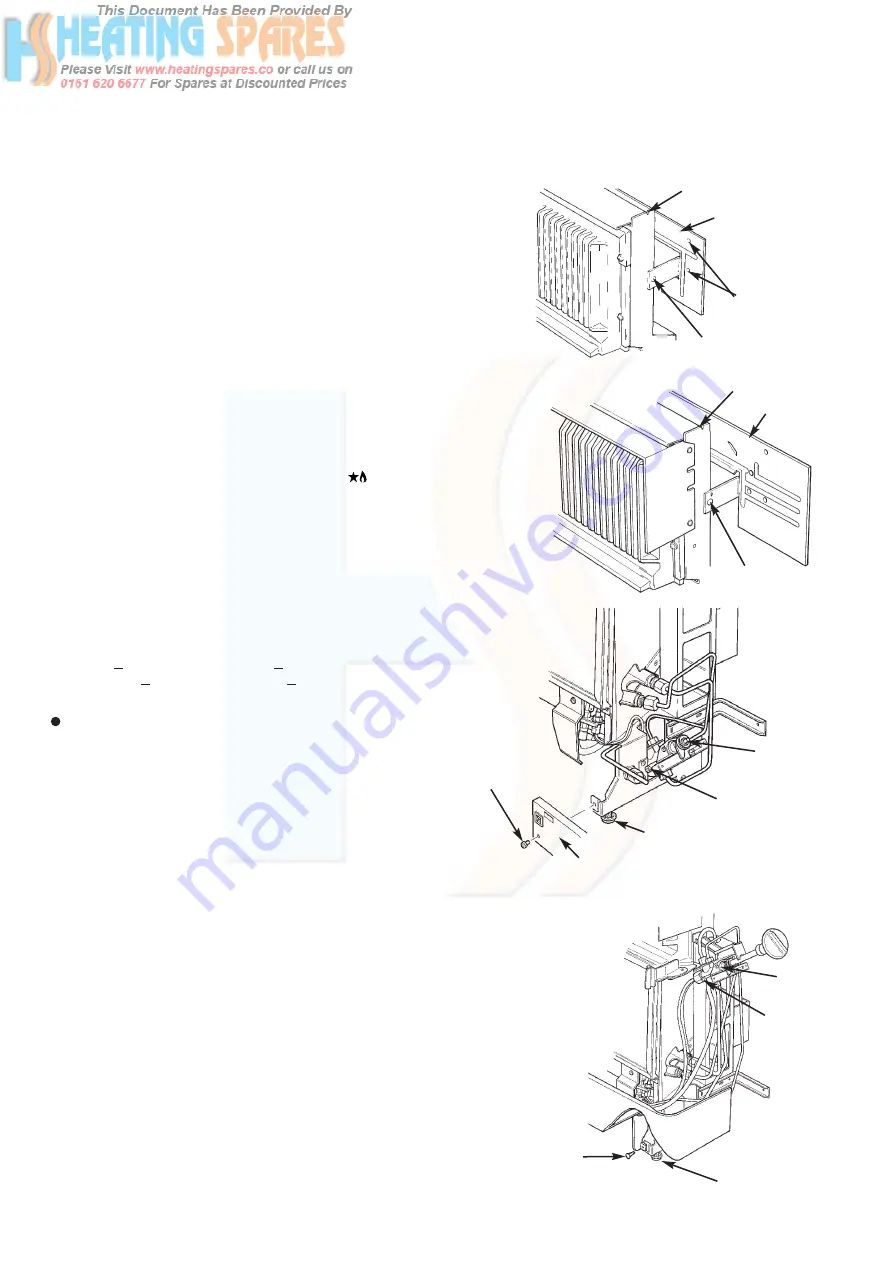
Supplied By www.heating spares.co Tel. 0161 620 6677
page 6
Commissioning the Fire
1. Remove the polystyrene fitting securing the coal bed
(Fig.11) as follows:
(a)
Disengage the front panel retaining clamps and
remove the glass front panel.
(b)
Remove the polystyrene fitting securing the coal
bed.
(c)
Carefully remove the coal bed from its plastic
bag.
CAUTION: The coal bed is extremely fragile and must
be handled accordingly. Gloves should be worn and
any inhalation of the dust should be avoided. Keep
the coals away from children at all times. Please read
the Important Information Section on page 3.
(d)
Replace the coal bed and glass front panel.
2. Remove the pressure test point sealing screw and
connect a pressure gauge (Fig.6).
3. Turn on the gas service tap (at present supplying gas
to the boiler only) fully anti-clockwise. The service tap is
now supplying both the boiler and the fire (Fig.4).
4. Purge according to in GB BS 6891 and in IE the
current edition of I.S. 813
“
Domestic Gas Installations
”
.
5. To light the fire pilot - fit the fire control knob, and
ensure that it is fully clockwise. Push in and turn anti-
clockwise past the positive stop at the pilot ( ) position
to operate the igniter. Repeat until the pilot lights.
Continue to hold in the control knob for a further 15
seconds. Release slowly and the pilot should stay alight. If
the pilot does not stay alight turn the control knob to the
OFF position fully clockwise and repeat.
6. Check that the fire burner lights smoothly by pushing in
the knob and turning fully anti-clockwise. Test for gas
soundness with leak detection fluid.
7. Check the fire pressure with the control knob in
position 4 fully anti-clockwise.The pressure should be
13.8mbar + 0.5mbar (5.5 in. wg. + 0.2 in. wg.) for LFE5
and 14.5mbar + 0.5mbar (5.8 in. wg. + 0.2 in. wg.) for GF3.
8. Turn the control knob clockwise to the OFF position
( ). Remove the pressure gauge and refit the pressure
test point sealing screw, ensuring a gas tight seal.
9. Test for clearance of flue products as follows:
(a) Ensure that all doors and windows are closed.
IMPORTANT NOTE: If there is an extractor or
ceiling fan in the room or adjoining room then
the spillage test must be performed with the
fan turned on and any interconnecting doors
between the fan and the appliance left open.
(b) Turn on the fire (position 4 fully anti-clockwise).
(c) After 5 minutes take a smoke match and insert it
into the boiler draught diverter in the position
shown (Fig.8). If the majority of the smoke is not
drawn into the chimney spillage is indicated and
the fire must be operated for a further 10 minutes
before rechecking. If spillage is still evident the
cause must be ascertained and rectified before
continuing with commissioning.
(d) Repeat with both fire and boiler alight, having run
the boiler for 5 minutes.
10.Fit the case as follows:
(a) Remove the control knob.
(b) Lift the outercase over the heat exchanger and
locate the two 'vee' notches in the top of the case
into the 'vee' notches at the top of the inner case
(Fig.5).
(c) Secure the outercase to the inner case using the
two securing screws provided (Fig.6).
11.Plug in the electrical supply to the case and fit the
controls cover panel and control knob (Fig.13).
12.Check the operation of the light effect by operating the
switch adjacent to the control tap (Fig.9).
13.Hand the user the User
’
s Instructions, explain the
operation of the boiler and fire and leave the unit set to
suit their requirements.
14.Leave these instructions with the user or adjacent to
the gas meter.
Fig. 6 Commissioning the Fire
Location "Vee" Notches
Backing Plate
Alternative Fixing
Hole Position
Backing Plate Securing
Screws (2 off)
Fig. 5 Backing Plate
Fig. 5 Backing Plate
Fig. 6 Commissioning the Fire
GF3 Super
LFE5 Super
Location "Vee" Notches
Backing Plate
Backing Plate Securing
Screws (2 off)
GF3 Super
LFE5 Super
Fire Control
Tap
Pressure Test Point
Sealing Screw
Adjusting Feet
(2 off)
Outer Case
Outer Case
Securing Screws
(2 off)
Fire Control
Tap
Pressure Test
Point Sealing
Screw
Adjusting Feet
(2 off)
Outer Case
Securing Screws
(2 off)