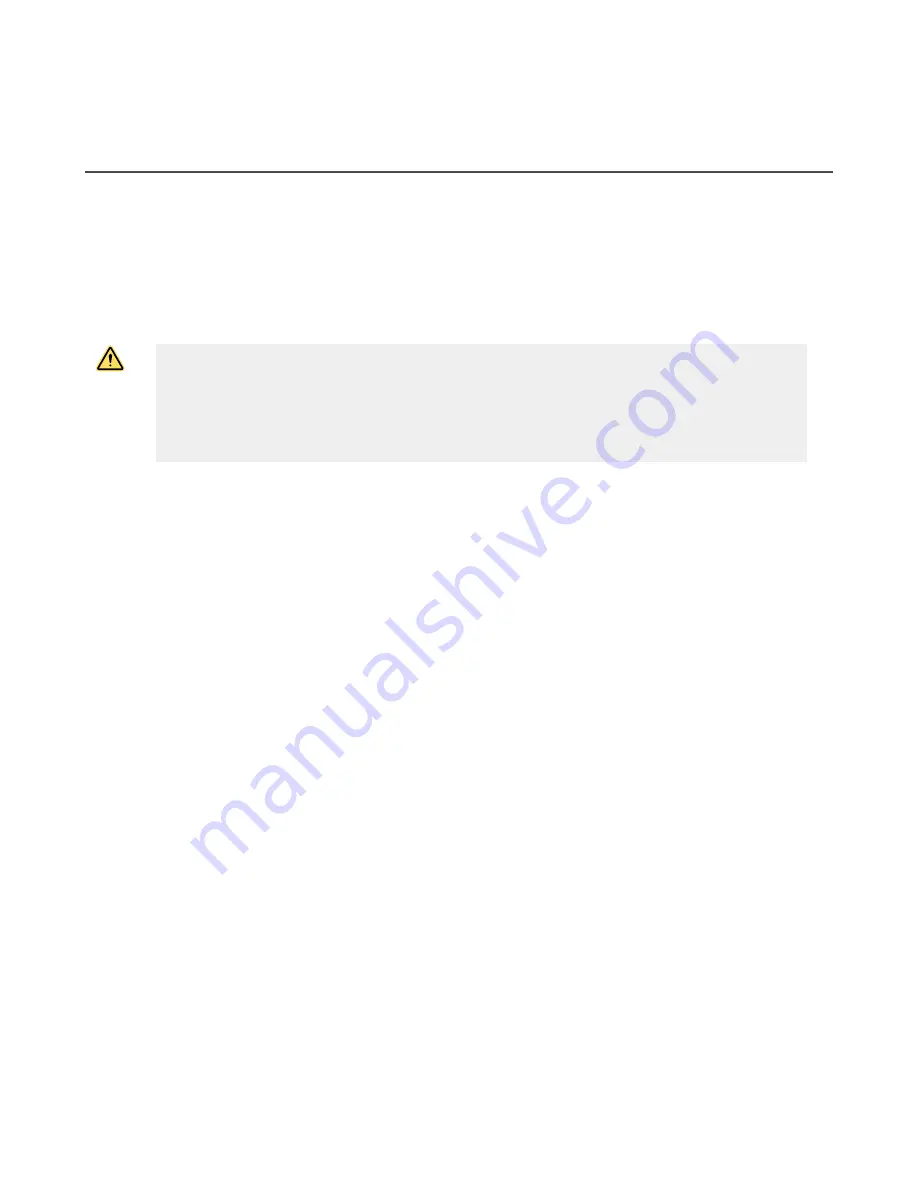
6. If the S4B System passes all checks during the trip test, go on to
Electrical Connections to the Guarded Machine
on
page 34.
6.5 Electrical Connections to the Guarded Machine
Verify that power has been removed from the S4B and the guarded machine. Make the permanent electrical connections as
required by each individual application.
Lockout/tagout procedures may be required (refer to OSHA 1910.147, ANSI Z244-1, ISO 14118, or the appropriate standard
for controlling hazardous energy). Follow relevant electrical standards and wiring codes, such as the NEC, NFPA79 or IEC
60204-1.
Supply power should already be connected. The S4B must also have been aligned and passed the Initial Checkout, as
described in
The final connections to be made or verified are:
•
OSSD outputs
WARNING:
•
Risk of electric shock
•
Failure to follow these instructions could result in serious injury or death.
•
Disconnect or turn off power before installing, removing, or servicing the device.
•
Install and connect the device in accordance with the National Electrical Code (NEC) and any
applicable local code requirements and supply the device with an appropriate fuse box or circuit
breaker (see
Specifications
).
6.5.1 Protective Stop (Safety Stop) Circuits
A protective stop (safety stop) allows for an orderly cessation of motion for safeguarding purposes, which results in a stop of
motion and removal of power from the Machine Primary Control Elements (MPCE) (assuming this does not create additional
hazards).
A protective stop circuit typically comprises a minimum of two normally open contacts from forced-guided, mechanically
linked relays, which are monitored through External Device Monitoring (EDM) to detect certain failures, to prevent the loss of
the safety function. Such a circuit can be described as a "safe switching point".
Typically, protective stop circuits are either single channel, which is a series connection of at least two normally open
contacts; or dual-channel, which is a separate connection of two normally open contacts. In either method, the safety function
relies on the use of redundant contacts to control a single hazard. If one contact fails ON, the second contact arrests the
hazards and prevents the next cycle from occurring.
The interfacing of the protective stop circuits must be accomplished so that the safety function cannot be suspended,
overridden, or defeated, unless accomplished in a manner of the same or greater degree of safety as the machine's safety
related control system that includes the S4B.
A Banner XS26-2 Safety Controller with XS1ro or XS2ro Relay Expansion Module, Banner SC10-2roe Safety Controller, or
Banner UM-FA-xA Universal Safety Module provides a series connection of redundant contacts that form protective stop
circuits for use in either single-channel or dual-channel control.
Output Signal Switching Devices (OSSDs) and External Device Monitoring
(EDM)
The S4B is able to detect faults on OSSD1 and OSSD2. These faults include short circuits to +24 V DC and 0 V, and
between OSSD1 and OSSD2.
Both Output Signal Switching Device (OSSD) outputs must be connected to the machine control so that the machine's
safety-related control system interrupts the circuit or power to the Machine Primary Control Element(s) (MPCE), resulting in a
non-hazardous condition.
Final Switching Devices (FSDs) typically accomplish this when the OSSDs go to an OFF state.
Refer to the output specifications in the Receiver Specifications and these warnings before making OSSD output connections
and interfacing the S4B to the machine.
S4B Safety Light Curtain
34
www.bannerengineering.com - Tel: + 1 888 373 6767