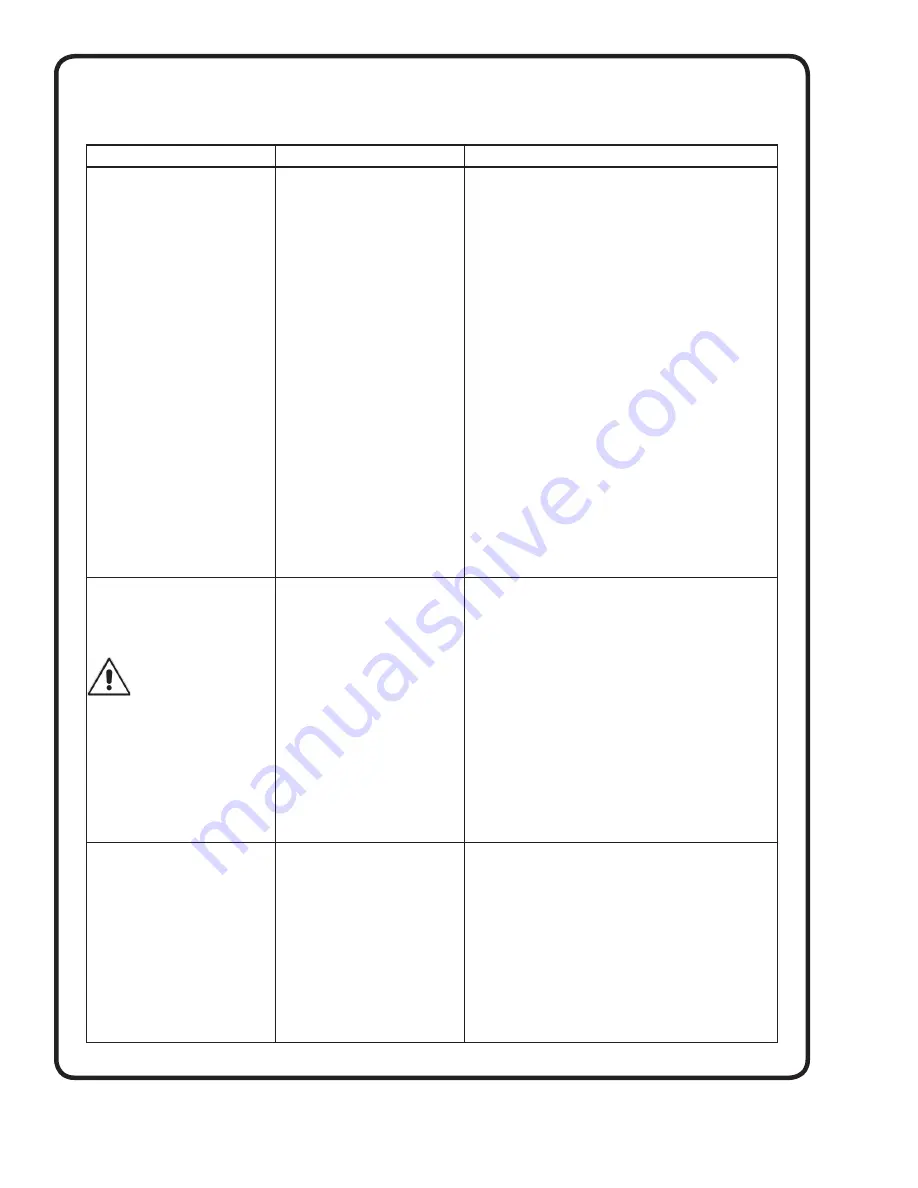
14
Symptom
Possible Cause (s)
Corrective Action
Pump delivers insuffi cient
capacity
1. Incorrect voltage
2. Excessive infl ow or pump
not properly sized for ap-
plication
3. Discharge restricted
4. Check valve stuck closed
or installed backwards
5. Shut-off valve closed
6. Impeller jammed or loose
on shaft, worn or dam-
aged, impeller cavity or
inlet plugged
7. Pump may be airlocked
8. Pump running backwards
1. Check all electrical connections for security.
Have electrician measure current in motor
leads. If current is within ±20% of locked rotor
Amps, impeller is probably locked. If current is
0, overload may be tripped. Remove power,
allow pump to cool, then recheck current
2. Recheck all sizing calculations to determine
proper pump size
3. Check discharge line for restrictions, including
ice. If line passes through or into cold areas
4. Remove and examine check valve for proper
installation and freedom of operation
5. Open valve
6. Check impeller for freedom of operation, se-
curity, and condition. Clean impeller cavity and
inlet of any obstruction
7. Loosen union slightly to allow trapped air to
escape. Verify that turn-off level of switch is set
so that impeller cavity is always fl ooded. Clean
vent hole
8. Check rotation. If power supply is three phase,
reverse any two of three power supply leads to
ensure proper impeller rotation
Pump shuts off and turns on
independent of switch (trips
thermal overload protector)
Pump may start
unexpectedly.
Disconnect power
supply
NOTE: Some pumps do not
have thermal load protec-tion
on the motor Check pump
specifi cations to determine
1. Incorrect voltage
2. Excessive infl ow or pump
not properly sized for ap-
plication
3. Impeller jammed, loose on
shaft, worn or damaged;
impeller cavity or inlet
plugged
4. Excessive water tempera-
ture (internal protection
only)
1. Check all electrical connections for security.
Have electrician measure current in motor
leads. If current is within ±20% of locked rotor
Amps, impeller is probably locked. If current is
0, overload may be tripped. Remove power,
allow pump to cool, then recheck current
2. Recheck all sizing calculations to determine
proper pump size
3. Check impeller for freedom of operation, se-
curity, and condition. Clean impeller cavity and
inlet of any obstruction
4. Check pump temperature limits & fl uid tem-
perature
Pump operates noisily or
vibrates excessively
1. Worn bearings, motor
shaft bent
2. Debris in impeller cavity or
broken impeller
3. Pump running backwards
4. Piping attachments to
building structure too rigid
or too loose
1. Check winding insulation (Megger Test) and
winding resistance. If check is outside of range,
dry and recheck. If still defective, replace per
service instructions
2. Check impeller for freedom of operation, se-
curity, and condition. Clean impeller cavity and
inlet of any obstruction
3. Check rotation. If power supply is three phase,
reverse any two of three power supply leads to
ensure proper impeller rotation
4. Replace portion of discharge pipe with fl exible
connector
Troubleshooting Chart
(Continued)