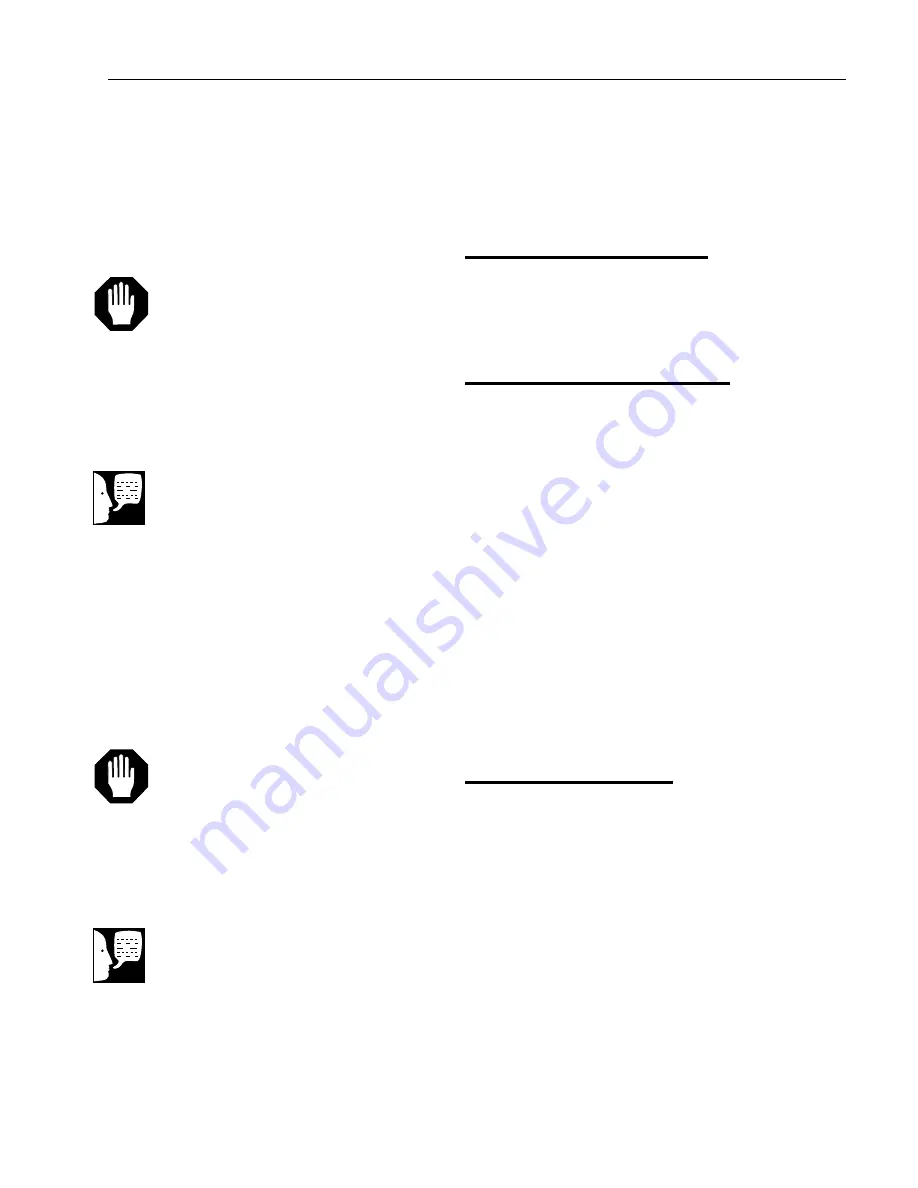
23
CAUTION
Minimize operation of furnace under 800°C.
Element life is reduced when operating below
800°C because the protective layer of silica
glass takes longer to form.
NOTE
Temperature setpoint or output power is
indicated on lower display, single depression
of scroll button will alternate between these
two parameters. The control will cause the
furnace chamber to heat to the chosen
temperature and hold it at this temperature
until you turn off the front circuit breaker
switch or select another temperature.
CAUTION
Remember that whenever the power switch
is turned “ON”, the furnace will begin to
heat to the setpoint temperature that was
previously programmed. This value will
remain unchanged for up to a year without
electricity being applied to the control.
NOTE
The two center push buttons are non-func-
tional.
Operating the Controller
The programmable control can be used as a single
setpoint control or as a programmable control.
Single Set Point Operation
To use as a single set point control simply push up or
down
buttons to choose a setpoint temperature.
To operate the control as a single set point control:
1. Turn front circuit breaker switch to the “ON” position.
The setpoint temperature presently set in the control
will appear on the lower display.
2. To change this set point, depress the “UP” or
“DOWN” push button until the desired setpoint value is
displayed,
then release the button.
3. At this point, the furnace will begin to heat if the new
set point temperature you have chosen is higher than
the
present chamber temperature.
4. The upper display indicates actual chamber tempera-
ture.
Programming Controller
To run a program, first determine your ramp rate, dwell
times, program levels. It is helpful to graph your program
for ease of loading program into controller. Observe
maximum ramp rates (heat up time) on the general
specifications page before programming ramp rates.
A maximum of 8 ramp and 8 dwell segment combinations
are available, thus enabling eight different setpoint levels
to be achieved. Each ramp is programmed by specifying
the program level (PL) and the required ramp rate (PR).
The control automatically calculates the time that is
required to attain the program level (PL) based on
O
PERATION
OF
P
ROGRAMMABLE
M
ODELS
Содержание F46110CM
Страница 37: ...37 Figure 1A Element Replacement...