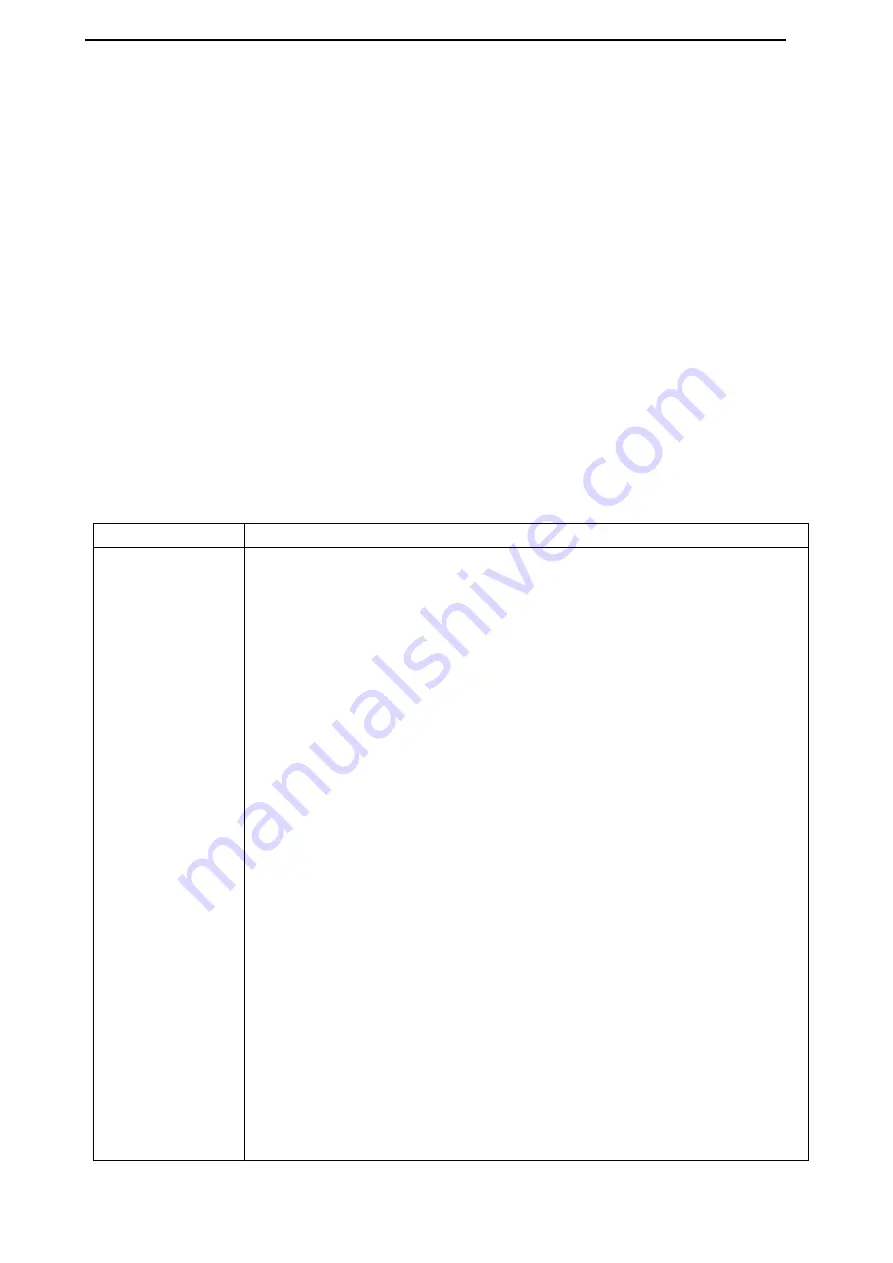
BANLAW PRODUCT DATA SHEET FILLSAFE ZERO 2” NPT F
xM FLOW CONTROL VALVE
Doc ID: PRH-OFP-25 Version: 4.0
Page
17
of
20
Please ensure you have the latest version of this document.
1.
Ensure adequate controls and condition monitoring are in place to ensure the contamination levels
(and other specifications) of your fuel supply are maintained
–
PREVENT
poor quality fuel entering
your sites fuel infrastructure and plant equipment.
2.
Install inline (bulk) filtration on all diesel dispensing lines
–
contact Banlaw for advice.
3.
Maintain the use of the Receiver Dust Cap and Nozzle Anchors, Holsters, or Dust Caps.
4.
Remove any contamination from the dry-break Receiver (front end)
prior
to connecting a Nozzle.
5.
Visually inspect the Receiver for excessive wear & tear or damage
prior
to connecting a Nozzle.
6.
Replace the BFCV50NPTF Valve assembly no later than every 8 years.
7.
Replace the Internal Pilot Line no later than every 2 years.
7.2
Banlaw Site Service and Preventative Maintenance
Clients can benefit from a
Banlaw Service Level Agreement (SLA)
to assist in the preventative and corrective
maintenance of a FillSafe Zero system onsite, in addition to other diesel, fuels, oils and coolant infrastructure.
Clients with an SLA can
focus on their core business activities
and allow experienced Banlaw technicians and
engineers to help keep such infrastructure operating at optimum
safety, performance and reliability.
8
TROUBLESHOOTING
This section provides troubleshooting recommendations for the BFCV50NPTF Valve and FillSafe Zero
system
when installed, operated and maintained in accordance with Banlaw guidelines.
PROBLEM
PROBABLE CAUSE AND SOLUTION
Premature nozzle
shut-off at the
start
of or
during
the
refuelling.
•
Zero system requires bleeding (to remove air). With the supply pump
running, cycle nozzle T-handle between ON and OFF several times to
resolve this issue (also refer section 5.3).
•
Residual pressure in Pilot line. Cycle nozzle T-handle between ON and OFF
several times to resolve this issue.
•
Pilot line blocked/obstructed, kinked or undersized. Check Pilot line size
and connections for blockages or obstructions. Avoid the use of restricted
bore style fittings, sharp elbows etc. within the Pilot Line routing between
the Flow Control Valve and Level Sensor.
•
Level Sensor installed too high (over 4m (13’)) above the Flow Control
Valve).
•
The BVLS model “venting” Level Sensor is
not installed correctly onto the
tank, e.g. installed within an “extended” socket or riser pipe etc. Refer to
BVLS requirements (i.e. PDS document) and rectify.
•
Float Valve at base of Level Sensor is “stuck” in the closed (up) position.
Remove Level Sensor, investigate, identify root cause and rectify.
•
Faulty Level Sensor. Replace Level Sensor.
•
Fuel flow out of the Flow Control Valve outlet ports is “choked” –
i.e. the
Valve is installed within a pipe, extended socket, etc. or installed too close
to the side of the tank or internal tank baffle (plate). Refer section 5.1.
•
Piston mechanism within Flow Control Valve is “stuck” in the closed
(forward) or otherwise restrict
ed in its “free” reciprocating action.
Remove Valve, investigate, identify root cause and rectify.
•
Faulty Flow Control Valve. Replace Flow Control Valve.
•
Flow rate below recommended minimum. Increase delivery flow rate.
•
Flow rate above recommended maximum. Reduce delivery flow rate.