts, the valve should
be centered between the flanges and then carefully opened
and closed to insure free, unobstructed disc movement
(see Figure 2).
3. Using the sequence shown in Figure 3, tighten the flange bolts
70103-00001D
-
03/08
-
Subject
to
change.
©
Belimo
Air
controls
(USA),
Inc.