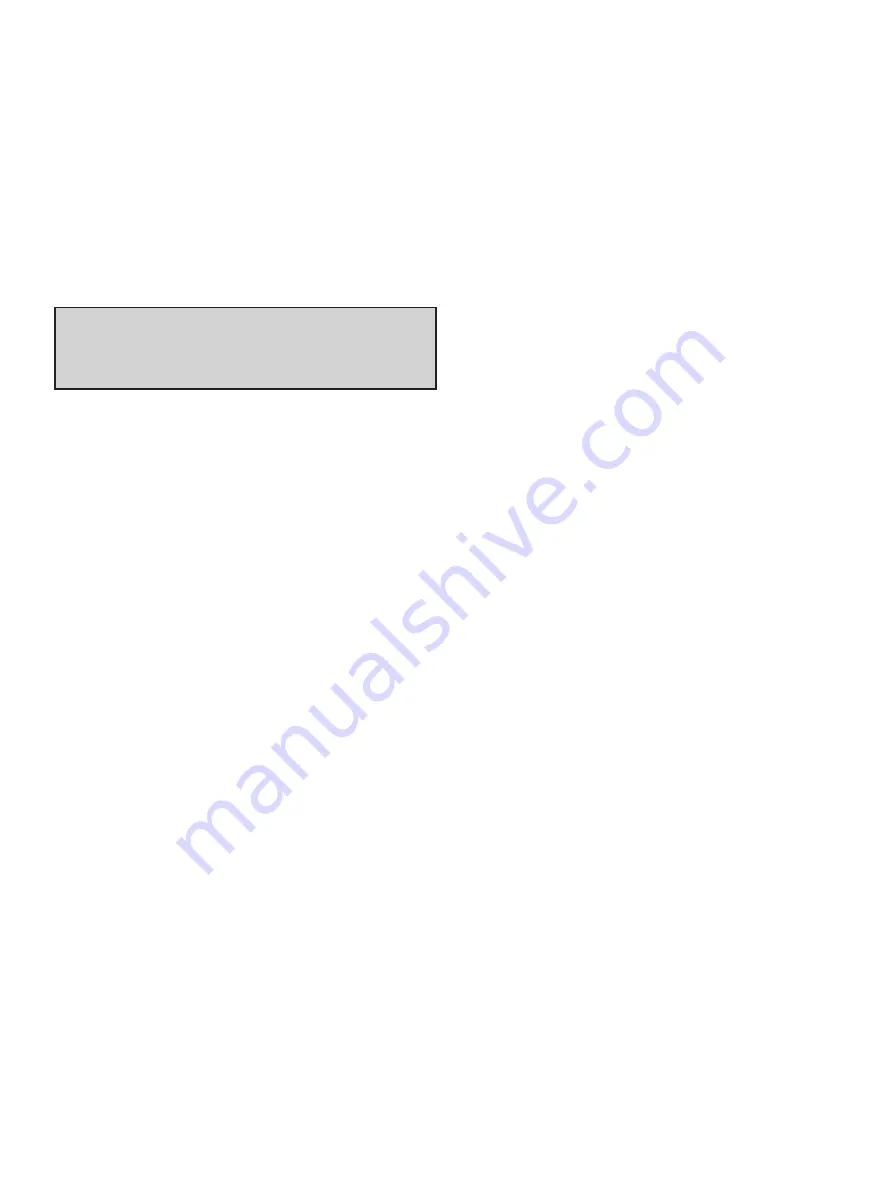
Masoneilan 84003 Series SteamForm Installation Guide | 9
Copyright 2020 Baker Hughes Company. All rights reserved.
Strainers
The SteamForm spray water injection system is made up
of a variety of nozzle types and sizes to ensure optimum
results in a variety of applications. Available nozzle types
include flat spray pattern nozzles, hollow-cone spray
pattern nozzles, and variable orifice nozzles. Each nozzle
is selected based on water quantity required and the
available water pressure differential. These nozzles all
possess a unique spray pattern and droplet size, which
dictates the performance capabilities of the SteamForm.
To prevent blockage of these small orifice nozzles, an
inline strainer is strongly recommended on all spray water
lines. Regardless of the quality of the water source, the
possibility always exists that scale, debris, or other pieces
of particulate can be found in the water system. This
particulate can be large enough to clog or block the flow
exiting the nozzle.
The strainer must always be installed as close to the
nozzles as possible to collect any possible scale or
debris that can be in the water system.
Baker Hughes
recommends minimum 100 MESH screen
strainer
at upstream of the water spray control valve. Strainers
must be monitored and maintained regularly to ensure
blockage does not occur. See figure 5 on next page for
strainer location, and general water injection control valve
recommendation.
Valve Installation
The steam conditioning valve is an instrumental piece
of equipment used to prolong the active life of the plant
and critical pieces of equipment. When properly used,
the steam conditioning valve keeps a plant on-line during
load rejections and allows the system to return to normal
operation with minimized delays. It can also be used to
protect sensitive downstream equipment from heat and
pressure excursions or during the plant start-up phase.
To protect the plant and its equipment, it is important
not to overlook the necessary steps that prolong the
life of the steam conditioning valve. Several steps can
be taken to ensure the valve is installed in the best
possible orientation, and it is easily accessible for routine
maintenance. The guidelines below are suggested to limit
exposure to undesirable scenarios and prolong the useful
life of the valve.
Valve Support
All valve supports must be mounted to fixed points
within the piping system. Excess strain on the valve
components must be avoided whenever possible. The
SteamForm can never be used as a fixed point at which
a system is mounted on. Supports must not be welded to
the SteamForm valve body.
Actuator Support
Actuation support can become a concern in the case of
horizontal actuation installations. When large actuators
are mounted horizontally, a spring-loaded saddle support
system must be used to cradle the actuator and minimize
stress applied to the valve plug and stem. The saddle
support system must be periodically monitored to verify
the support is not out of its original tuning. If not properly
maintained, the support system can become a source of
additional stress on the actuator, plug, and stem.
Warning:
Failure to install a strainer can result in
blockage of the nozzle, damage to heat sensitive
equipment, and plant shutdown.