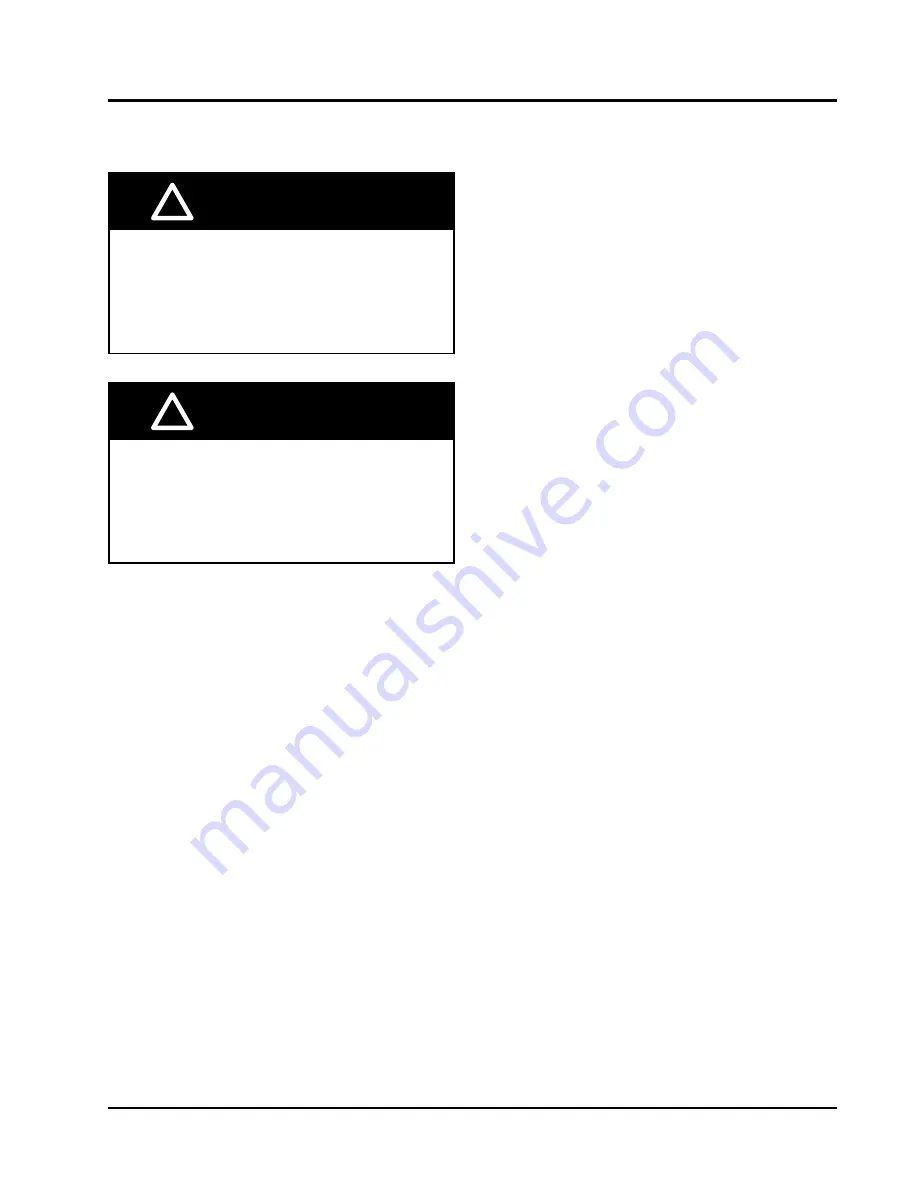
Manual 2100-670I
Page
41 of 47
MAINTENANCE
Standard Maintenance Procedures
4. Manually spin fan and blower motors to ensure
they turn freely. All motors are permanently
lubricated, so no oil is necessary.
5. Inspect free cooling damper actuator and linkage.
6. Install new air filter; check for additional filter
grilles internal to the structure.
7. Inspect the control panel of the system.
• Look for insect or rodent activity and remove
any nesting materials.
• Manually push contactor closed, observe for
movement—contactor points should have
minimal discoloration, no spalling or other
signs of arcing. Replace if doubtful.
• Check field and factory wiring for tightness and
look for signs of overheating (discoloration of
terminals or wire insulation).
8. Ensure that supply and return registers are not
obstructed, and more importantly, are not recycling
the air to one another. Adjust supply louvers if
necessary to direct discharge air away from any
direct route to the return grille.
9. Re-assemble wall-mount unit, turn breakers back on.
10. Enable system to LV1000 controller (see latest
revision of LV1000 Service Instructions 2100-
673).
11. Repeat steps for additional wall-mount units.
Bard Guard Anti-Theft System Option
While the system is powered, push DISARM/RESET
button to disarm the system. Once the button is
pushed, the blue LED will illuminate. As long as
the blue LED is illuminated, the Bard Guard system
is disarmed and will remain disarmed depending
on the preset time for up to 250 minutes (default
approximatey 15 minutes). After the preset time
expires, the system will rearm automatically.
For situations that require an individual unit to be
disconnected from the Bard Guard security system for
an extended period of service time (longer than the
maximum 250 minutes disarm time), place a jumper
across the appropriate terminals on the BG1000
terminal block to temporarily remove the unit from the
security system.
Be sure to remove the jumper from the
terminals after service has been completed.
See the latest revision of BG1000 Installation
Instructions 2100-672 for information on operating the
BG1000 controller.
1. Disable system from LV1000 controller (see latest
revision of LV1000 Service Instructions 2100-
673).
2. Turn off AC breakers at wall-mount units.
3. Check inlet sides of condenser and evaporator coils
for obstructions/debris—clean if necessary using a
quality manufactured coil cleaning product specific
for the evaporator or condenser coil.
• Condenser coil: Remove the upper side panels
from the condenser section. This will give
clear access to the inlet side of the coil for
cleaning. Follow the coil cleaner manufacturer’s
directions for necessary safety gear and
precautions, as well as for application and use.
More than one application may be necessary.
Rinse thoroughly.
• Evaporator coil: Open filter access panels
and remove filters. Apply specific evaporator
cleaner directly to the inlet side of coil, being
very careful not to overspray into insulation
or surrounding panels and wiring. Residual
cleaner and dissolved debris should drip into
the drain pan and leave the unit through the
condensate hose. More than one application
may be necessary. Rinse thoroughly.
Cut hazard.
Wear gloves to avoid contact with sharp
edges.
Failure to do so could result in personal
injury.
!
CAUTION
Electrical shock hazard.
Disconnect all power supplies before
servicing.
Failure to do so could result in electric shock
or death.
!
WARNING