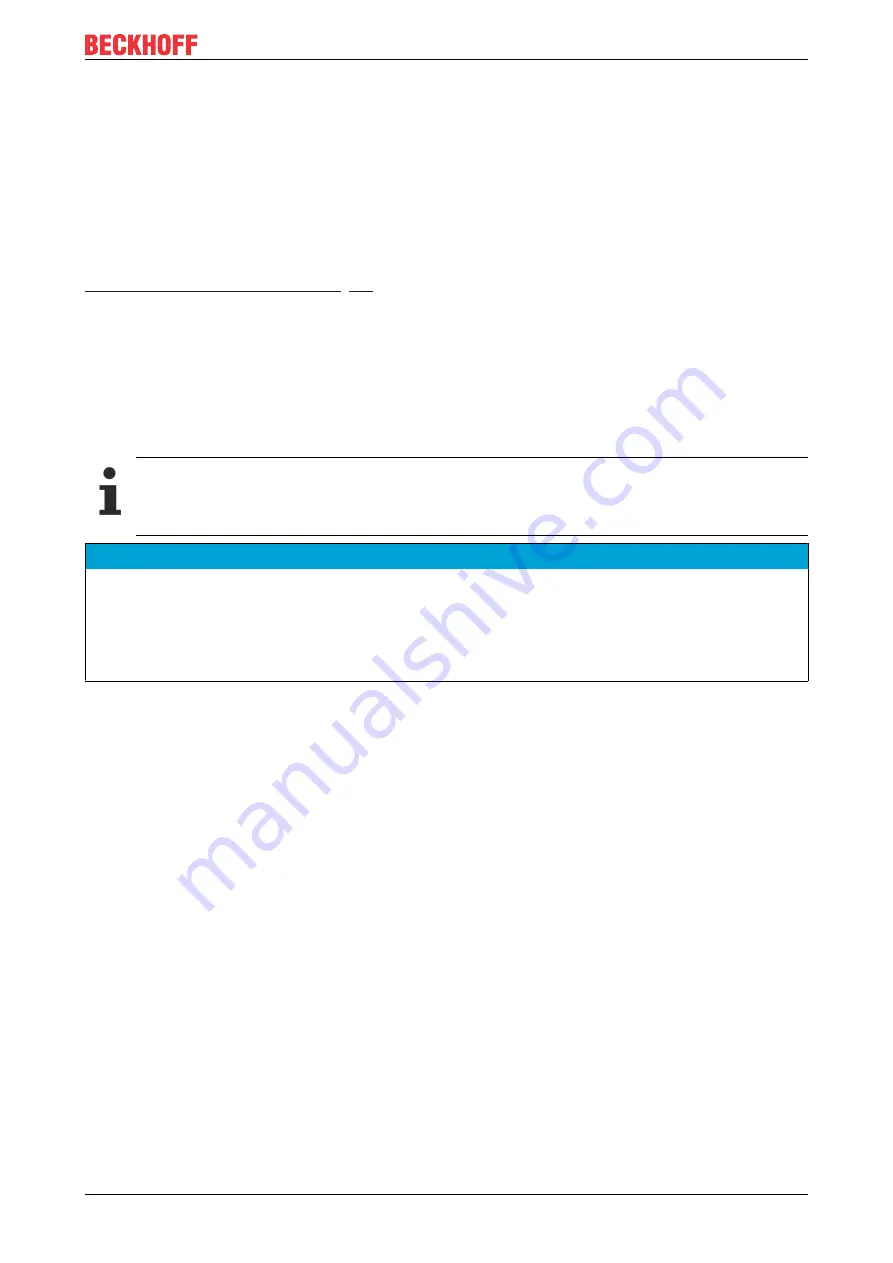
Calculating the synchronisation phase
TS5055
23
Version: 1.3
7
Calculating the synchronisation phase
An attempt is made when calculating the synchronisation phase to find an optimum solution while observing
the boundary conditions specified by the user. If it is not possible to observe the specified boundary
conditions, the coupling is declined and an appropriate error message is issued.
Optimizations
As can be seen in the flow chart below, the individual bit masks partly influence the internal optimization
steps of the profile calculation, since an optimum is searched for depending on predefined rules (see
Parameterizable boundary conditions [
). Essentially, a 5th order polynomial or a combination of a 5th
order polynomial with a 1st order polynomial is used. A 5th order polynomial is generally not free from
overshoot, but the accelerations are more moderate than when combining a 5th order polynomial with a 1st
order polynomial. The combination of the 1st and 5th order polynomials is calculated in such a way that it is
always free from overshoot. However, higher accelerations and decelerations occur with it. If, for example,
the actual velocity matches the synchronous velocity, but a certain position difference must be compensated.
Then the optimum velocity is calculated internally as a function of the maximum acceleration. Result is a 5th
power polynomial a 1st order polynomial with the calculated velocity and a 5th power polynomial. At least
one of the two 5th power polynomials exploits the maximum acceleration. To avoid extreme jerk values, the
jerk check should be switched on.
The optimizations shown can only be carried out if both the master and slave axes are free of accel-
eration at the time of coupling. For accelerated axes, a 5th order polynomial is used for synchro-
nization, which is checked for compliance with the specified boundary conditions, but cannot be op-
timized.
NOTE
If the master axis is an encoder axis (an "external encoder system"), something which as a rule is never
mathematically free from acceleration, particular care must be taken to filter the actual acceleration. Alter-
natively the determination of the actual acceleration can be deselected in the encoder, i.e. set to zero. The
NC also has an internal algorithm for this combination (master encoder axis with the Universal Flying Saw
as a slave). This algorithm sets master accelerations whose magnitudes are less than (2.0 • scaling factor /
cycle time
2
) to zero at the coupling time.
Optimisation step 1:
Aim: "Velocity profile free from undershoot or overshoot"
An attempt is first made to calculate a profile that synchronises the velocity without overshoot or undershoot
(a combination of a first order polynomial and a 5th order polynomial or vice versa: in abbreviated form,
polypolynomial5 or polypolynomial1). If the acceleration check is active at this stage, and
if one or more of these limit values (acc, dec) is exceeded, then another profile, which in general is not free
from overshoot (polynomial5) is calculated. If one of the active limit values (acc, dec) is still exceeded with
his profile, then the synchronisation command is finally declined with an error code.
Optimisation step 2:
Aim: "Limitation to maximum permitted velocity"
If the first optimization step is not possible, the second optimization step checks whether the maximum
permitted velocity for the slave axis is exceeded by a general standard profile (polynomial5). If this is the
case, an attempt is made to generate a profile in which the maximum profile velocity is precisely the
maximum velocity permitted to the slave axis (machine data) (polypolypolynomial5). It
should be noted that this optimization attempt usually results in larger values of acceleration or deceleration.
If the acceleration check is active at this stage, and if one or more of these limit values is exceeded, then this
second optimization step is rejected, and finally a profile, which is not in general free from overshoot
(polynomial5), is calculated. If one of the active limit values (acc, dec) is still exceeded with his profile, then
the synchronization command is finally declined with an error code.
Содержание TS5055
Страница 1: ...Manual EN TS5055 TwinCAT 2 NC Flying Saw 2022 11 22 Version 1 3...
Страница 2: ......
Страница 4: ...Table of contents TS5055 4 Version 1 3...
Страница 31: ...Interfaces TS5055 31 Version 1 3 ADS interface Documentation of the ADS interface...
Страница 43: ...PLC API TS5055 43 Version 1 3 Type definition for the characteristic parameters of a flying saw synchronization...
Страница 46: ......