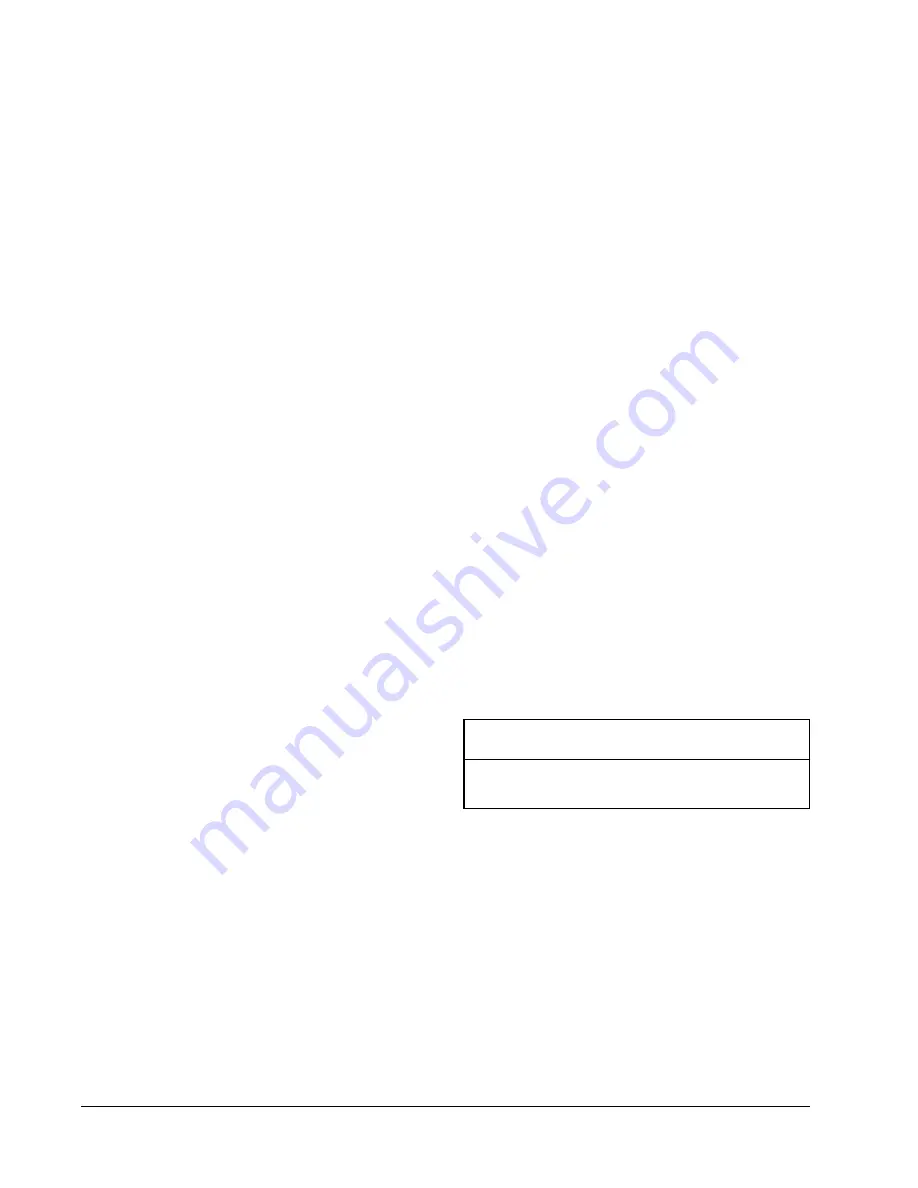
Manual 2100-392
Page 18
IMPORTANT
Do not set the blower “on” set point lever of
the combination fan/limit control above 150.
LOUVERS AND GRILLES
In calculating free area for above ventilation and
combustion air requirements, consideration shall be
given to the blocking effect of louvers, grilles, or
screens protecting openings. Screens used shall not be
smaller than 1/4 inch (6.3 mm) mesh and shall be
readily accessible for cleaning. If the free area through
a design of louver or grille is known, it shall be used in
calculating the size opening required to provide the free
area specified. If the design and free area is not known,
it may be assumed that wood louvers will have 30-35
percent free area and metal louvers and grilles will have
60-75 percent free area.
VENTING
The flue pipe to the chimney must be the same size as
the flue outlet of the furnace, have no reductions, be of
a corrosion-resistant material, and have an upward pitch
of 1/4” for every foot of horizontal run. A barometric
damper is supplied with the furnace and should be
installed in the flue pipe observing the instructions
packaged with the damper control. The barometric
damper opening must be located in the same
atmospheric pressure zone as the combustion air inlet to
the furnace. This furnace must not be vented into the
same chimney with any solid fuel burning appliance.
Masonry chimneys must be lined with a listed system or
other approved material that will resist corrosion,
softening, or cracking from flue gas at temperatures up
to 1800° F. See Standard for Installation of Oil Burning
Equipment NFPA31 and Standard for Chimneys
NFPA211 for additional information.
THERMOSTAT
NOTE: FC models do not wire directly to the
primary control. See wiring diagram on
Page 33.
These furnaces are designed to be controlled with any
24V heating or heating/cooling thermostat. The
heat/cool thermostats must be designed for independent
heat/cool transformer circuits to assure that the 24V
transformer built into the oil primary control does not
conflict with the main furnace 24V transformer. The
heat anticipator should be set at 0.20A. This is a
nominal setting. The thermostat circuit should be
checked to verify setting.
FAN AND LIMIT CONTROL
The fan and limit control is factory installed in all units.
See Table 13 for factory settings. The fan on/off
settings may have to be varied due to the static pressure
imposed upon the system. The limit control is factory
set at maximum fixed stop allowable and must not be
reset.
When the installation is completed, measure the air
temperature in the discharge plenum and return air
plenum. The temperature rise across the unit should
fall within the “Rise Range” as shown in Table 13. It is
normally desirable to operate in the middle of the range
unless air conditioning or other installation
requirements make that unfeasible. The speed of the
blower may have to be either increased or decreased to
obtain this temperature. The blower is equipped with a
3 or 4 speed motor to make these adjustments.
The fan and limit control in the burner compartment
governs the blower operation by means of two
temperature selections. One lever is set at 140 degrees
for example to start the blower, and the other lever is at
a lower temperature, 110 degrees to stop the blower.
These settings may be varied to suit the homeowner’s
comfort. A greater temperature difference between
settings may result in less repetition of the blower
operation at the end of the heating cycle. A low “off”
temperature is recommended for longer blower
operation as this keeps the air of the home in more
constant circulation.
NOTE: On model FC085D36D the blower “on”
setting is timed to assure blower operation.
This blower “on” setting cannot be adjusted.
Содержание FC085D36D
Страница 33: ...Manual 2100 392 Page 31...
Страница 34: ...Manual 2100 392 Page 32...
Страница 35: ...Manual 2100 392 Page 33...