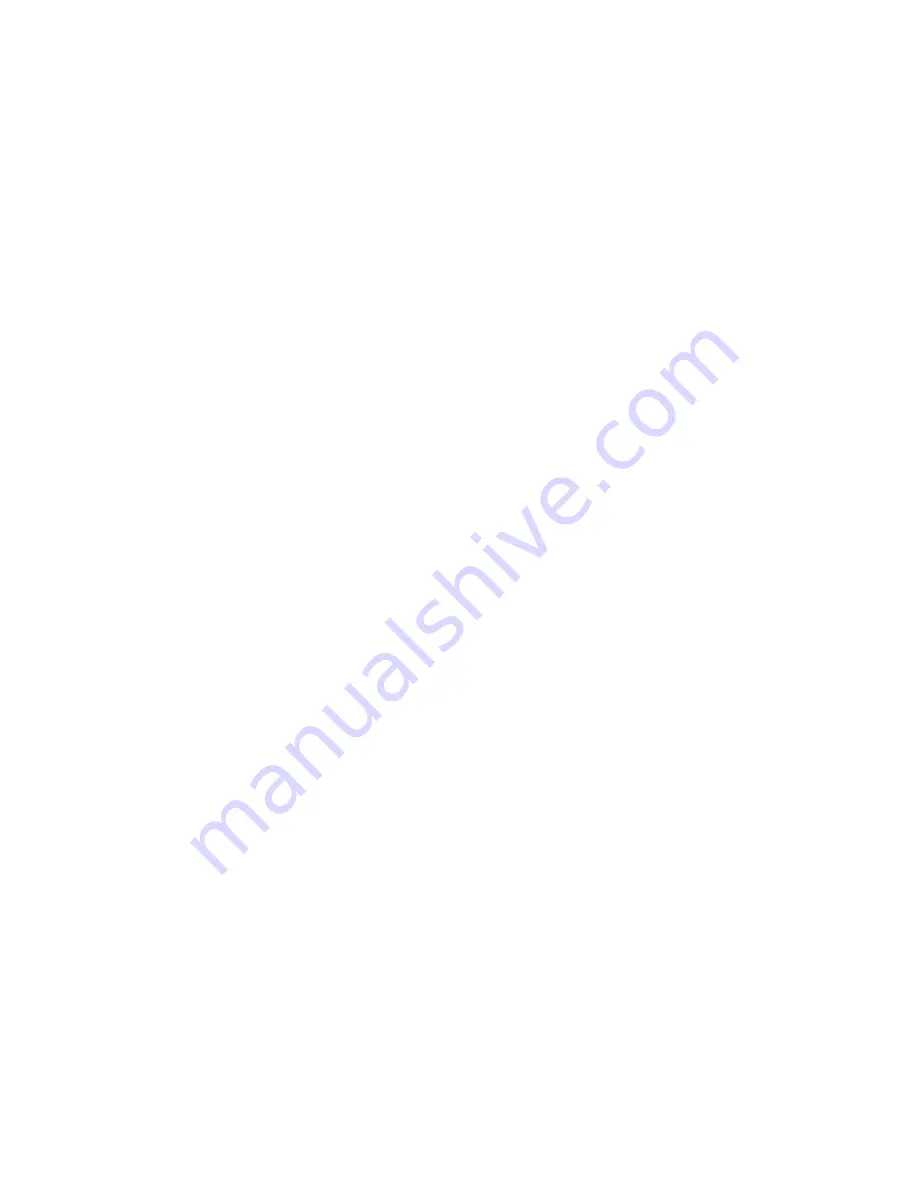
6
SECTION B: GENERAL INFORMATION
B-1) To the Purchaser:
Congratulations! You are the owner of one of the fi nest
pumps on the market today. Barnes® Pumps are products
engineered and manufactured of high quality components.
Over one hundred years of pump building experience
along with a continuing quality assurance program combine
to produce a pump which will stand up to the toughest
applications.
This Barnes pumps manual will provide helpful information
concerning installation, maintenance, and proper service
guidelines.
B-2) Receiving
Upon receiving the pump, it should be inspected for
damage or shortages. If damage has occurred, fi le a claim
immediately with the company that delivered the pump. If
the manual is removed from the packaging, do not lose or
misplace.
B-3) Storage:
Short Term -
Barnes pumps are manufactured for effi cient
performance following long inoperative periods in storage.
For best results, pumps can be retained in storage, as factory
assembled, in a dry atmosphere with constant temperatures
for up to six (6) months.
Long Term -
Any length of time exceeding six (6) months, but
not more than twenty four (24) months. The units should be
stored in a temperature controlled area, a roofed over walled
enclosure that provides protection from the elements (rain,
snow, wind blown dust, etc..), and whose temperature can be
maintained b40 deg. F and +120 deg. F.
If extended high humidity is expected to be a problem, all
exposed parts should be inspected before storage and all
surfaces that have the paint scratched, damaged, or worn
should be recoated with a water base, air dry enamel paint.
All surfaces should then be sprayed with a rust-inhibiting oil.
B-4) SERVICE CENTERS:
For the location of the nearest Barnes Service Center, check
your Barnes representative or Crane Pumps & Systems, Inc.,
Service Department in Piqua, Ohio, telephone (937) 778-8947
or Crane Pumps & Systems Canada Inc., Bramton, Ontario
(905) 457-6223.
SECTION C: PREPARE PUMP FOR OPERATION:
1. See Engine Manufacturer’s instruction manual for
quantity, grade and viscosity of oil and change interval.
Fill engine crankcase with amount needed. and check
oil level frequent. Fill tank per manufacturer,s
recommendations. Be familiar with engine START UP
and SHUT DOWN procedures before operation.
Operate engine in accordance with the manufactures
instructions.
2. Turn down all grease cups on the pump. Keep the cups
full of good clean grease - Exxon Ronex MP or equal.
3. For best performance locate pump as close to water as
possible. Vertical suction lift should not exceed
25 ft. (7.6M) At high lifts, 15 ft. (4.5M) and up, a foot
valve is recommended. When using suction hose, make
sure the gasket in the female fi tting at the pump end is
in place and in good condition.
When using pipe, coat the threads with a thread sealing
compound. Suction hose must be in good condition with
no leaks and lining tight. A loose lining will collapse under
suction and keep liquid from being drawn into pump.
A coarse strainer at end of suction hose is advisable if
there is a possibility of pumping large, hard, unbreakable
solids, such as, rocks, wood, tin cans, etc., that could be
caught between connecting rod and water box, causing
pump
damage.
4. To lead water away, connect non-collapsible suction
hose to the discharge connection. Discharge hose should
not be smaller than suction hose and not kinked.
Discharge head should never exceed 25 ft. (7.6M)
5. On high lifts, or if pump has been idle and valves are dry,
pour water into the discharge opening to help seal valves
and speed up priming.
6. Pump speed can be regulated with throttle control on
engine. from full volume, 65 strokes, to about 40 strokes
for lesser volume and seepage. By regulating pump
speed to suction and discharge conditions, the
intermittent up and down movements of the liquid
columns in the suction and discharge hoses can be
timed so they will assist each other and smooth out the
pump operation, rather than act in opposition. Smoothest
operation can be determined by trying pump at several
speeds.
7. Drain pump in freezing weather by removing drain plugs.
SECTION D: MAINTENANCE INSTRUCTIONS
1. Keep interior of pump and valves clean. When pumping
liquids containing foreign materials, fl ush out pump with
clear water whenever possible.
2. Keep suction hose air tight and check for leaks and loose
lining, as these are major trouble sources when priming.
3. Valves and valve weights must be straight, seat well and
have no cracks.
4. The capacity of a diaphragm pump will vary greatly
depending on the height of the suction lift and length of
discharge line. A discharge line which is too small, long
or high will cause:
A. Excessive bulging of diaphragm on down stroke.
B. Valves closing with loud snap.
C. Rough operation.
D. Engine overloads and slows down.
E. Reduced capacity.
5. Check all bolts frequently and keep them drawn up tightly.
6. TO CHANGE DIAPHRAGM:
A. Rotate the power source (manually) such that the
diaphragm is in the down position.
B. Remove four 5/8” Dia. bolts that hold the clamp ring
and diaphragm to the waterbox. Also remove the two
5/8” nuts that hold the diaphragm to the connecting rod.
C. Manually rotate the drive such that the connecting rod
assembly moves up and off the diaphragm.
D. Remove the diaphragm from the diaphragm bottom
and install a new one onto the studs of the diaphragm
bottom.
E. Install the diaphragm and diaphragm and diaphragm
bottom loosely onto the connecting rod and slowly rotate
the drive such that the connecting rod is in the down
position.
F. Center the diaphragm on the waterbox and bolt the
clamp ring in place and tighten the four bolts on a
crossing
pattern.
Содержание 4CDD6
Страница 8: ...8 Figure 2 Figure 1...
Страница 9: ...9 Figure 3...
Страница 12: ...12 Figure 4...
Страница 15: ...15 Notes...
Страница 16: ...16 Notes...