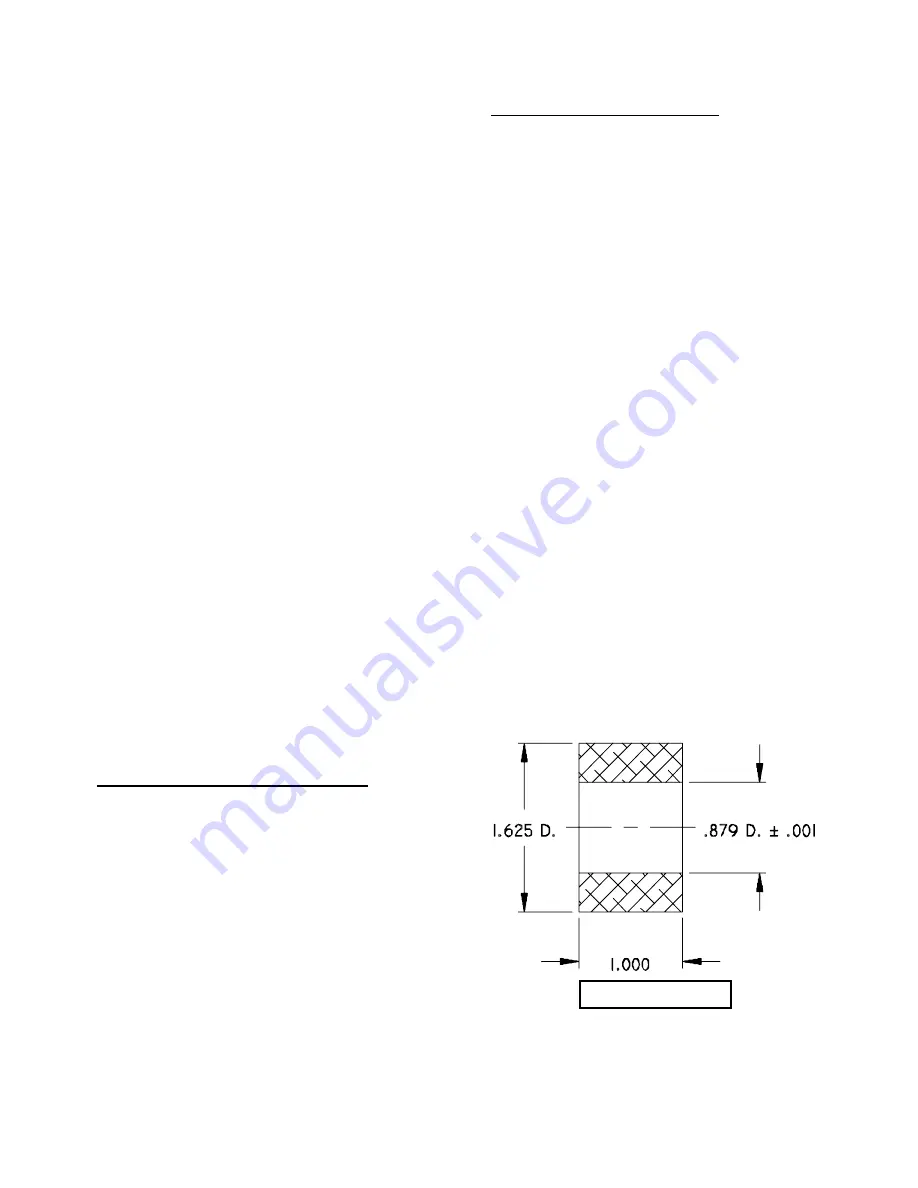
Lowest noise level indicates correct rotation.
4.) Another method that can be used if unit is installed in
tank is to close discharge line. With adequate water to
place pump under load, start pump and check
amperage draw on all three lines. Stop pump, reverse
two leads (red, white, or black). Restart and recheck
amperage draw on the three lines. Lowest average
amperage occurs when pump is running correct
rotation. Note the noise level when unit is pumping.
Lowest noise level indicates correct rotation.
D-3) Start-Up Report:
Included at the end of this manual are two start-up report
sheets, these sheets are to be completed as applicable. Return
one copy to Barnes Pumps, Inc. and store the second in the
control panel or with the pump manual if no control panel is
used. It is important to record this data at initial start-up since
it will be useful to refer to should servicing the pump be required
in the future.
D-3.1) Identification Plate:
Record the numbers from the pump’s identification plate on
both START-UP REPORTS provided at the end of the manual
for future reference.
D-3.2) Insulation Test:
Before the pump is put into service, an insulation (megger) test
should be performed on the motor. The resistance values
(ohms) as well as the voltage (volts) and current (amps) should
be recorded on the start-up report.
D-3.3) Pump-Down Test:
After the pump has been properly wired and lowered into the
basin, sump or lift station, it is advisable to check the system
by filling with liquid and allowing the pump to operate through
its pumping cycle. The time needed to empty the system, or
pump-down time along with the volume of water, should be
recorded on the start-up report.
SECTION E: PREVENTIVE MAINTENANCE
The sealed motor is oil filled and is lubricated for life, no internal
lubrication or other maintenance is required, if there is evidence
of internal problems, the unit should be taken to an authorized
service station.
However as with any mechanical piece of equipment a
preventive maintenance program is recommended and
suggested to include the following checks:
1) Inspect impeller and body for excessive build-up or
clogging and repair as required per section F-5.
2) Inspect seal for wear or leakage and repair as
required per section F-6.
SECTION F: SERVICE AND REPAIR
NOTE:
All item numbers in ( ) refer to Figures 19 & 20 for EL
Models and 21 & 22 for EDS Models.
F-1) Checking Oil:
To check oil or before removing seal or disassembling motor
section drain the oil by removing either pipe plug (11) in switch
end bell (42) or drive end bell (46). Catch oil in a clean
container. Check the oil for water or other contaminants, a milky
appearance indicates water has emulsified with the oil.
F-2) Testing Oil:
1.
Check oil for water contamination using an oil tester
with a range to 30 Kilovolts breakdown.
2.
If oil is found to be clean and uncontaminated (measure
above 15 KV. breakdown), refill the motor housing
as per section F-4.
3.
If oil is found to be dirty or water contaminated
(or measures below 15 KV. breakdown), the the pump
must be carefully inspected for leaks before refilling with
oil. To locate the leak, perform a test as per section F-3.
After leak is repaired, refill with new oil as per
section F-4.
F-3.1) Leak Checking - Single Seal:
When leak checking units, seal retainer (see Figure 2) should
be used in place of impeller and top cover (20) must be
removed. Push motor diaphragm (40) down into cavity. Place
a plug with no burrs or sharp edges (see Figure 4) in recess
formed by diaphragm. Hold diaphragm plug in place with
diaphragm clamp (see Figure 5) fastened to switch end bell.
Remove pipe plug (11) from either switch end bell (42) or drive
end bell (46). Apply 8 to 10 PSI air pressure to inside of motor
housing. Submerge motor, any bubbling indicates leakage. In
any case where leakage occurs, changes must be made to
correct the problem. After removing motor from water, drain
and dry all water from top section of switch end bell (42).
Fig. 2 - Single Seal
9
Содержание 4SE-EDS Series
Страница 15: ...Fig 15 SINGLE PHASE 1 5HP 2 2HP Fig 16 SINGLE PHASE 2 7HP 4 5HP Fig 17 THREE PHASE 15...
Страница 18: ...Fig 19 SERIES 4SE EL 18...
Страница 19: ...Fig 20 SERIES 4SE EL 19...
Страница 22: ...SERIES 4SE EDS Fig 21 22...
Страница 23: ...SERIES 4SE EDS Fig 22 23...
Страница 27: ...SERIES 4SE EDS Fig 23 27...