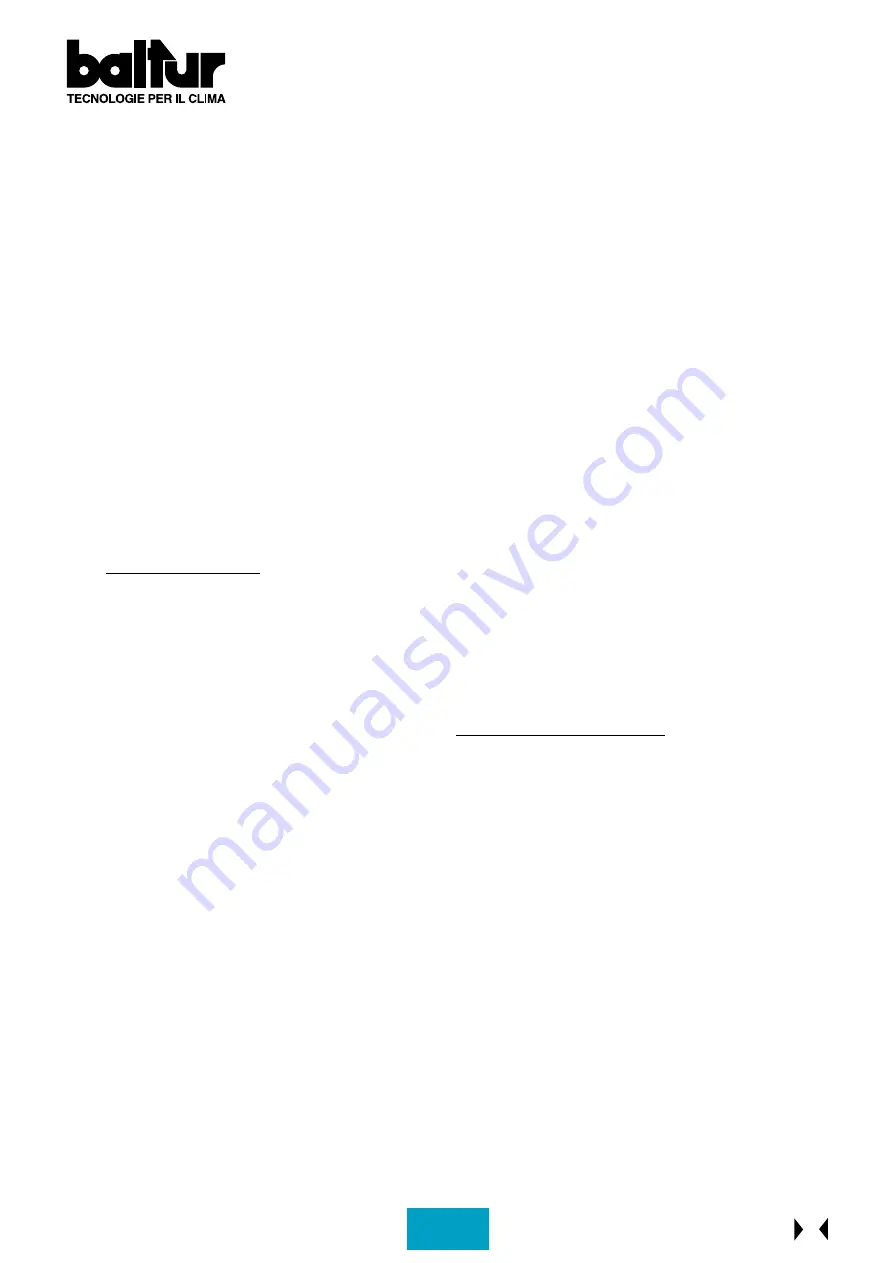
43
EN
Carry out a visual control of the flame and proceed, if necessary, with regulating the combustion air and the gas
by operating the adjustable screws of the regulating disk.
The operation described above should be repeated progressively (by moving forward the disk about 12° at a
time) and modifying every time, if necessary, the fuel/air ratio during the whole modulation run.
Make sure that the increase in fuel delivery occurs gradually and that maximum delivery is reached at the end of
the modulation run.
This is necessary in order to ensure that the modulation functions with good graduality.
The positions of the screws that command the fuel may need to be modified in order to obtain the graduality
required.
14)
With the burner operating at maximum delivery required for the boiler, check combustion with the appropriate
instruments and modify, if necessary, the previous regulation carried out after a visual control only (CO2 max. =
10% - CO max. = 0,1%).
15)
We recommend controlling the combustion with the appropriate instruments and, if necessary, modify the previous
regulation carried out, after a visual control only, also in a few intermediate points of the modulation run.
16)
Check that modulation function automatically by putting the AUT - O - MAN switch in the "AUT" position and the
MIN - O - MAX switch in the "O" position.
In this way, modulation is activated exclusively by the automatic command of the boiler's probe, if the burner is
a BGN...M (modulating) version, or on the command of the thermostat or pressure switch of the 2nd stage, if the
burner is a BGN...DSPGN (two-stage progressive) version.
(See instruction "Electronic Potentiality Regulator RWF ... for the modulating version).
17)
The air pressure switch has the job of bringing the control box to a safety shut down if the air pressure is not at
the correct value.
Therefore, the air pressure switch must be regulated in such a way as to intervene by closing the contact
(foreseen to by closed while working) when the air pressure in the burner has reached a sufficient level.
The pressure switch is self-controlled and therefore it must close the contact (fan stops and consequently there
is an absence of air pressure in the burner) if it does not, the control box will be inserted (the burner remains at
a stadstill).It must be specified that if the contact is not closed during working (insufficient air pressure), the
control box will carry out its cycle, but the ignition transformer will not be inserted and the gas pilot valves will not
open. Consequently, the burner will go to "shut down".
Check that the air pressure switch functions properly with burner at minimum delivery, increase the regulating
value until it reaches intervention point and the burner should go to shut down. To unblock the burner, press the
special push-button and return the pressure switch regulator to a sufficient value in order to measure the air
pressure existing during the pre-ventilation phase.
18)
The pressure switches which control the gas pressure (minimum and maximum) have the job of stopping the
burner functioning when the gas pressure is not within the values specified. From the specific functions of the
pressure switches, it is evident that the pressure switch controls the minimum pressure must make use of the
contact, which is closed, when it measures a pressure which exceeds that at which it has been set.
The maximum pressure switch must make use of the contact, which is closed, when it measures a pressure
below that at which it has been set.
The minimum and maximum gas pressure switches should be regulated during the burner's general inspection
and should be in function with the pressure found each time.
The pressure switches have been electrically connected in series and therefore the intervention (by this we
mean the opening of the circuit) of any one of the gas pressure switches, will prevent the control box and thus
the burner from starting up.
When the burner is operating (flame lit), the intervention of the gas pressure switches (opening of the circuit)
determines the immediate arrest of the burner.
During the burner's general inspection, check the correct functioning of the pressure switches. By operating the
respective regulating device, it is possible to control the pressure switch's intervention (opening of circuit) which
causes the burner's arrest.
19)
Check the efficiency of the flame detector (ionisation electrode) by detaching the wire coming from the electrode
and by turning on the burner.
The control box should carry out completely its cycle and two seconds after the ignition flame (pilot) is formed, it
should go to "shut down". This control should also be carried out when the burner is already operating.
Содержание BGN 17 DSPGN
Страница 12: ...12 PORTATE m 3 h GAS METANO d 0 85 IN TUBI GAS COMMERCIALI UNI 3824 68 PERDITA CARICO MAX 5 mm CA N BT 1387...
Страница 20: ...20 SCHEMA DI PRINCIPIO REGOLAZIONE ARIA PER BRUCIATORI A GAS N BT 8769 1 IT...
Страница 29: ...29 APPARECCHIATURA DI COMANDO E CONTROLLO PER BRUCIATORI A GAS LMG 2 IT...
Страница 30: ...30 APPARECCHIATURA DI COMANDO E CONTROLLO PER BRUCIATORI A GAS LMG 2 IT...
Страница 31: ...31 APPARECCHIATURA DI COMANDO E CONTROLLO PER BRUCIATORI A GAS LMG 2 IT...
Страница 32: ...32 APPARECCHIATURA DI COMANDO E CONTROLLO PER BRUCIATORI A GAS LMG 2 IT...
Страница 36: ...36 EN GENERAL DIAGRAM FOR INSTALLATION OF GATE FILTER STABILIZER ANTIVIBRATION JOINT OPENABLE PITTING N BT 8780...
Страница 45: ...45 N BT 8769 1 AIR REGULATION PRINCIPLE DIAGRAM FOR GAS BURNERS EN...
Страница 52: ...52 EN...
Страница 53: ...53 EN GAS BURNER CONTROLS LMG 2...
Страница 54: ...54 EN GAS BURNER CONTROLS LMG 2...
Страница 55: ...55 EN GAS BURNER CONTROLS LMG 2...
Страница 56: ...56 EN GAS BURNER CONTROLS LMG 2...
Страница 60: ......
Страница 61: ......
Страница 62: ......
Страница 63: ...62...