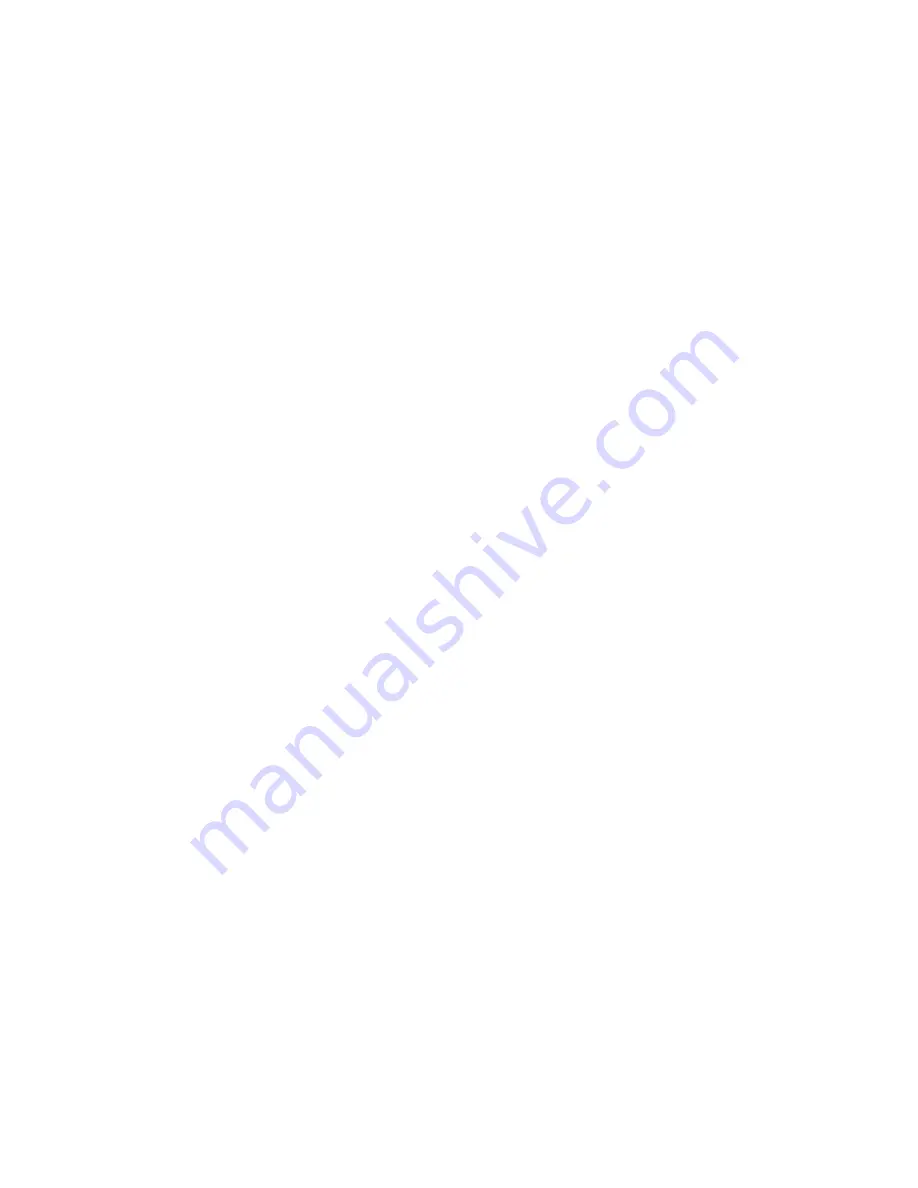
24
BL20K SERIES REV E 2013
5.4
MOTHERBOARD ( continued )
5.4.2
The variable frequency 45 to 500 Hertz square-wave is generated on the Motherboard. A CMOS phase
locked loop (U5), and 8 bit counter (U6) and Voltage Controlled Oscillator (U7) are the basis for the square-wave
generator. The front panel frequency control sets a DC voltage which determines the frequency of the VCO. The
VCO generates a square-wave at a frequency between 45 and 500 Hertz. This square-wave is used as a
reference signal for the PLL. The frequency of the VCO is multiplied by a factor of 256 by the PLL. The resultant
is used as a clock signal for the 8 bit counter.
5.4.3
In order to produce data in the form of a sinewave, a "Look-up" table is stored in a PROM on each phase
control card. The outputs of the 8 bit counter are tied to the address lines of each PROM. As the clock runs, the
data in the PROMS are clocked into the D/A convertors. This action produces a series of steps at the output of
the D/A convertor that approximate a sinewave. Further filtering produces a clean sinewave at the frequency of
the VCO. Phase displacement is determined by the PROM data.
5.4.4
The mother board also produces a triangle-wave signal that is common to the PWM modulators contained
on the phase control cards discussed later.
5.4.5
All inter-connection between circuits and controls are provided via the Motherboard. Four 22 pin card
edge connectors are present for the installation of 3 phase control cards and a GPIB interface card. Distribution
of all low voltage supplies is via the Motherboard.
5.5
OUTPUT INVERTER
5.5.1
The 3 output inverters (3 phase units) are based on a half bridge topology. A 600 volt, 100 amp, IGBT
module (1200V for 20K) is connected between the +/-250 Vdc rails. The drive signal to the inverter is a "sine
weighted" Pulse Width Modulated (PWM), isolated rectangular pulse train. The output of the half bridge is a 20
KHz pulse train that swings 500 volts peak-to-peak and has a varying duty cycle based on the modulating signal
(sinewave generator). This output is filtered by a low pass network. The result is a sinewave voltage that is an
amplified version of the sinewave signal.
5.5.2
Pulse Width Modulation is performed by the individual phase control cards. The tri-wave signal generated
by the Motherboard is distributed to each phase control card. Components U7, U12, U13, and U14 form a
modulator circuit that provides a dual polarity PWM signal that is applied to opto-coupled driver IC's U17 and U18.
These driver IC's provide boosted, isolated, drive for the upper and lower IGBT of the output invertor. The two
inputs to the modulator are the 20 KHz tri-wave and the locally generated sine-wave.
5.5.3
The driver IC's provide short circuit protection via an isolated fault output. This circuit detects the VCE
voltage of the upper and lower IGBT. If the output of the inverter is shorted the IGBT's collector to the emitter
voltage will increase and trigger the short circuit detection. The fault detect signal is used to set a latching lock
out that turns off the PWM drive signals. The latch logic is comprised of U9, U10, U12 on the Motherboard. The
latch must be reset by cycling power.
5.5.4
The output amplitude of each phase is also regulated by the phase control card. A sample of the output
voltages fed to an RMS to DC convertor (U4). The resultant DC voltage is compared to a reference DC voltage
set by the front panel voltage control or remote interface. This comparison is performed by U3a and is integrated
to provide an error signal to control the amplitude of the sinewave signal fed to the PWM modulator.
Compensation for load line (wire) drops performed by summing in a signal form
the current monitor. The more
current drawn, the more correction is provided. This compensation is adjustable via the front panel.
5.6
METERING
5.6.1
Metering is provided by DC signals taken from the phase control cards. These signals are derived from
the voltage and current monitoring circuits. These signals are attenuated and applied to the front panel DVM's.
The frequency display derives it's data from the VCO signal.
5.7
MISCELLANEOUS
5.7.1
Internal heat sink temperature is monitored via an sensor mounted to the extrusion. The sensor is
normally open but will close when a safe temperature is exceeded. When this sensor closes the PWM signal is
eliminated by setting the same latch used by the short circuit protection.
Содержание BL20000 Series
Страница 18: ...13 BL20K SERIES REV E 2013 Figure 3 2 Typical BL 20000 Front and Rear Panel Views ...
Страница 31: ......
Страница 32: ...26 BL20K SERIES REV E 2013 THIS PAGE INTENTIONALLY BLANK ...
Страница 50: ...6 1 SECTION 6 DRAWINGS ...
Страница 51: ......
Страница 52: ......
Страница 53: ......
Страница 54: ......
Страница 55: ......
Страница 56: ......
Страница 57: ......
Страница 58: ......
Страница 59: ......
Страница 60: ......
Страница 61: ......
Страница 62: ......
Страница 63: ......
Страница 64: ......
Страница 65: ......
Страница 66: ......