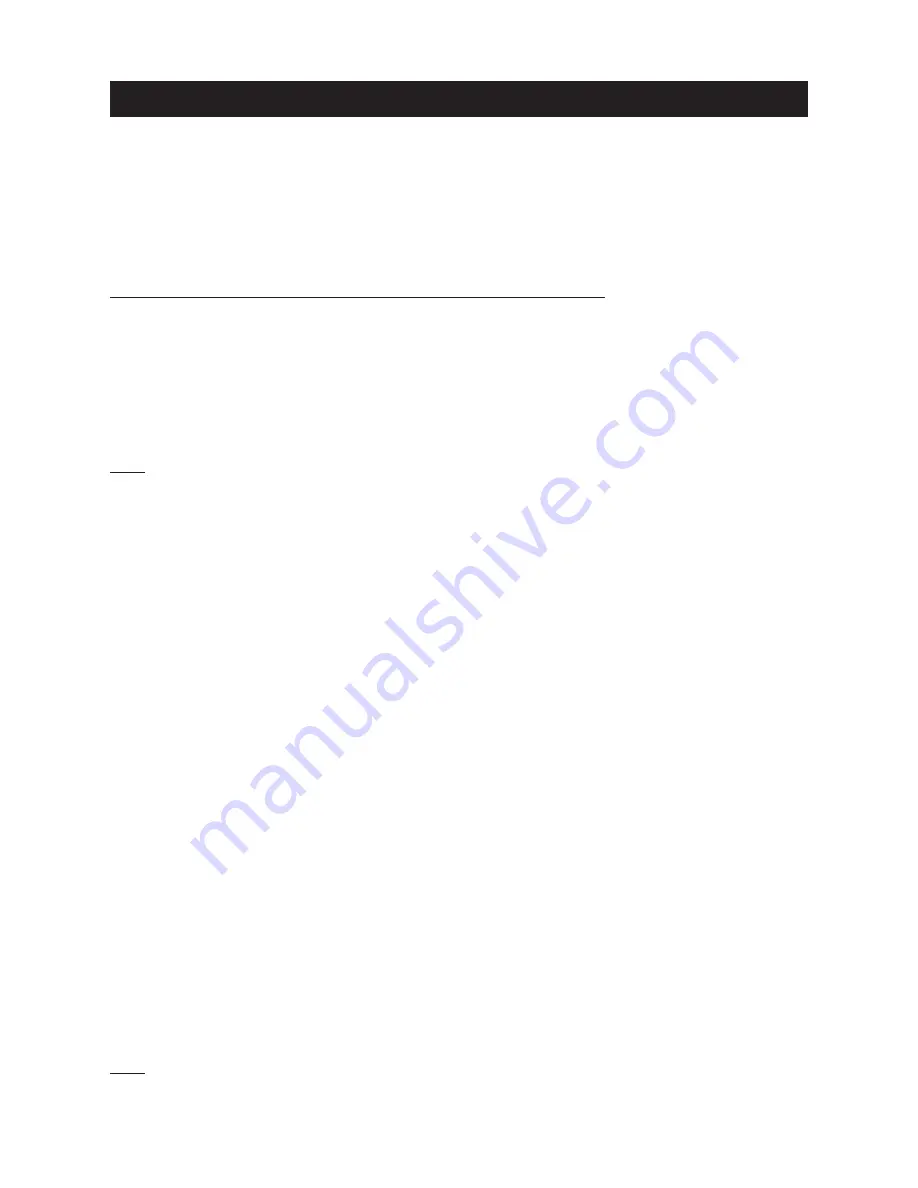
5
Important information for system operators
1.3
Start-up and maintenance
Have Windhager Customer Service or one of our customer service PARTNERS put your new boiler into servi-
ce. In this way, all functions of the new unit will be thoroughly checked; you will also benefit from the detailed
information provided by the system installer. Installation by a qualified technician as well as the maintenance
required by the guarantee limitations will guarantee the optimal use and service life of your boiler system. This
is the only way to assure the benefits of this technologically advanced boiler and guarantee safe, environmentally
friendly and energy-saving system operation.
The following preconditions must be met before you order the initial start-up:
1.) Boiler installed correctly.
2.) System fully wired up electrically.
3.) System rinsed, filled and vented – heat consumption must be possible.
4.) Hot water tank connected to domestic water and filled.
5.) Sufficient quantity of fuel available (pellets, split logs, oil or gas).
6.) The customer must be present during start-up.
The initial start-up cannot be carried out if any of these points are neglected. The customer will be charged for
any unnecessary costs arising as a result. Start-up and maintenance are part of the guarantee requirements as
listed in the enclosed „guarantee limitations“.
Note:
During the first few weeks after start-up, condensation can occur in the combustion chamber, on the hea-
ting surfaces and in the ash pan. This has no effect on the function and service life of the boiler.
1.4
Checking the heating water
The chemical composition of the heating water must meet the specifications of ÖNORM H 5195 Part 1 or VDI
2035 T1. According to ÖNORM M 5195 Part 1, the condition of the heating water must be checked every 2 years
by a heating technician in order to avoid corrosion and sediment accumulation in the heating system.
The check must be performed once every year in heating systems with more than 1500 litres of heating water.
In the event of repair work requiring a change of water in the heating system, the heating water is to be checked
within 4 to 6 weeks after such work. Corrosion and sediment resulting from improper heating water are not
covered by the guarantee and warranty.
1.5
Operating noises
The FireWIN is a modern, fully automated pellet central heating boiler for living areas with a high level of conve-
nience in terms of operation and cleaning. This automation means that operating noises may occur during normal
operation.
Normal operating noises are:
Flame noises – Natural flame noise can be heard depending on the size of the flames.
Light scratching and scraping noises – Depending on the level of contamination, cleaning noises may occur
during automated cleaning or shake-out. If these become louder over time
⇒
Clean the pellet central heating
boiler for living areas, especially the burner pot.
Trickling of pellets and vacuum cleaner noise – Fully automated pellet supply involves pellets being sucked from
the storage room into the reserve supply container. During filling, the suction turbine generates a „vacuum cle-
aner noise“ in the storage room and the feed hose, and the trickling of the pellets can be heard in the reserve
supply container.
Clicking noises – The relays switch on or off when the control unit is installed.
Liquid noise, gurgling – This is caused by air in the heating water
⇒
Bleed the system.
Air induction noises – Air induction noise occurs at the air supply induction point for combustion (air opening
in the device)
⇒
Use air supply pipes to relocate the induction point outside the house or into an adjacent room.
Note:
Due to these operating and flame noises, we do not recommend installing the device in bedrooms or
quiet rooms – see also the information in the FireWIN installation instructions, „Installation“.