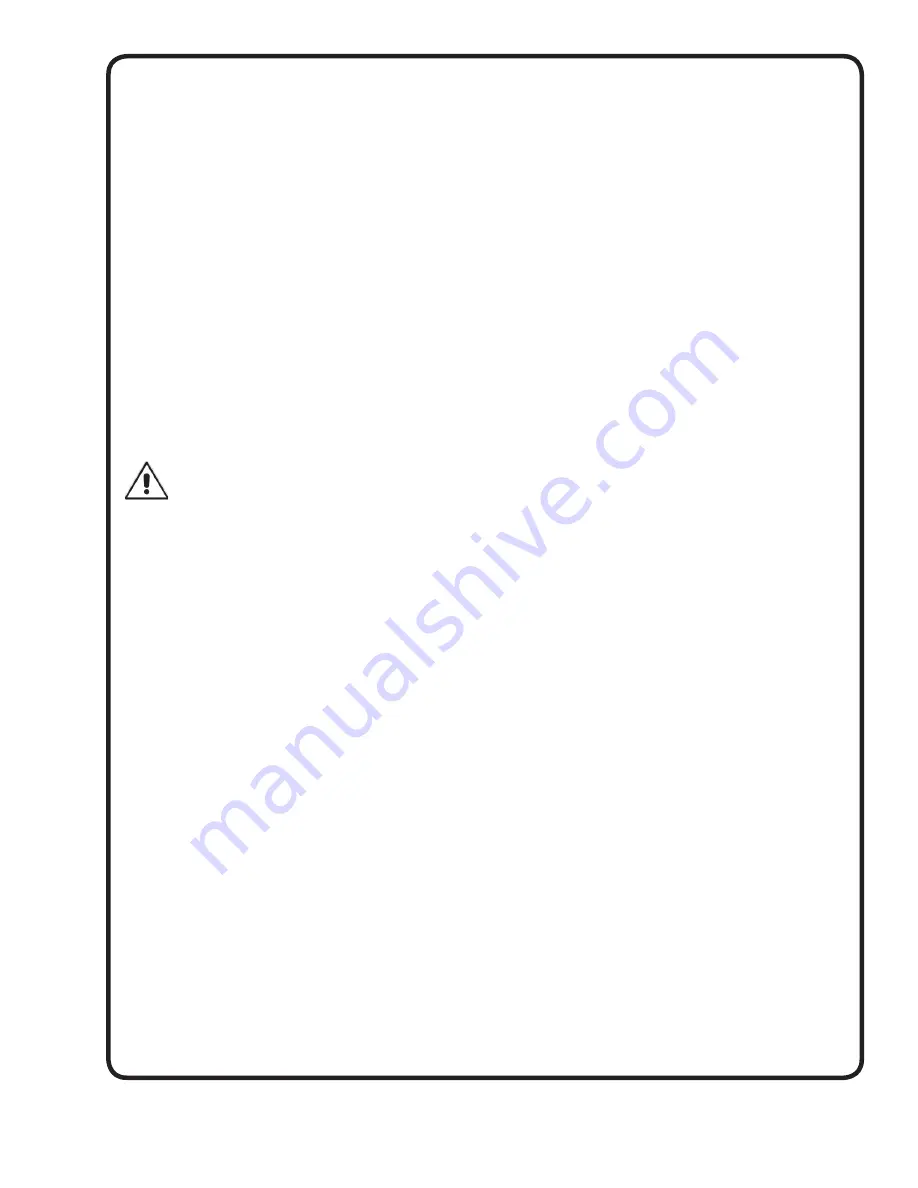
5
It will then automatically reset and restart the pump after
the motor cools to a safe temperature. In the event of an
overload, the source of this condition should be deter-
mined and rectifi ed immediately.
DO NOT LET THE
PUMP CYCLE OR RUN IF AN OVERLOAD CONDITION
OCCURS!
SECTION D - START UP OPERATION
D-1) Check Pump Rotation:
Before putting pump into service for the fi rst time, the
motor rotation must be checked. This is especially true
on 240 volt pumps after installing the appropriate cable
plug. Improper motor rotation can result in poor pump
performance and can damage the motor and/or pump. To
check the rotation, suspend the pump freely, momentarily
apply power and observe the “kick”. “Kick” should always
be in a counterclockwise direction as viewed from the top
of the pump motor housing. Pump “kick” is the opposite
direction of pump rotation.
D-2) Start Up:
DO NOT attempt to start a frozen pump.
Instead, submerge pump in water for twenty
minutes before starting. DO NOT attempt to
thaw a frozen pump with a torch
.
D-3) Warranty Registration:
Fill in the Warranty Registration at the end of this manual
and send it in to our Warranty / Service Department. Also,
record the model number and date code numbers in
Section F-1 of this manual for future reference if needed.
SECTION E - PREVENTATIVE MAINTENANCE
The following procedure must be followed to assure
proper pump operation.
E-1) General Safety:
Frequent inspections shall be made. All electrical parts,
including the portable cable and wiring shall be kept in
a safe condition.
KEEP CABLE GLAND NUT TIGHT.
CHECK FREQUENTLY.
There shall be no openings in the
casing of the electrical parts. The operating voltage shall
match the voltage rating of the motor.
E-2) Servicing:
Pump shall be restored to the state of original safety with
respect to all lead entrances, etc. following disassembly.
E-3) Renewals and Repairs:
Special care shall be taken in making renewals and re-
pairs. Leave no parts off. Use replacement parts furnished
by the manufacturer. When any lead entrance is disturbed,
the original leads or exact duplicates thereof shall be
used.
E-4) Fasteners:
All bolts, nuts, screws and other means of fastenings shall
be in place, properly tightened and secured.
E-5) Cable Requirements:
Special care shall be taken in handling the cable (7)
against mechanical injury and wear. Connections and
wiring to the power source shall be in accordance with all
electrical and safety codes.
E-6) Shaft Seals:
The seals (12 & 16) should be inspected every 400 or
500 operating hours for wear (more often if abrasives are
present). To make a quick check of the seal’s condition,
drain and inspect the oil in the seal chamber (see Section
F1.1). If oil removed from the pump contains water or
abrasives, replace the seals.
SECTION F - SERVICE AND REPAIR
F-1) Lubrication:
F-1.1) Checking Oil -
To check the seal chamber oil,
invert the pump and remove the screws (26) lockwashers
(11) strainer (25), suction case (24), impeller nut (15),
washers (14 & 22) and Impeller (21). Remove the socket
head screw (9) with o-ring (8) from the hole marked “OIL”.
With a fl ashlight, visually inspect the oil in the seal cavity
to make sure it is clean and clear, light amber in color and
free from suspended particles. Milky white oil indicates
the presence of water. If the oil looks milky white, pour
the oil out of the oil chamber and let it settle in a clean
dry container. If any water settles out in the bottom of
the container or if the oil is white and thick (emulsifi ed),
replace the mechanical seals and oil.
You can also check oil for contamination by using an oil
tester with a range to 30 Kilovolts breakdown. If oil is
found to be clean and uncontaminated (measure at or
above 15KV. Breakdown), refi ll the seal cavity. If the oil
is found to be dirty, or contaminated (or measures below
15KV. Breakdown), replace the mechanical seals and oil.
F-1.2) Replacing Oil:
Follow steps in E-2.1 to remove socket head screw (9)
with o-ring (8) from the hole marked “OIL”. Turn pump
over to drain oil from seal chamber. Dispose oil properly.
Flush inside seal chamber of diffuser thoroughly to be
sure it is clean and free of abrasives. Refi ll seal chamber
with 3 oz. (90 ml) of an approved oil. The oil shall be of a
highly refi ned paraffi nic base, straight mineral oil, free of
all additives (called non-inhibited or non-detergent). Refer
to Table 1 for recommendations.
Содержание 70 Series
Страница 8: ...8 Figure 2...
Страница 12: ...Notes...