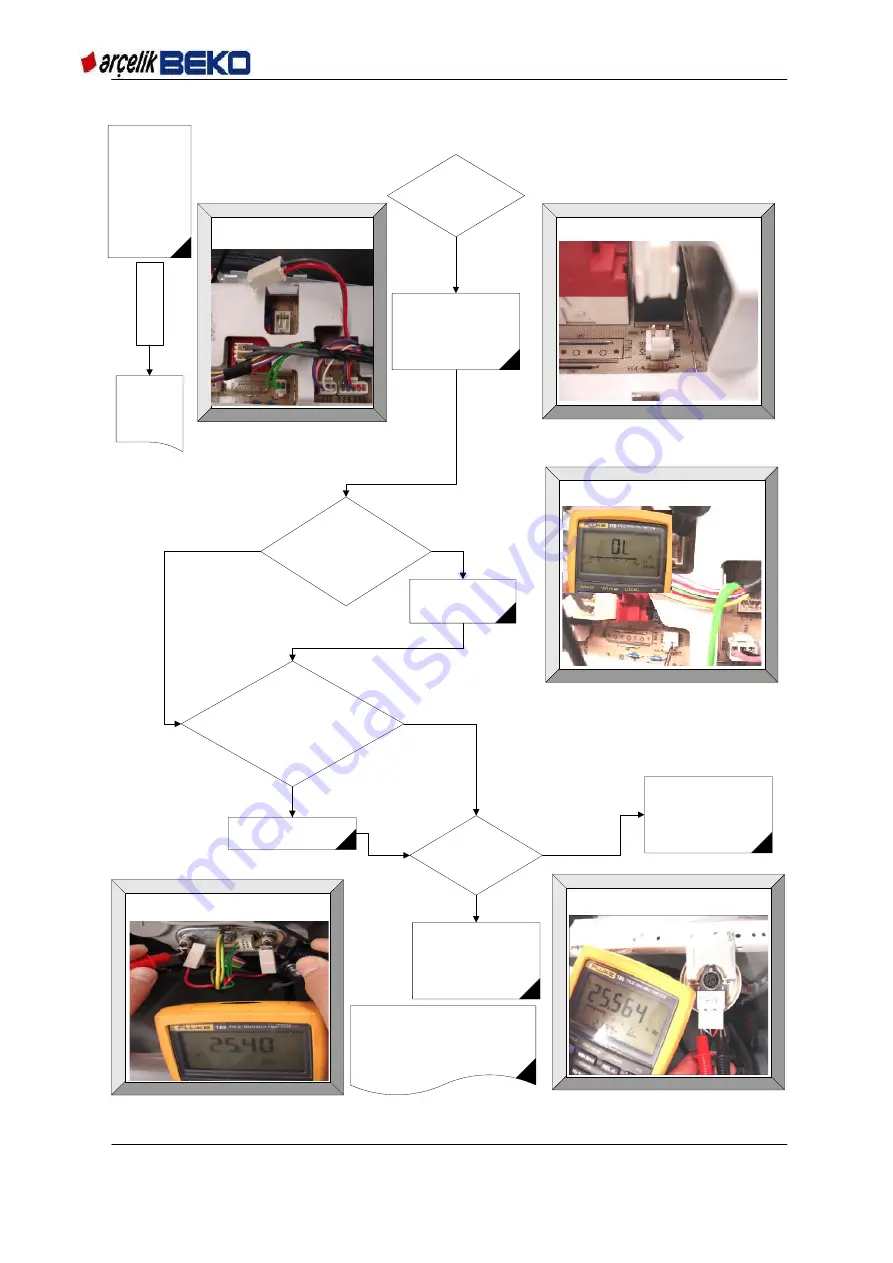
B7S B7SLED WASHING MACHINE SERVICE HAND BOOK
74
Yes
Replace control card.
No
Open the rear cover of the machine.
Measure heater resistance by removing at
least one of the heater terminals; is the
resistance 25 Ohms? (Picture E2-4)
Replace the heater
Is there E2 error?
Check to see if there is any short
circuit between the first pins of
both connectors.
(Picture E2-3)
No
Yes
Check water level sensor.
Measure the frequency
between pins 1 and 3 while
the machine is empty and
energized. It should be
around 25560 Hertz. (Picture
2-5)
Does the heater operate
although there is no
water?
Yes
Remove the panel for a
comfortable measuring.
Remove KN5 (Picture E2-1)
Heater socket and KN8
(Picture E2-2) Tacho socket.
Yes
You may start the washing
program.
No
Important Note:
The washing machine makes cold washing
and ends the program before the heater is
activated in NTC open circuit / short circuit
and Heater open circuit conditions, i.e. if
there is E1, E2 or E3 error.
PICTURE E2-4: One of the cables on the
heater is removed (left) and heater resistance
is measured.
* Heater open
circuit error
E2
0
0
0
1
0
*Does not heat
water.
*Machine boiled
the water once,
but now it does
not heat at all.
PICTURE E2-1: Heater socket on
the KN5 card is removed.
PICTURE E2-2: KN8 tacho socket is removed.
PICTURE E2-5: Water level sensor is being
checked
PICTURE E2-3: Short circuit check is being
made between KN8-1 pin and KN5-1 pin.
Содержание B7S-B7SLED
Страница 69: ...B7S B7SLED WASHING MACHINE SERVICE HAND BOOK 69 11 FAILURE FLOW DIAGRAM Revisions Rev 01 07 10 2012 ...
Страница 90: ...B7S B7SLED WASHING MACHINE SERVICE HAND BOOK 90 ...
Страница 91: ...B7S B7SLED WASHING MACHINE SERVICE HAND BOOK 91 12 POWER CIRCUIT DIAGRAM ...
Страница 92: ...B7S B7SLED WASHING MACHINE SERVICE HAND BOOK 92 ...
Страница 93: ...B7S B7SLED WASHING MACHINE SERVICE HAND BOOK 93 ...
Страница 94: ...B7S B7SLED WASHING MACHINE SERVICE HAND BOOK 94 ...
Страница 95: ...B7S B7SLED WASHING MACHINE SERVICE HAND BOOK 95 13 EXPLODED DRAWINGS 13 1 Body Group 13 2 Control Group ...
Страница 96: ...B7S B7SLED WASHING MACHINE SERVICE HAND BOOK 96 13 3 Water System 13 4 Visual Group ...
Страница 97: ...B7S B7SLED WASHING MACHINE SERVICE HAND BOOK 97 13 5 Visual Group 13 6 Front Wall Group ...
Страница 98: ...B7S B7SLED WASHING MACHINE SERVICE HAND BOOK 98 13 7 Front door 13 8 Driving Group ...