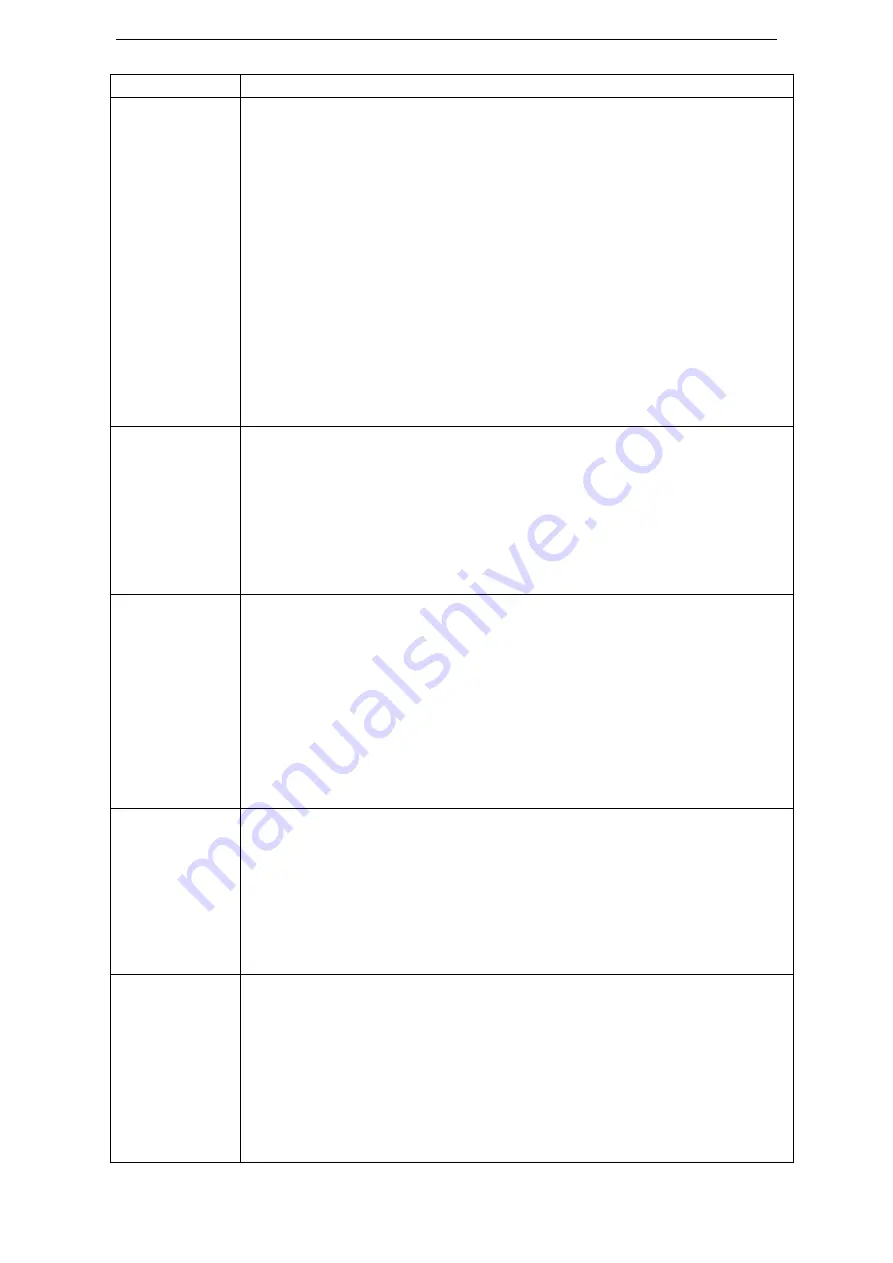
BANLAW PRODUCT DATA SHEET
DRY-BREAK DIESEL REFUELLING NOZZLES
Doc ID: PRH-REF-70 Version: 7.0
Page
31
of
32
Please ensure you have the latest version of this document.
PROBLEM
PROBABLE CAUSE AND SOLUTION
o
Fuel and/or air leakage from tank(s)
after
closure of the vent(s)
–
identify source of leakage and effectively seal (e.g. leaking
manual filler point cap).
•
Nozzle or OFP system flow rate outside the recommended range.
Maintain flowrate within the recommended minimum and maximum
range.
•
Nozzle operating handle being forcibly held in the ON (open) position
during refuelling
–
assess root cause(s) and rectify.
•
Nozzle is reopened after the tank is filled
–
train operator(s) on correct
nozzle operation.
•
Nozzle spring setting too “high” (heavy) for application. Contact Banlaw
or your nearest Banlaw agent for advice.
•
Vent pressure relief spring setting below Nozzle and Receiver shutoff
value. Contact Banlaw or your nearest Banlaw agent for advice.
Fluid Leakage
from Nozzle
•
Faulty fluid seal(s) within Nozzle
–
replace Nozzle and have faulty Nozzle
serviced.
•
Over-pressurisation of Nozzle
–
maintain fluid pressure under the SWP.
•
Temperature below minimum operating temperature of the Nozzle
–
replace Nozzle with a Banlaw “arctic” series Nozzle.
•
A foreign object is caught within the Nozzle
–
investigate.
•
Fuel overly contaminated
–
investigate and rectify.
Fluid Leakage
between Nozzle
and Receiver
during
Refuelling
•
Faulty fluid seal(s) within Nozzle
–
replace Nozzle and have faulty Nozzle
serviced.
•
Sealing surfaces on Receiver are damaged
–
replace Receiver.
•
Contamination (dirt, mud etc.) build-up within Nozzle
–
clean Nozzle and
Receiver or replace Nozzle and have faulty Nozzle serviced. Ensure
Receiver Dust Caps and a Nozzle Holster or Anchor are used.
•
Fuel overly contaminated
–
investigate and rectify.
•
Temperature below minimum operating temperature of the Nozzle
–
replace Nozzle with a Banlaw “arctic” series Nozzle.
Nozzle
Uncouples from
Receiver During
Refuelling
•
Incorrect combination of Nozzle and Receiver. Confirm compatibility.
Only use the correct combination of Nozzle and Receiver.
•
Worn ball lock mechanism on Nozzle and/or Receiver. Inspect both
equipment and replace if necessary.
•
Contamination within ball lock groove on receiver body. Clean
thoroughly and reconnect nozzle.
•
Nozzle improperly coupled to Receiver. Try again.
No fuel flow
through Nozzle
•
Valve upstream or downstream within system is closed
–
investigate.
•
Banlaw FuelTrack receiver ID tag (code) has not been entered into the
onsite FMS database and/or properly configured within the database.
•
FuelTrack receiver ID tag has not been received by local FMS depot;
o
Existing fault with auto ID dry-break system, e.g. short circuit or
under-voltage
–
investigate and rectify.
o
Faulty auto ID chip in receiver
–
install new Banlaw FuelTrack
Receiver.