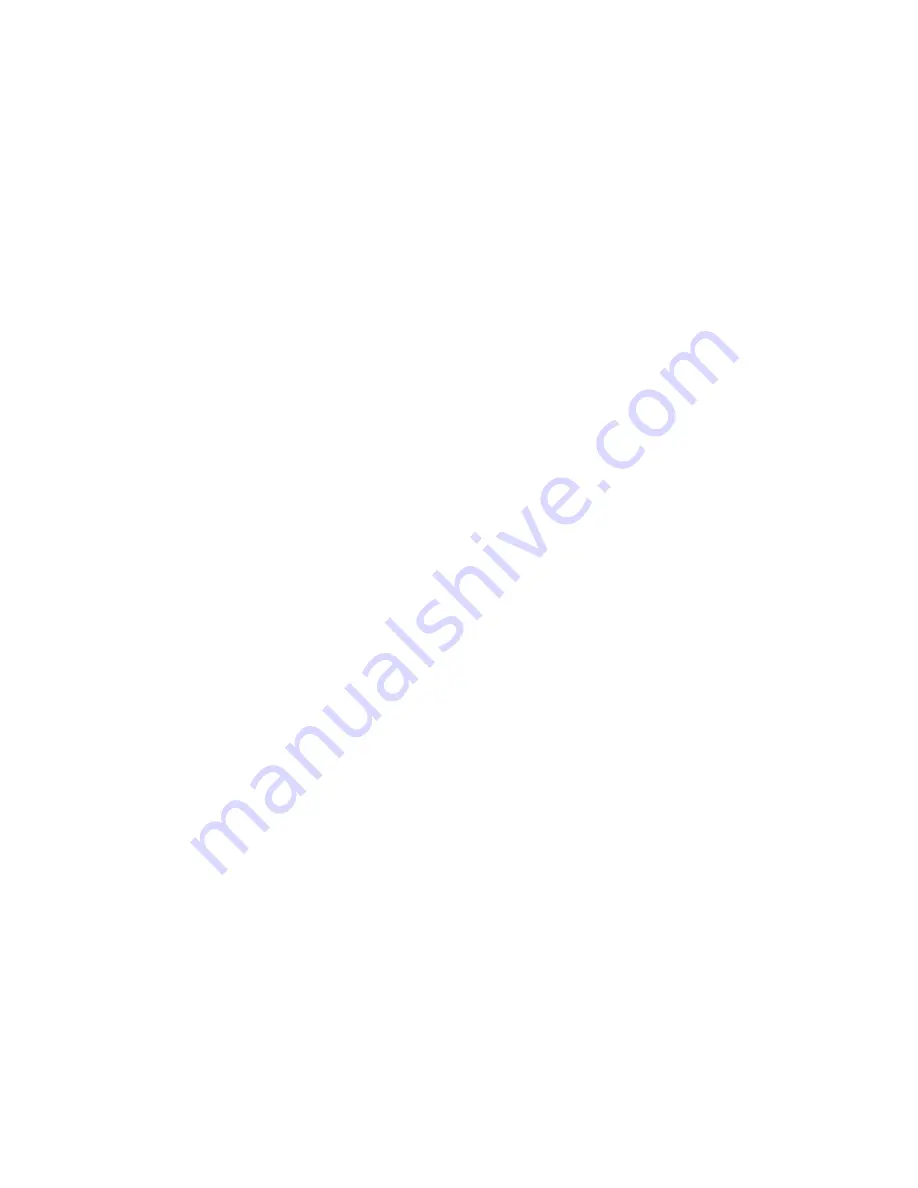
Consolidated 13900 Series POSRV Maintenance Manual
|
33
© 2018 Baker Hughes, a GE company. All rights reserved.
XXIV. Manufacturer’s Field Service, Repair
and Training Programs
A. Field Service
BHGE maintains the largest and most competent field
service staff in the industry. Service technicians are
located at strategic points throughout the United States
to respond to customers’ requirements for service. Each
Service technician is factory trained and long experienced in
servicing safety valves. BHGE’s Service technicians restore
disc and seat bushing critical dimensions which affect valve
performance, and are capable of modernizing valves in the
field.
It is highly recommended that the professional talents of a
BHGE Field Service technician be employed to make final
field adjustments during the initial setting of all Consolidated
Safety Valves.
B. Factory Repair Facilities
BHGE’s Consolidated factory maintains a Repair Center. The
Repair Department, in conjunction with the manufacturing
facilities, is equipped to perform specialized repairs
and product modifications, e.g., butt-welding, bushing
replacements, code welding, and pilot replacement.
C. Maintenance Training
The rising costs of maintenance and repair in the utility and
process industries indicate the need for trained maintenance
personnel. BHGE conducts service seminars that help your
maintenance and engineering personnel reduce these costs.
Seminars, conducted either at your site or ours, provide
participants with an introduction to the basics of preventative
maintenance necessary to minimize downtime, reduce
unplanned repairs, and increase valve safety. While these
seminars do not create “instant experts,” they do provide the
participants with hands-on experience with Consolidated
valves. The seminar also includes valve terminology and
nomenclature, component inspection, troubleshooting,
setting, and testing with emphasis on the ASME Boiler and
Pressure Vessel Code.
For further information, please contact your local Green
Tag Center.