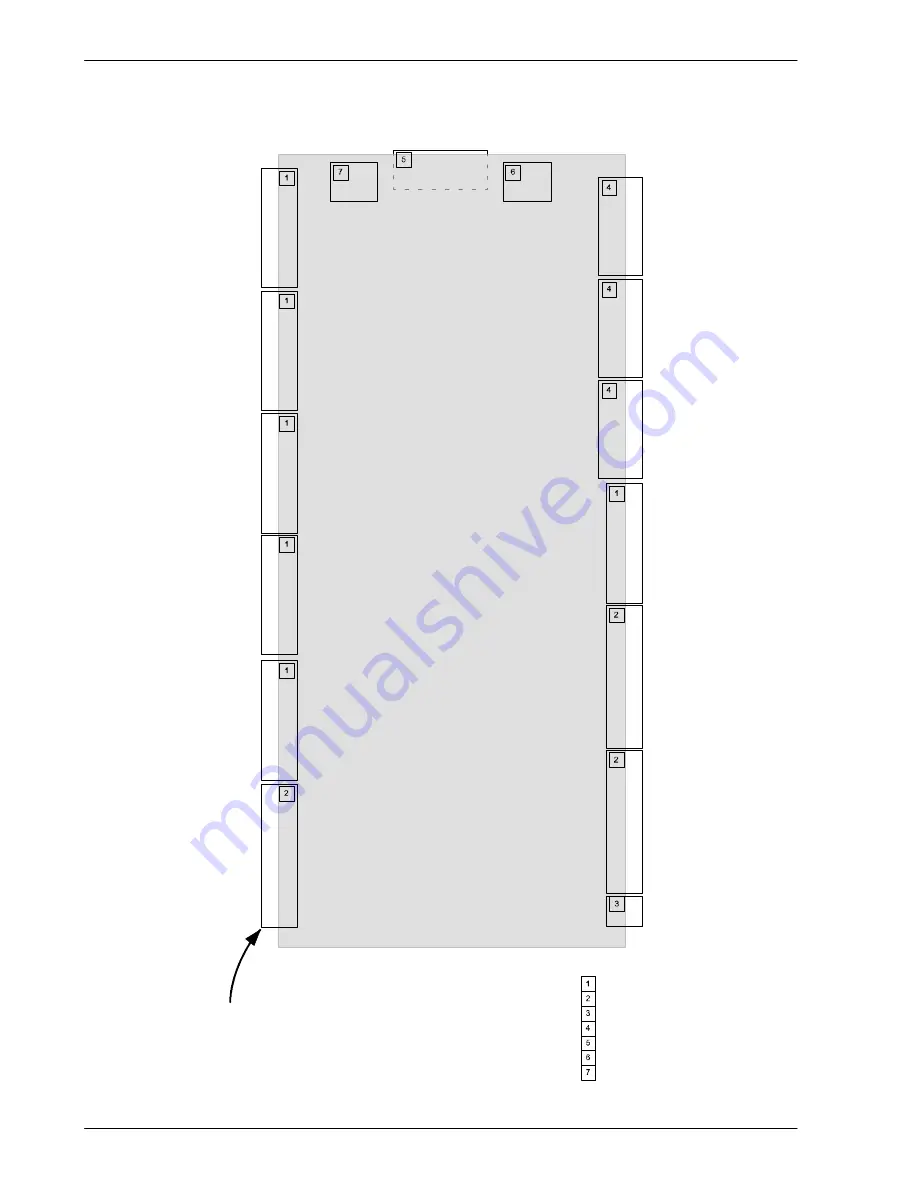
www.supportme.net
4-2 Input / Output
MN1924
4.1.1 Connector locations
Tightening torque for terminal block
connections is 0.3Nm (2.65 lbf-in)
X12 AIN 0-1
& relay
X7 Encoder2
X6 Encoder1
X4 DOUT 8-10
X2 STEP 0-1
AIN0+
AIN0-
AGND
AIN1+
AIN1-
Shield
REL COM
REL NC
REL NO
REL COM
CREF2
CREF1
CREF0
!RSTIN
USR GND
USR V+
USR V+
DOUT10
DOUT9
DOUT8
Shield
DIR1+
DIR1-
STEP1+
STEP1-
DGND
Shield
DIR0+
DIR0-
STEP0+
STEP0-
DGND
Serial
Required mating connectors
:
Sauro CTF10008
Sauro CTF12008
Sauro CTF02008
9-pin D-type plug (male)
9-pin D-type socket (female)
RJ45 plug
USB type B plug
1
2
3
4
5
6
7
8
9
10
12
11
10
9
8
7
6
5
4
3
2
1
10
9
8
7
6
5
4
3
2
1
X11 DOUT 0-7
DOUT0
DOUT1
DOUT2
DOUT3
DOUT4
DOUT5
DOUT6
DOUT7
USR V+
USR GND
1
2
3
4
5
6
7
8
9
10
X10 DIN 0-3
(fast interrupts)
DIN3
Shield
CREF0
DIN2
Shield
CREF0
DIN1
Shield
CREF0
DIN0
1
2
3
4
5
6
7
8
9
10
X9 DIN 4-11
DIN11
DIN10
DIN9
DIN8
DIN7
DIN6
DIN5
DIN4
CREF1
Shield
1
2
3
4
5
6
7
8
9
10
X8 DIN 12-19
DIN19
DIN18
DIN17
DIN16
DIN15
DIN14
DIN13
DIN12
CREF2
Shield
1
2
3
4
5
6
7
8
9
10
X13 AOUT 0-3
(demands)
DEMAND0
AGND
Shield
DEMAND1
AGND
Shield
DEMAND2
AGND
Shield
DEMAND3
AGND
Shield
1
2
3
4
5
6
7
8
9
10
11
12
X3 STEP 2-3
Shield
DIR3+
DIR3-
STEP3+
STEP3-
DGND
Shield
DIR2+
DIR2-
STEP2+
STEP2-
DGND
12
11
10
9
8
7
6
5
4
3
2
1
X5 Encoder0
X1 +24V in
+24V
0V
2
1
CAN
USB
Содержание Nextmove ESB
Страница 1: ...NextMove ESB Motion Controller MOTION CONTROL Installation Manual 1 04 MN1924...
Страница 2: ......
Страница 6: ...iv Contents MN1924...
Страница 16: ...www supportme net 3 4 Basic Installation MN1924...
Страница 42: ...www supportme net 4 26 Input Output MN1924...
Страница 57: ...www supportme net Operation 5 15 MN1924 Figure 28 The NextMove ESB servo loop...
Страница 88: ...www supportme net A 4 General MN1924...
Страница 94: ...Index MN1924...
Страница 96: ...Comments MN1924 Thank you for taking the time to help us...
Страница 97: ......