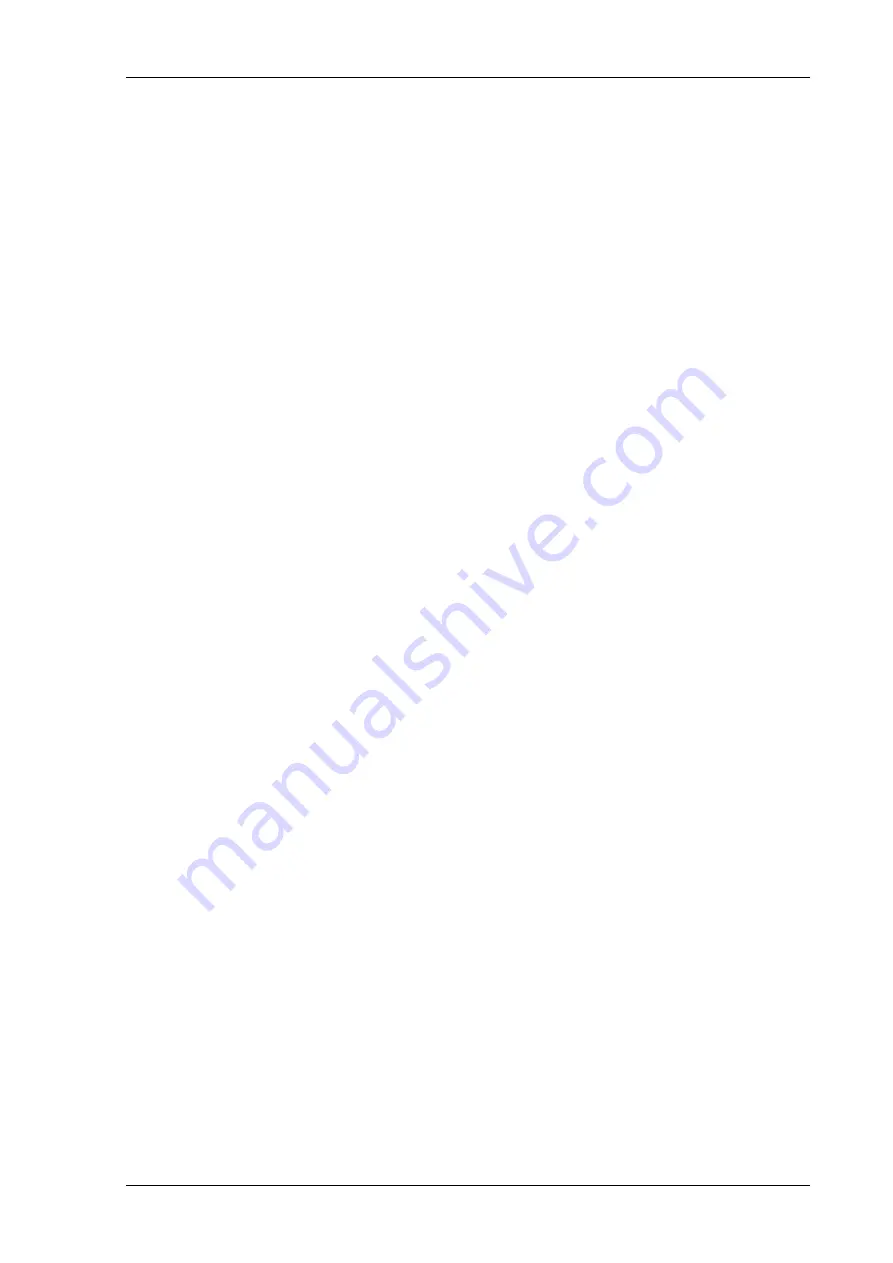
C1120 S5 to II/O Lightbus Interface
Beckhoff II/O-Lightbus System
Date 27.06.97
Version 2.1
Page 15 of 52
Modules can be set up in the configuration list as:
-
direct module or
-
indirect module,
depending on the necessity of access in every PLC cycle. This is supplied to enlarge the
address space of the PLC above 128 bytes process image.
Direct modules
Direct modules are mapped directly to the PLC process image. The PLC process image
addresses are edited in the I/O byte addresses D0 to D3 of every telegram frame belonging to
the module - each line in the setup screen belongs to a dedicated II/O-Lightbus telegram frame
to the addressed module. The address names (e.g. O 10) of the PLC programm are used for
reference.
Example given: the modules 1 and 2 are mapped as direct modules. The STEP5 program
accesses the I/O addresses 23 to 26, the C1120 maps the I/O data to the modules 1 and 2:
IB 23, IB 24
from module 1
OB 23, OB 24, OB 25, OB 26
to module 2
The inputs and outputs can be addressed bit-, byte-, or wordwise:
I 23.0 ... I 23.7, oder IW 23 = IB 23 & IB 24
are handled as usual.
All direct mapped modules are refreshed synchronously and cyclic with the PLC cycle and
process image refresh. The direct mapped modules can be accessed directly from the PLC
program at any time.
The modules 7 and 8 are also direct modules. However, they are assigned to the fast
communications channel by means of their identification codes “ SA” and “ SE” respectively.
If intelligent modules are to be addressed during the PLC cycle (e.g. terminal bus coupler) the
first two data bytes (D0, D1) can be assigned constants. Those constants are entered with the
identification codes “ M” (for memory) and “ C” (for constant).
In the example, D0 on module 5 is assigned the fixed value 1 (“ M” ) and D1 the fixed value
128 (“ C” ).