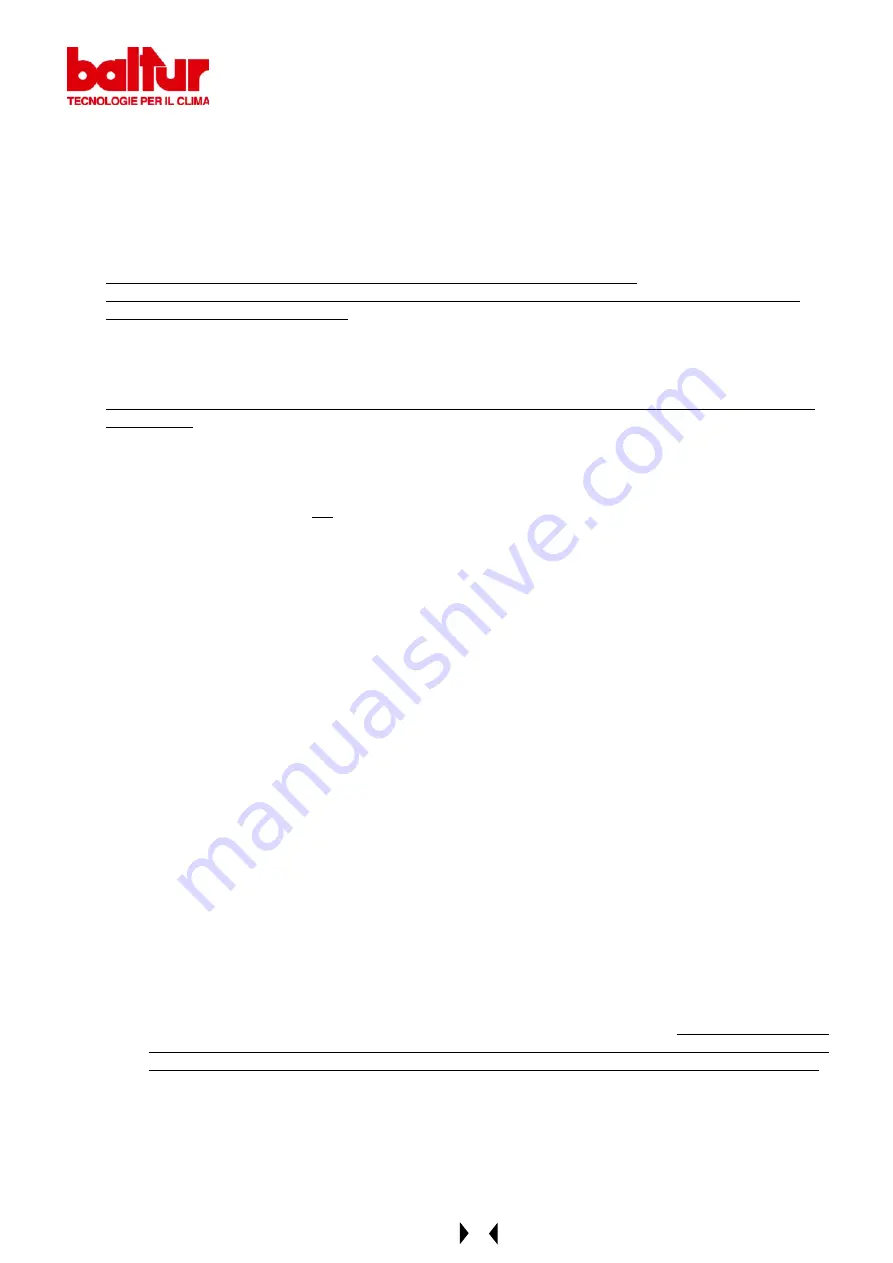
16
STARTING UP AND REGULATION WITH METHANE
1)
If not already done at the moment of connecting the burner to the gas pipeline, it is indispensable to carry
out a purge of the air contained in the pipeline. As a precaution, special care should be taken and doors and
windows should be opened. Open the pipe union on the pipeline situated near the burner and then open a little
the gas cut-off cock (or cocks). When the characteristic odour of gas can be smelled, close the cut-off cock.
Wait until the gas present in room has dispersed, and then reconnect the burner to the gas pipeline. Subsequently,
re-open the gas cut-off cock.
2)
Check that there is water in the boiler and that the system’s gate valves are open.
3)
Check, with absolute certainty that the discharge of combustion products can take place freely (boiler and
chimney lock-gates should be open).
4)
Make sure that the voltage of the electric line to which the burner is to be connected,corresponds to that
required by the burner and that the electrical connections (motor and principle line) have been prepared to mach
the voltage rating available. Also check that all the electrical connections carried out on the spot are in accordance
with our electric wiring diagram.
5)
Make sure that the combustion head is long enough to enter the furnace to the extent specified by the boiler
manufacturer. Check that the device which regulates the air on the combustion head is in the position considered
necessary for the fuel delivery required (air passage between the disk and the head should be considerably
reduced when the fuel delivery is reduced; on the other hand, when the fuel delivery is fairly high, the air passage
between the disk and the head should be relatively open). See Chapter “Air Regulation on the Combustion Head”.
6)
Apply a manometer with an adequate scale (if the entity of pressure forecast allows it is preferable to use a
column of water instrument, do not use a pointer instrument for moderate pressure) to the pressure plug on the
gas pressure switch.
7)
Open, to the quantity considered necessary, the flow regulator incorporated in the ignition flame valve (s)
(pilot). Check that the combustion air regulation shutter is in the right position; if necessary, modify it by operating
the adjustable screws of the regulating disk.
8)
Remove the protective cover from the disk on which are inserted the screws which regulate the gas and air
delivery, and unloosen the locking screws.
9)
With the switch on the burner’s control panel in the “o” position and the main switch inserted check, by manually
closing the relay, that the motor rotates in the right direction.
If it does not, exchange the places of two cables of the motor’s supply line in order to invert its sense of rotation.
10)
Now insert the switch on the command panel and put the modulating switches in the MIN (minimum) and MAN
(manual) positions. The control box receives voltage in this way and the programmer turns on the burner as
described in Chapter “Description of Operations.
Note
: Pre-ventilation is carried out with air open and, during this phase, the servomotor regulating the delivery
(gas/air) is inserted and completes the whole opening run until it reaches the “maximum” position.
Subsequently, the servomotor which regulates delivery (gas/air) returns to the starting position (minimum).
Only when modulation has returned to the “minimum” position, does the control box proceed with its
ignition programme and insert the transformer and the gas ignition valves for ignition.
During the pre-ventilation phase check that the air pressure switch effects a changeover (it should pass from a
closed position without measurement of pressure to a closed position with measurement of air pressure).
If the air pressure switch does not measure sufficient pressure (it will not effect the changeover) and neither the
ignition transformer nor the gas ignition flame valves will be inserted and the control box will go to “shut down”.
It should be pointed out that “shut downs” during the first ignition phase are considered normal.
This is because air still exists in the pipeline of the valve incline and must be expelled before it is possible to have
a stable flame. To unblock the control box, press the relevant push-button.
Note
: If gas flame detection is carried out with an ionisation electrode, the shut down (with flame presence)
could be caused by flame instability in the ionisation zone. This fault can be eliminated by operating the
combustion head regulator (move it backwards or forwards) until the necessary conditions to ensure flame
stability and sufficient intensity and stability of the ionisation current are obtained. It could happen that the
ionisation current is held up by the current of the ignition transformer (the two currents have to run the
same course on the burner’s earth) and so the burner goes to “shut down” due to insufficient ionisation.
This can be remedied by inverting the input (230 V. Side) of the ignition transformer (change the places of
two wires that take voltage to the transformer). A shut down with flame presence could also be caused by
the burner’s casing not being properly grounded. The minimum value of the ionisation current to ensure the
working of the control box (LFL...) is 7 micro-amperes; normally the ionisation current is decidedly higher
(this value is shown on the wiring diagram). To check the ionisation current, connect a microammeter with
an adequate scale “in series” to the ionisation current. The high isolation wire that comes from the electrode
must be inserted to the negative (sign -) of the microammeter.
Содержание BGN 100 DSPGN
Страница 6: ...6 BGN 40 DSPGN 100 DSPGN N 7604 2 Rev 02 02 96 BGN 120 DSPGN 350 DSPGN N 7605 5 Rev 17 11 97...
Страница 19: ...19 AIR REGULATION PRINCIPLE DIAGRAM FOR GAS BURNERS BT 8769 1...
Страница 35: ......
Страница 36: ......
Страница 37: ......
Страница 38: ......
Страница 39: ......
Страница 40: ......
Страница 41: ......
Страница 42: ......
Страница 43: ......
Страница 44: ......
Страница 45: ......
Страница 46: ......
Страница 47: ......